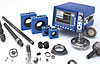
Eddy current can be easily integrated into production lines, used in an offline test cell or even as an audit tester in the quality lab. Source: Uson
There must be a good number of quality managers and subordinates who have either lost sleep, used their precious weekend hours-or both-agonizing over and working to correct or recover from a product quality problem. If they are lucky, they will catch the problem before it gets out the door. Otherwise, the quality managers should be prepared to deal with one or more irate customers.
Product quality ranks in the top two when spending money on high-ticket items such as the latest big screen LCD TV or automobile. Most consumers talk with people, do research online or read magazines looking for information on those items that have made their “short list” in order to make sure that they are comfortable with not only the performance, but also the product quality before making a purchase.
The quality of today’s high- performance workhorses-cars, trucks and industrial machinery-fortunately is not left to chance, but involves some highly educated decisions from concept through production.
When talking about engines, the job of the product engineer is to create a quality product. The engine will contain a multitude of internal components, each of which will have been carefully designed. And it is during the design and manufacturing processes where the engineer must use his training to ensure each of the components will result in a product that meets or exceeds the reliability and product longevity, or final product quality, required.
This is not to say that all final product quality rests on the shoulders of a design engineer. There are many other factors and processes involved that are out of their hands. On the road to production, all steps taken have equally important roles to play in terms of product quality. If one step is missed or not followed through, a weak link is created. This is especially true during the manufacturing process. It does not matter if the end product is a $10 can opener or a $10,000 high-performance engine. If one weak link exists within, rest assured of Murphy’s Law. Then the question is, “How will you reliably locate and remove this weak link from thousands of manufactured parts?”
Design starts first with the evaluation of a need, which then turns into a concept and design phase. Many things are taken into consideration at this point, one of which is the type of material to be selected for the component. When the material is a metal, it is extremely important to select both the right type of metal for the job and the correct material processing. This will ensure that the metal’s performance will meet the design requirements in terms of function and durability, or component quality.
One of the difficulties in manufacturing is identifying the missteps in a process. In some cases it is obvious where a casting, forging or machining error occurred. There are other processes, however, where an error is not so obvious. One such area is in the heat treatment of metals.
There are many types of heat treatment processes. In all cases, without proper heat treatment the material can be too soft or too brittle, which can result in premature failure of the component. Some examples or problems that can occur because of operator error, failure of system tooling or production cycle errors are:
- Non-heat treated part gets mixed in with good processed parts.
- Air-cooled parts.
- Short-cycled parts (short heat, short quench).
- Excessively heated parts due to increased temperature or heat time.
- Delayed quench due to a process interruption.
- Misplaced case pattern (induction hardening), which can occur from bent induction coils or misalignment of tooling.
The traditional method of capturing these conditions has been by batch testing. One or more parts are collected and destructively analyzed in a quality lab to verify correct heat treatment. The problem with this method is that it can often result in excessive scrap material because parts continue to be made out on the production line. It then becomes difficult and time consuming to identify and quarantine all of the affected parts when hundreds or thousands of parts per hour are being produced, or the search and destroy quality mentality. The real key to manufactured component quality is to evaluate each part as it is being produced and kick it out right away.

Eddy current testing can be considered for use on any material that is conductive or can support electrical current flow. Source: Uson
Even slight changes in the material conductivity from production process variations have an effect on how the eddy currents flow within. The test instrument then detects these slight changes and makes a determination on the product’s quality based on previously established test limits.
Eddy current is a clean, fast, reliable and repeatable test method. It is capable of testing products at production line speeds. It does not get tired or provide subjective results like other manual inspection methods. It can be easily integrated into production lines, used in an offline test cell or even as an audit tester in the quality lab.
Take a close look at how a company is catching the occasional rejectable component-or not. Maybe eddy current can help the quality managers get that extra sleep that they have been missing.
Joe Jessop is the component testing business manager at Uson L.P. (Snoqualmie, WA). For more information, call (425) 974-2901, e-mail [email protected] or visit www.uson.com.