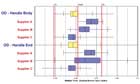
The Rising Dependence on Supply Chain Quality
Recalls are costing businesses billions of dollars annually, and manufacturers simply cannot afford to gamble with quality control. When manufacturers rely so heavily on the supply chain to deliver quality materials, measuring and controlling these products in real-time, before they are purchased and shipped becomes imperative.As the supply chain is playing an increasingly prominent role in business vitality, manufacturers have been incorporating supplier rating systems that provide greater transparency into their quality records. While some organizations rely strictly upon supplier certificates of analysis (COA’s) or some internal supplier rating score to manage their suppliers, there is often a discrepancy with the actual findings at incoming inspection. While incoming inspections can usually detect problems before additional steps occur, they are time-consuming, costly, and performed after-the-fact.
A much more efficient way of managing supplier quality is to do so while the products are being manufactured on the supplier’s plant floor. Using collaborative technology to facilitate the communication and share data in real-time, manufacturers and their suppliers can work together to ensure that the products meet specifications prior to being purchased and delivered. Additionally, when working with multiple suppliers of the same product, manufacturers who have access to supplier quality data can evaluate the various vendors and can scientifically determine the highest quality suppliers.
The Shift to Supply Chain Collaboration
Investing the time and money on stringent quality control procedures and standards internally will only go so far in preventing defects from supplied products. If supplied materials and components are not meeting standards and are being sent back, or actually incorporated into the final product, even the most capable manufacturing facilities are operating inefficiently.When manufacturers and their suppliers apply the scientific methodology of real-time Statistical Process Control (SPC), manufacturers can methodically improve the quality of incoming materials. By collecting and analyzing supplier shop floor data in real-time – and by receiving instant alarms – manufacturers have the ability to collaborate with their suppliers to immediately help them identify and resolve quality issues before they become quality problems.
Forward-thinking manufacturers realize that the supply chain is playing an increasingly prominent role in business vitality and have incorporated modern technologies into their quality management strategy.
Case Study: Quickie Manufacturing
Quickie Manufacturing, the nation’s largest manufacturer of cleaning tools, relies almost exclusively on outside suppliers, many of which overseas, to provide the components that are assembled into finished goods at Quickie’s manufacturing plants. Quickie has over one hundred suppliers and the quality of their products is directly dependent upon the quality of the materials provided by them. Quickie needed to implement a system to monitor and manage their suppliers’ quality - all the way down to the shop floor - as the products were being manufactured.Quickie has begun to implement a solution with its suppliers to enable the sharing of real-time quality data and improve supply chain performance. Developed by SPC software provider InfinityQS, this technology collects raw shop floor data from multiple suppliers into a centralized database, and then applies proven statistical methods for quality control to the data for thorough, real-time analysis. The solution, called “eSPC”, is the next generation of InfinityQS’ shop-floor SPC software that is currently installed in over 2,000 manufacturing facilities worldwide.
For Quickie Manufacturing, the goal is to improve supplier quality. “It’s particularly critical to identify problems that are caused by a breakdown in manufacturing process control up front rather than at the tail end of the process-after they’ve already produced hundreds of products and packaged and shipped them, ” says Dan Romano at Quickie Manufacturing.
Quickie realized benefits within just a few weeks of the eSPC implementation. Quickie now has instantaneous access to lot quality, supplier-to-supplier comparisons, lot-to-lot comparisons, and lot verification. The eSPC system also sends real-time alarms to alert Quickie of potential issues so that Quickie can work with their suppliers to resolve them before they become problematic. This instant access to global quality records drastically reduces the risk of receiving defective lots and allows Quickie to implement incentive programs that reward the better suppliers and reduce the costs of working with poor performing suppliers.
Learn more about Supply Chain Quality Management by attending a free Webinar. Call 1-800-772-7978 for Webinar times and dates, and be sure to mention the “How-To-Guide”.