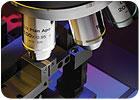
Turret-mounted objectives allow rapid magnification change while keeping the area of interest at each magnification within the field of view. Source: View Micro-Metrology
Optical measurement encompasses a broad category of technology that measures by imaging. Optical measurement involves the use of an optical system to relay an image of something so that image can be analyzed to derive measurements of a parameter of interest. Typically, the optical system magnifies the image to improve the ability to resolve detail.
What is measured and to what resolution can vary dramatically within the realm of optical measurement. One extreme is the telescope measuring distances between stars in light years. Then there are satellites mapping features on the Earth’s surface to a few meters. At the other extreme are high-magnification microscopes measuring a plethora of biological and industrial features. All of these devices perform optical measurement.
Manual vs. Automated Measurement
Optical measurement is different from measurement of optics. For a company that manufactures lenses, optical measurement usually means evaluating the optical quality of lenses and lens systems. For example, lens specifications typically include surface form, or variations in surface shape from that which is desired; transmitted wavefront quality, or how much the lens distorts an image; and defects such as scratch and dig. Many of these specifications are verified with interferometers and other optics-based technologies. This could be called the optical measurement of optics.Every type of optical measurement involves optics as the measurement medium. In manufacturing and research and development (R&D), one key advantage of optical measurement is that it is noncontact. Optics image a surface without physical contact with that surface. This has obvious benefits for any part that might be damaged or deformed by physical contact.
Optical measurement for quality control covers a range of variations. In a simple manual case, an inspector can look into an eyepiece of an optical system that includes a reticle, or scale. The operator positions a part and reads a dimension off the scale as a measurement. That can be called manual optical measurement.
At the other end is the automation spectrum, in which an optical system moves a part into position, focuses, analyzes the image and takes its next action based on the results of that analysis automatically, without any operator involvement. That can be called automated optical measurement. There is a continuum of optical measurement systems with capabilities between these extremes.

A dual magnification optical system with two sets of imaging optics and cameras can change magnification almost instantaneously. Source: View Micro-Metrology
Sort Out Terminology
Many optical measurement systems bear the names of their subcategories, which leads to confusion. Sometimes these subcategories are based on characteristics of the system.As an example, a video measurement system is an optical measurement system that uses video camera technology. Such a system uses optical imaging. It measures by analyzing characteristics of the image relayed by optics to a camera. Calling it a video measurement system helps categorize it within the umbrella term optical measurement.
Even among subcategories confusion can persist. There are video systems and vision systems, for example. Both types of systems perform optical measurements. Both use lenses and cameras. The distinction between the two is not hard and fast, but, in general, parts are brought to a video system while a vision system inspects parts as they are conveyed within a manufacturing process.
Lens Selection
No matter what is being measured, there is a direct relationship between the optical quality of the imaging system and the accuracy of the measurement. Lens systems have aberrations. A perfect lens system would faithfully recreate an image of a part with all distances to actual proportion.Among the range of aberrations, astigmatism is a condition in which a surface with horizontal features will focus in a different plane than a surface with vertical features. Distortion is a condition in which a line projected through the lens will vary in straightness and spacing as it is imaged at distances away from the center of the field of view. The magnitude of lens aberrations can be large enough to affect measurements. So it goes without saying: better optics provide better images, increasing the likelihood of higher accuracy measurements.
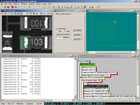
Metrology software measures a large number of parameters automatically.
Source: View Micro-Metrology
Magnification Methods
Although many measurements can be made at one magnification, a versatile optical measurement system will measure at more than one magnification. Finding a measurement area directly at a high magnification can be a frustrating and tedious process. Instead, an area of interest can be found at a low magnification covering a large imaging area. A particular area within that larger area can be imaged for measurement at a higher magnification.Technically, any magnification change has the same requirement-the area of interest being imaged should be in the same optical field of view when the magnification is changed. There are a number of ways of providing that capability.
One method is the turret of objectives. Its accurate detent positions allow different magnification objectives to be rotated into position with each imaging larger or smaller fields of view of the same position on a part. Turrets can be manually rotated or motorized for automatic operation.
Another method of magnification change is a dual magnification configuration. In such a system there are two lens systems and two cameras. The part imaging optics are common so the area of interest is centered for each imaging system. The camera imaging optics have different magnifications. In addition, the size of the camera detector can be different for the two cameras, offering yet another method of varying magnification. In such a system, the magnification change between the two systems can be nearly instantaneous.
Finally there is the zoom lens. It can provide a range of magnifications through a common lens system.
An optical measurement system is more than the sum of all its parts. There are serious engineering considerations that ultimately affect measurement performance. No matter what the specifications of the individual components, correct system integration determines the ultimate capabilities, performance and reliability.
Optical measurement is widely used in quality processes across diverse industries. It expands the range of human imaging and quantifies details in images to provide highly accurate measurements. With tighter and tighter manufacturing tolerances, many of today’s most advanced products would not exist without optical measurement.