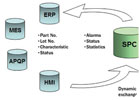
Remember the first time in school you used a calculator instead of paper and pencil to add, subtract, multiply or divide? It made the job so easy, it almost felt like cheating. The technology freed you to focus on the problem rather than the mechanics of arithmetic.
Statistical process control (SPC) methods have been applied in manufacturing process control since the early 1930s. Over the decades, countless hours were expended plotting charts with pencils on graph paper. Then computers arrived and, like the calculator did for the schoolboy, freed the engineer to spend time analyzing the process instead of focusing on the formulae.
Over the years SPC software has matured in functionality, making statistical analysis quicker, more powerful and more flexible. The driving force has made the software easier for the practitioner to use. SPC software will continue to develop in ways that eliminate unnecessary steps, freeing quality practitioners from rote tasks and enabling them to focus efforts on improving the manufacturing process.
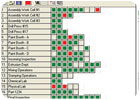
The past
As access to computers in the manufacturing environment grew, along came the first wave of products that automated the tasks associated with statistical analysis. Although they provided the tools for engineers to analyze the manufacturing process, these systems were difficult for many practitioners to use. They required tedious data entry and a Ph.D. statistician's knowledge to configure the software and analyze the data-a combination of tasks and abilities not easily married. Furthermore, obtaining interpretable results was a process completed long after the production run being analyzed had finished. This delay complicated the task of addressing process problems that continued to change-and probably resulted in additional process variation-in the interim.Many timesaving features have since been added to advance SPC software usability. These software systems leverage other technologies such as automation standards and Internet access to simplify and integrate tasks-making administration, data collection, statistical analysis and reporting easier for today's practitioners.
Administration and data collection
Today's SPC software is designed to make the setup of parts and processes easy to accomplish. Common graphical user interface features such as tree views with drag-and-drop functionality dominate the market. These features reduce the repetitive tasks of separately creating items with only minor differences and instead allow for copying and duplicating similar components and then assigning unique parameters.The introduction of communication standards across various platforms takes this ease-of-administration approach even further. Now SPC software can be configured to automatically obtain and update parts, processes, specifications, nominals and other pertinent information from values stored in other enterprise software systems such as manufacturing resource planning, manufacturing execution systems and human machine interface. Not only does this eliminate the effort spent re-entering and updating configuration information in multiple packages, it saves the effort expended tracking down entry errors that occur when the process is done manually.
Today's SPC software can automatically collect data from other enterprise software systems. As with the time-saving benefit for administrative tasks, this capability reduces the need to configure and maintain separate data collection interfaces and eliminates re-entry errors.
Current SPC software also has used communication standards to simplify the time-consuming job of connecting the system to data collection devices. Advances in software masking functionality permit out-of-the-box connection to a wide range of digital devices. And with dynamic masking capabilities, SPC software can automatically react to changes in device output and adjust to collect the specified data. This flexibility frees the practitioner from the tedious chore of administering SPC software every time there is a change to a device's output.
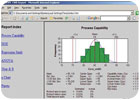
Real-time analysis
Today's SPC software products are designed to collect data, produce charts and alarm in real time. This enables shop-floor operators to receive statistical feedback as close as possible to the point of production. Alarming capabilities include notification of supervisors, managers and other personnel responsible for maintaining and improving the production process. Immediate feedback and alarming enable all parties to begin problem solving and root causes analysis immediately. Eliminating the delay between a special cause and detection can reduce the investigation and corrective action effort by empowering quality practitioners with useful production feedback at the moment of a problem's inception.Current development in SPC software includes the ability to provide supervisors with dashboard-style status indicators of all collection operations in the plant. Snapshot views of production status on a single screen allow busy supervisors to manage by exception instead of manage by walking around. Such SPC software systems aggregate and prioritize production information for the supervisor, reducing data-gathering demands.
Reporting
One of the most time-consuming tasks in applying statistical methods to a manufacturing process is developing relevant and understandable reports to form the basis for decision making. Modern SPC software makes the job easier by providing built-in report templates that can organize and deliver reports focused on the key characteristics of a process. Moreover, reports that are needed on a regular basis can be scheduled and automatically generated based on then-current production information. This is a time saver for those responsible for communication among quality team members.Finally, the effort previously expended producing and distributing charts to various users and locations is reduced by leveraging the Internet. A Web-based SPC report with hyperlinks to various types of analyses can easily be distributed to multiple persons, teams or facilities.
The future
Future SPC software development will follow the trend to eliminate cumbersome, low-value tasks and generally make SPC systems easier to administer and use. Describing the particular form such future development will take is speculative, but here is one possible way SPC software could evolve to address new challenges.It may not be until the 24th century when Star Trek's android, Data, is seen on each quality team to provide statistical analysis of the manufacturing process. But the precursor to his arrival can already be seen in the combined capabilities of intelligent and expert systems. Intelligent systems emulate the human ability to learn from past experience and to make reasoned decisions and take action based on those experiences. Expert systems rely on a knowledge base to build models to diagnose, advise and act on real-world problems. Intelligent and expert systems are already deployed in control technology for manufacturing processes. It is not a great leap to believe that these technologies will profoundly change the nature of SPC software.
There are many ways in which intelligent and expert SPC systems would enhance the effectiveness and simplify the work of quality practitioners. On the most superficial level, these systems would learn from previous SPC configuration to logically reorder the system to make future administration easier. For instance, such systems could recognize which devices are being deployed and suggest effective collection methods and preferred connection approaches based on past experience.
But the administrative assistance offered by intelligent and expert SPC systems would run much deeper than that. Such systems could save countless hours helping determine how to monitor the process. Building on the history of previous production successes and failures, SPC software could select key parameters to track when to set up new parts or processes, and determine the most effective way to chart and report on those parameters. The software itself could anticipate problems and alter monitoring methodologies to adapt to changes in the manufacturing process.
The impact of intelligent and expert systems would perhaps be greatest when it comes to interpreting process statistics and acting on that analysis. There is not enough time in the day for the quality practitioner to thoroughly analyze the mountain of information generated from each production run. SPC software with learning and knowledge-based capabilities, coupled with computational power, will provide insights into the process beyond what the practitioner alone could achieve. With the advent of intelligent and expert SPC systems, the computer can transcend the earlier comparison made to a calculator. Such systems could not only assume or simplify menial tasks currently performed by the quality practitioner, but will also become a readily available and trusted source of expert guidance and advice.
Of course, the future developments suggested here may never come to pass. Nonetheless, it is almost a foregone conclusion that the SPC software of tomorrow will be more intelligent and capable of simplifying many jobs that burden today's quality practitioner. The future of SPC software is what frees those practitioners from time-consuming, low-value tasks and enables them to more easily obtain the analytical results that inform business decisions.
Frank Tappen is the director of solution delivery at DataNet Quality Systems (Southfield, MI).
Beena Anand is the WinSPC trainer at DataNet Quality Systems. They can be reached at [email protected] and [email protected]. For more information, call (248) 447-0117 or visit www.winspc.com.
Quality Tech tips
- Over the years SPC software has matured in functionality, making statistical analysis quicker, more powerful and more flexible.
- Now SPC software can be configured to automatically obtain and update parts, processes, specifications, nominals and other pertinent information from values stored in other enterprise software systems.
- Building on the history of previous production successes and failures, SPC software could select key parameters to track when to set up new parts or processes and determine the most effective way to chart and report on those parameters.