Manufacturers with global operations also rely on SOPs to standardize processes in all of their facilities. For example, a Japanese automotive company will train its personnel in the United States on key manufacturing processes and then use SOPs to make sure that high quality is reflected in every car sold by the company, regardless of where it was assembled.
There are many other reasons why organizations use SOPs, including:
• To ensure consistent, repeatable processes
• To facilitate training by giving trainees a point of reference
• To facilitate cross-training of employees on tasks they do not normally perform, such as when they need to substitute for vacationing or sick coworkers
• To reduce safety risks and other hazards by specifying how to avoid and prevent them
• To have a basis for evaluation and improvement of processes
• To comply with regulations and quality standards.
Regulations and Standards
The last reason-compliance with regulations and quality standards-is a key factor that drives many organizations to establish and maintain SOPs. In FDA and ISO environments, the concept of quality is made tangible by the information and processes captured in SOPs, and correct implementation of those SOPs helps ensure quality.FDA’s Current Good Manufacturing Practice (CGMP) regulations for finished pharmaceuticals (21 CFR Parts 210-211) require written procedures for production and process control to ensure that products have the identity, strength, quality and purity they purport to possess (Section 211.100). These written procedures, including any changes, must be reviewed and approved by the quality control unit.
CGMP regulations for blood and blood components (21 CFR 606) state that “written operating procedures shall be maintained and shall include all steps to be followed in the collection, processing, compatibility testing, storage, and distribution of blood and blood components for transfusion and further manufacturing purposes” (Section 606.100b).
The Quality System Regulation (21 CFR Part 820) for medical devices similarly requires SOPs and documented instructions that define and control the manner of production (Section 820.70).
Manufacturers and other organizations that adhere to quality standards developed by the International Organization for Standardization (ISO) face similar requirements.
ISO 9001: 2000 and ISO 13485: 2003, widely used throughout the world, require companies to document their procedures, describe how those processes interact and develop documents for implementation of the quality system. Compliance with ISO standards is voluntary, although certain countries require ISO certification and many customers prefer vendors and suppliers that are ISO-certified.
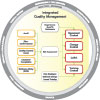
Types of SOPs
SOP formats are as varied as business operations. An SOP may come in the form of a checklist, a linear flowchart or some other type of flowchart, hierarchical steps or annotated photos.Neither the FDA nor ISO require any specific SOP formats. In general, however, SOPs in regulated environments are expected to be consistent and traceable. They should provide document identification and facilitate control.
To be effective, an SOP should include company name, a descriptive SOP title, identification and control numbers, purpose, scope, responsibilities involved-specific tasks, who is performing what, certification and qualification requirements-and step-by-step procedures. Depending on the nature of the process being described, the SOP may include calculations for data handling.
SOPs are usually categorized by procedure type, such as design, manufacturing or quality assurance. Categories help determine the correct format for each SOP and also facilitate appropriate review and approval for the document.
Challenges
Despite the much ballyhooed “information age” and “computer revolution,” most companies continue to rely on paper-based processes. Typically, SOPs are created using Microsoft Word, printed out and stored in three-ring binders. The binders are then routed physically from one approver to the next. After approval, the contents of the binder are photocopied so every affected department will have one binder handy.For a small organization, this process may be just fine. But for most companies, a manual system poses many challenges, including:
• Inefficiency. The process of routing, reviewing and approving an SOP can be slow and inefficient. This is particularly true if an organization generates hundreds or thousands of SOPs, and the people who need to review and approve them are in different locations or out of the office. It is likely that SOPs may get lost while being routed, either buried in someone’s messy desk or computer in box. Search and retrieval of SOPs entails sorting through voluminous paperwork. Updating SOPs is equally slow. In addition to going through the same routing and approval process during revision, obsolete paper documents must be purged.
• Poor communication. In a manual system, quality processes are not connected, making it hard for people who operate those processes to communicate. To speed up the approval of an SOP, the originator needs to make phone calls, send e-mails or remind approvers in person-and that is just one SOP. Multiply the number of phone, e-mail and personal reminders a dozen times for an employee responsible for a dozen SOPs. In a fast-paced organization, SOPs are likely to change constantly, but people affected by the changes may not be notified in a timely manner.
• Lack of training. It is bad enough that employees are not notified about new or revised SOPs in a timely manner, but it is worse when they do not get the appropriate training on the new SOPs. This failure to keep up with training on new SOPs is inherent in a manual system that is not connected to the training control process. So, employees may be using new SOPs, but they may be doing it poorly without the appropriate training.
• Ineffective documentation. Effective implementation of SOPs has a direct impact on product quality; that is why it is critical for organizations to capture accurate and up-to-date information in SOPs. But it takes a lot of time and effort to manually update SOPs, so employees may sit on updates, jeopardizing conformance. It is equally difficult to rely on employees to always remember to document any changes in an SOP, including who made the change, why and when.
