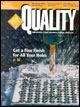
A traditional coordinate measuring machine (CMM) is more accurate than a noncontact optical system, but is slower and can't be used on soft or very small parts. A noncontact optical system can capture more data and do it more quickly than a CMM, even with very small parts, but it is not as accurate. Combining the two can speed up throughput and offer flexibility for measuring parts that are large or small, 2-D or 3-D, and hard or soft.
"The types of optical sensors that are used in certain applications, whether they are spot lasers, line lasers, or vision-type technology, are only a part of the solution," said Walter Pettigrew, vice president of LK Metrology Systems Inc. (Brighton, MI). "In most applications you have to use other technologies that go along with it, such as touch probes or scanning probes."
While not a large part of the overall CMM market, most, if not all, CMM manufacturers offer some type of multisensor system that includes such noncontact measuring devices as lasers, comparators and video. Conversely, manufacturers of vision equipment have begun to add tactile sensors to their equipment.
The two essentially different sensor technologies can switch between contact and noncontact sensors using probe changers or multiple heads. The CMM can be programmed to know when a traditional touch trigger probe should be used or when a part needs to be measured with a vision system. Complex mathematical algorithms can then correlate the disparate types of information. "There is a known relationship between the two different types of sensors that are used in unison to measure a single part," said Rich Knebel, director of software development for Carl Zeiss IMT Corp. (Minneapolis).
When using two sensors, each sensor should be qualified before use, said Freddy Hiatt, metrology systems division manager for L.S. Starrett Co. (Athol, MA) "With a touch probe you have to take a known reference and measure the reference to find the position of the sensor itself. The visual unit does basically the same thing except it uses a glass standard, rather than a physical standard, to locate it."
Getting better all the time
Incorporating multiple sensors on CMMs began with the electronics industry, as those manufacturers looked for ways to find small printed circuit boards on the CMM table. This mix and match technology came in use in the discrete manufacturing industry as parts started to be miniaturized. Its uses may continue to grow as part design becomes more complex and part surfaces become more multitextured, stepped and contoured. These types of parts have areas that are more suited to either touch or noncontact measurement; a traditional CMM can only measure what it can touch, and a vision system can measure only what it can see.
Adding sensors to a CMM is not a new concept. CMM manufacturers such as Carl Zeiss offered multisensor CMM products more than a decade ago, but the product did not take off. The CMM manufacturers said that the accuracy wasn't as good back then and the available offerings were difficult for the CMM makers to integrate.
"Years ago a vision company would develop a sensor and it would be an intelligent piece of hardware, but it was a stand-alone piece of hardware, and the CMM manufacturer would have to develop the interface and technology that surrounded it," said Pettigrew. "This made the integration of these probes a time-, cost- and risk-based issue. We not only had to integrate it, but we also had to learn about technology and build software applications to go along with it."
Today, vision companies are developing sensors that are packaged with built-in, value-added technology and software. Integrating the technology is easier and today some CMM makers call them plug-and-play technology.
"Vision technology went from telling if something was there, to doing some measurement to a machine that is dedicated to coordinate metrology," said David Genest, marketing director for Brown and Sharpe (North Kingstown, RI).
Despite advancements, CMM manufacturers said the accuracy of vision systems are not as high as a touch-trigger or scanning probe and this must be weighed against the benefits of flexibility. In general, optical sensors are not for extremely high accuracy applications. Camera-based optical systems are limited by pixels and resolutions of the camera image. And, while lasers are extremely accurate as a scale system, errors could creep in when using it as a sensor, depending on the part material. "Now, you are beholden to how the laser is bouncing off the part," said Knebel. "What is all that light doing as it reflects off the part?"
The earlier systems of vision and laser probes also were a little fragile, said Genest. "Putting all the guts inside a little box, spinning it around and using it 24 hours a day presented some problems early on, but a lot of those problems have been fixed," he said. "You can buy quite reliable lasers and vision probes."
