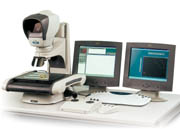
Trying to get a handle on industrial noncontact measurement requirements can be a bit like opening Pandora's Box. The challenge for many inspectors of plastic automotive, precision machined and other components is finding the right mix of solutions with the flexibility to perform a wide range of metrology tasks. Regardless of the task, inspectors are demanding the ability to obtain clear, high-definition images, as well as high-accuracy, repeatable measurement of complex manufactured components.
The answer to the age-old desire to examine multiple options in the hope of finding a single solution? According to Joe Michalek, production manager for Vision Engineering (New Milford, CT), it is optical microscope imaging technology. "We have seen a demand for optical technology combined with fully automated measurement capabilities. Users need a single modular and flexible solution to meet a wide range of measuring requirements."
The solution Michalek refers to is Vision Engineering's pioneering Hawk 3-Axis, fully automated, noncontact optical technology for fatigue-free, eyepieceless microscopes used in applications ranging from the rapid measurement of machined components to plastic automotive components to medical device components as well as molded tools used in their manufacture.
An enhanced image
The Hawk 3-Axis noncontact measuring system's Dynascope optical image technology uniquely provides for enhanced surface definition for fast and simple measurement of critical parts. "Most other systems use camera-based measurement. Numerous video-based measurement machines exist in the market today that are automated, but their drawback is when inspectors encounter that one part or feature that is difficult to image," Michalek says. "In those cases, they rely on the video monitor image to perform the measurements. With the advent of the Hawk, they can switch to the optical head to obtain a crisp, pure optical image of the part in order to make more precise measurements."
For example, automotive components today bring critical quality requirements in the areas of function, tolerance and aesthetic appearance. Increasingly, plastic components are replacing steel or aluminum, both in interior trim and mechanical components. While reducing overall weight and improving cosmetic finish, the trend demands that manufacturing criteria on plastic components equate with that of machined metal.
As automotive moldings become more complex and their quality more critical, consumers have become more demanding, thus driving the need for noncontact measurement systems that are accurate and capable of measuring optically challenging components in volume. Today's automotive moldings tend to be manufactured in dark, low-contrast colors-most frequently black, near-black and various shades of gray. While this is good for the car designer because the components coordinate well with the wide variety of color options in today's cars, it creates a challenge for inspectors needing accurate viewing and gaging.
"Whether we're talking about plastic molded gears, valves or other parts, especially white molded or colored plastic, inspectors face a notoriously difficult challenge when it comes to viewing and gaging surface definition because of the relatively poor contrast," Michalek explains. "Teeth on a gear, for example, are simple to pick up automatically, but you may have other features on that part such as blind holes or raised tabs on the surface that exhibit poor contrast. A video camera may not detect an edge in this case, whereas if you view it optically you can see it clearly."
This is because video-based systems tend to suffer when viewing the low-contrast black-on-black, white-on-white or transparent features seen on many automotive moldings. The human brain is by far the most powerful "technology" when it comes to difficult optical subjects. The Dynascope technology assists with viewing in that it presents a clear, pure optical image to the operator through an expanded exit pupil display head. The image does not experience loss of color clarity or contrast using the technology, whereas video-based systems make it difficult to view these low-contrast images typified by many automotive moldings.
Precision machined parts
The Hawk technology can be tailored for a range of system configuration options. In the area of precision machining, one application is the measuring and imaging of a black, highly light-absorbent, low-contrast plastic connector. In one case, the Hawk 3-axis, noncontact measurement system was used with a configuration that included a 150 x 150 millimeter high-accuracy quick-release stage; 2X and 10X objective lens magnification, with a magnification of 20X and 100X respectively; a 6-point ring light and epi-illumination; and QC5000 3-D Metrology Software.
The 150 by 150 millimeter stage provided accuracy better than
5 micrometers. 20X magnification used for diameter and radii measurement. The 100X magnification used for measuring 3-millimeter blind bores provided high magnification within the field of view and a depth of focus of 4 micrometers, allowing for accurate measurement in the Z-axis. The lens epi-illumination was used to illuminate the internal bore, while sub-stage illumination provided profile measurement. The metrology software allowed all the required geometric functions to be met, including advanced statistical reporting functions.
In general, the Hawk technology's measuring stage options include 150 by 150 millimeter (6 by 6 inch) and 200 by 150 millimeter (8 by 6 inch) stages, with factory-completed non-linear error correction calibration to ensure optimum accuracy and tracebility for the purposes of meeting ISO 9000 standards. The Hawk can be linked to external accessories such as a digital camera, video or closed-circuit TV.
"Because this technology combines both optical image display with fully automatic video edge detection, users avoid having to purchase dedicated equipment and, as a result, save in capital equipment investment. The real benefit, however, is the confidence users have in the measurements and data output from the system," Michalek says.