• Poor revision control. Companies that rely on a manual system often complain that it is difficult to get rid of obsolete documents. Even after SOPs have been revised and approved, old documents may resurface on the shop floor. Another problem is that employees may use documents that have not been approved simply because they are able to grab that binder sitting on someone’s desk. In both cases, using uncontrolled SOPs could lead to nonconformance.
• Poor collaboration. Creating and updating SOPs usually requires collaboration. For organizations that use manual processes, collaboration would entail face-to-face meetings and passing around a document that employees take turns editing. This manual process works when there are few collaborators who are based in the same facility and whose schedules are similar. But collaboration among employees with varied schedules and responsibilities and who are based in different facilities is practically impossible.
• Lack of visibility. Paper-based processes are not connected, making it difficult for management to monitor the effectiveness of SOPs and make timely decisions. For example, if the customer complaint process is not connected to either corrective and preventive action (CAPA) or change control, it may take a while before management realizes that a certain complaint should have been escalated to CAPA and should have resulted in a change in a manufacturing SOP, perhaps preventing a product recall.
Solutions
A quality management suite should consist of configurable, easy-to-use and integrated applications for automating, streamlining and effectively managing SOPs and other documents, change control, training control, audits, CAPA, customer complaints and other forms-based quality and business processes under a single Web-based platform.To address manual-based challenges, an automated system can provide a variety of solutions including:
• Efficient system. A Web-based system can automate routing, delivery and storage of SOPs, thereby increasing the efficiency of SOP management. The system provides a secure, centralized repository that makes search and retrieval easy. SOPs will not get lost because the system can track every document’s exact location.
• Effective communication. Automatic follow-up helps improve efficiency. The system will continue to send notifications until the person acts on an SOP. It incorporates escalation, so if the person is unavailable for a period of time, the SOP will move to the next person authorized to approve it. A Web-based platform may allow offsite or traveling employees to participate in the review and approval process through the Internet. Even suppliers, consultants and other third parties may be given limited access to the system so they can be immediately notified upon approval of changes to SOPs that affect them. As an alternative, external links can be created to make selected documents and processes available without giving them system access.
• Integrated training. By integrating training control with SOP management and other quality processes, all employees affected by new or revised SOPs will be automatically sent training tasks. Some systems automate assignment, monitoring and verification of training tasks. The system also may automate grading of online exams. It allows implementation of a progressive training program by sequencing training courses. After a prerequisite is completed, the next course is automatically launched.
• Effective documentation. An automated system makes it easier to keep SOPs accurate and current. To update or revise documents, there is only one place to make a change because all SOPs will be stored in a centralized, Web-based repository that can be accessed by authorized users from virtually anywhere. There is no need for employees to remember to document changes because the system provides a time-stamped audit trail that captures the identity of anyone who creates, views or changes an electronic record, when the action occurred, and the changes made. Along with the stamp, users are asked to enter a reason for every change.
• Automatic revision control. Employees will no longer use uncontrolled SOPs because only approved documents will be released and made available to them. Obsolete SOPs will not resurface. With an automated system, when an SOP is revised, the original version is automatically archived on approval and release of the revision. Also, setting an expiration date will make an SOP obsolete on that date and it will automatically be archived. Automatic revision control will ensure that when an SOP is being revised, it will not be available for check out until approval of the revision.
• Improved collaboration. A virtual collaboration workspace allows individuals to participate at their convenience. They can review, comment on, revise or approve an SOP without having to be physically present with the rest of the team. A Web-based platform allows even off-site or traveling employees to collaborate.
• Increased visibility. An automated system can make the entire quality system visible by integrating different processes and connecting different departments. Management will be able to monitor the effectiveness of SOPs in a single, integrated system better than in separate processes.
For FDA-regulated and ISO- certified companies, SOPs are more than just a tool of operation. SOPs directly affect product quality, and therefore, compliance. Development of effective SOPs and implementing them correctly require commitment from the entire organization. Choosing the right software solution that will facilitate and improve SOP management should be a part of this commitment. Once established, an efficient and effective SOP management system will serve as a foundation for an organization’s sustainable compliance and long-term success in the market. Q
Tech Tips
• SOPs, in conjunction with personnel training, help relay knowledge from one department to another.• Manufacturers with global operations also rely on SOPs to standardize processes in all of their facilities.
• Compliance with regulations and quality standards is a key factor that drives many organizations to establish and maintain SOPs.
• In FDA and ISO environments, the concept of quality is made tangible by the information and processes captured in SOPs, and correct implementation of those SOPs helps ensure quality.
• An SOP may come in the form of a checklist, a linear flowchart or some other type of flowchart, hierarchical steps or annotated photos.