A dedicated CMM or vision system will still offer better accuracy. "If I can design a machine around a touch probe with a certain lead stylus, it will be better than a machine with all different types of styli," said Pettigrew. "The more elements you try to package into a CMM, the more you sacrifice in your fringe areas."
What are they good for?
The true benefit of a multisensor system is the flexibility it offers. With these systems, parts that require tactile and vision measurements do not have to be moved from the CMM to the vision system. Companies that produce small or batch runs can benefit from this flexibility. A job shop, for example, might make transmission cases one day and then the next day have to fill an order for very small parts. With the multiple sensors, the company would not have to buy a complete vision machine to measure the 2-D parts.
"There is lot of versatility with these machines," said Hiatt. "Multisensor CMMs can be extremely beneficial for first article type inspection and small batch runs."
Another application is sheet metal or thinned wall products, said Hiatt. "If you've got stamped parts, and you don't have small enough sensors, visual application comes in extremely handy," he said.
Lasers also are good for larger sheet metal parts. For instance, a good laser application is on a horizontal-arm machine that is used in the measurement of sheet metal in automotive applications, said Genest. In this case, the tolerances for these contoured, complex shaped parts that require collecting lots of data points across the plane, are moderate. Because of this, an increase in measuring speed can be achieved. "You can now start to do very high speed gaging of sheet metal right in the assembly line," he said. "That is helping automakers out right now so they don't have to take the part out of the line. It can be done right in the production line."
The most obvious application is for parts that cannot be touched such as clay models, soft car seats and dashboards -- products that a company might consider buying a dedicated vision system to measure. "The question is, 'Why measure with a CMM if these are your applications,'" said Pettigrew. "But accuracy is not the only value that a CMM brings to table. It is automated, and it is flexible. You are not buying a CMM just for a particular part. As a product line for a company migrates or changes, the flexibility of this technology migrates with it."
When is too much, too much?
Theoretically, a CMM can be constructed with any and every type of sensor attached. It may not be practical from a financial or accuracy standpoint to do so, however. Depending on use, a dedicated system may be a more beneficial investment.
"Many times the sensor technology that you are trying to add to this CMM may only be 5% to 10% of the utilization of the ma-chine," said Pettigrew. "A lot of the effort is focused around that, which is a poor utilization, in my opinion, of a CMM. If you are looking for justification of adding a sensor to a CMM, then 40% to 50% of the utilization of the CMM should center around that technology. Then you are beginning to approach the kind of volume that might make that technology practical on the CMM."
A CMM manufacturer can estimate use by conducting a gage repeatability and reproducibility study. The supplier takes a series of parts and measures them a number of times to develop a statistical analysis of the level of uncertainty and compares that to the tolerance range. This level of uncertainty is a key issue to consider. A company's error budget, which is the uncertainty of the measurement caused by environmental and other effects on the machine, probe and part, is usually in the 10% to 20% range. "If you can add this technology to the CMM, stay within those ranges and still meet the production capabilities, then it is most certainly a good use of the technology," said Pettigrew.
Future applications
New noncontact technologies and applications are expected in the future for multisensor CMMs. Some of the possibilities include fracturing techniques to look at a surface finish. In this comparative application, a light shines on a surface-the rougher the surface, the more fractured the light. A smooth surface produces less fracturing. Also, eddy current-type probes that can look for flaws on a part are under development. This would be especially helpful in the aerospace industry, where microcracks are a major concern.
"The sensors will not only be dimensional controls, they will also begin to look at flaw detection," said Pettigrew.
Future applications for multisensor CMMs focus on sheet metal applications, as well as parts that have low to medium tolerance requirements, such as moldings.
"The molding industry is one of the biggest new markets that we have," said Genest. "Everything is made out of plastic, and the industry is getting larger. Being able to measure them with a noncontact probe is sort of untouched right now."
Whether a multisensor CMM is right for a particular company depends on the application, usage rates and error budgets. "Technology has moved along tremendously," said Pettigrew, "but it still boils down to whether you want to use specialized technology on a general machine or develop a specialized machine. Much of it is the balance of what the application is and whether there is a value there. In some cases there is; in some cases there isn't."