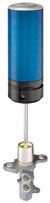
The new IPS-10 from Hommel-Etamic inspects surfaces in bores with a short inspection time and a high resolution. Source: Hommel-Etamic
Like many innovative products, the IPS-10 was in the works for a couple of years. As a result, the finished product offers a new way to do optical flaw detection.
Previously, optical flaw detection was generally done with line cameras or simply visual inspection, says Andy Blind, vice president, standards and marketing at Hommel-Etamic (Rochester Hills, MI).
For those who would like to do this type of measurement of bores, it would require a high-precision rotary device, or what Hommel-Etamic came up with, which was basically the ability to scan 360 degrees, Blind says.
“It really revolves around our optical surface capabilities,” he adds.
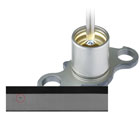
A 360-degree panoramic view optic creates an image of the inside surface of the bore. Source: Hommel-Etamic
How It Works
The 360-degree optical sensor inspects bore surfaces and provides automated in-line part inspection of bores, such as those found in connecting rods, brake master cylinders, injection system components and hydraulic valves that cannot tolerate surface finish defects.Consisting of an optical sensor, computer and a slide to position the sensor, the IPS-10 internal inspection system can be installed within a production line to inspect bores with a diameter of 14 to 50 millimeters and depths to 450 millimeters. Typical cycle times are only seconds per part to produce a complete optical inspection of a bore’s inside surface.
A 360-degree panoramic view optical system inserted into the bore creates an image of the bore’s inside surface. Circumferential lines in the bore are projected in circular lines in the image plane. This image is scanned continuously by a CMOS ring sensor array. Simultaneous forward movement of the inspection sensor and circular scanning creates an undistorted image of the inside surface that shows a rolled-out representation. Identical illumination conditions at every point produce rich-contrast images. The optimum illumination and scanning speed of the camera make this inspection system a good solution.
Hommel-Etamic first showed the system concept at the Control show in 2006. By 2007, they had several installations in place and demonstrated a working version of the product. They also showcased it at this year’s Control show in Stuttgart, Germany.
Previously this type of inspection required the manual labor of a borescope, or sitting in front of videoscreens.
Parts to be inspected must have a clean, dry surface in order to use this optical inspection method, according to the company. The system detects surface flaws such as cavities, scratches, porosity, valleys, edge flaws and unmachined surfaces fully automatically. The completeness and position of transverse holes and grooves also is possible in the same step.
The company will examine a customer’s application and recommend the technology if it is a good fit. The optical sensor can only pick up what can be seen on the surface, Blind says, so for cracks hidden below the surface, technologies such as tomography or eddy current would be better able to pick up the defects.
The price of IPS-10 depends on how it is packaged. For an OEM system, it would come with evaluation software, a frame grabber and controller, along with an industrial PC. A complete system starts in the low $100,000 range. While this initial cost may seem high, Blind points out that compared to the cost of labor for two shifts, with two operators per shift, the product can yield significant savings.
“A lot of people have been searching for a solution for a long time,” Blind says, and they have been responding to the product. A customer in Spain bought one, and another one and another one, Blind says, for a total of five.
“They loved the idea of incorporating it into their own production lines, and they don’t have to do a lot of automation,” Blind says.
While the product has already been met with success, Blind points out it is still in its early stages, with more applications being discovered for the product.
“People ask about potential applications such as surfaces on steering rods that they previously were not able to check,” Blind says. “With the technology of the IPS-10, they can implement an effective check.”
Software
The software itself is another asset. While an innovative sensor is one thing, the system would not be complete without the powerful software.The sensor can scan the bore with good resolution and get a 360-degree image of the surface, but simply having an image does not give all the capabilities needed to see the surfaces. Features have to be recognized by the software. Grooves may not be errors, as the surfaces are complex, Blind says.
“We work together with the customer to determine what is an error and what isn’t,” says Blind. The software also allows the companies to determine tolerances for each zone, some of which may be more critical than others, and to tell the system to look out for defects.
Technology Contact
For more information on the IPS-10, contact:- Hommel-Etamic America Corp.
1505 West Hamlin Rd.
Rochester Hills, MI 48309
(248) 853-5888
[email protected]
www.hommel-etamic.com