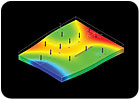
Finite Element Analysis shows an exaggerated view of distortion in granite components. The red area shows less than a 2 micron deflection. Source: Starrett
With the metrology industry’s seemingly boundless quest for ultra high accuracy and sophisticated designs, the question is begged, how much accuracy is absolutely necessary and at what cost? Fortunately, recent advancements in video measuring equipment design provide accurate, productive, cost-effective solutions that are well within the vast majority of even the most stringent metrology requirements.
The common drivers of today’s requirements include miniaturization, high volume, increased accuracy and 3-D measurement. These are some of the buzzwords being heard more frequently in the metrology business-and they dictate the capabilities that are being designed into today’s video and multisensor measurement systems. However, one of the obvious factors, particularly in challenging economic times, is lower cost.
While the cost factor may seem to be at odds among the other drivers, there are design enhancements that are being incorporated into larger travel systems that come virtually free of charge. In addition, component manufacturers are receiving the same pressure to increase performance while decreasing cost.
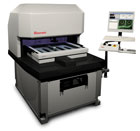
Recent advancements in video measuring equipment design provide accurate, productive, cost-effective solutions that are well within the vast majority of even the most stringent metrology requirements. Source: Starrett
Optimizing Design, Reducing Cost
Nothing demonstrates component optimization at reduced cost better than the changes in the linear encoder industry. Virtually all precision measurement systems use linear encoders to monitor the position of their stages in closed-loop configurations.In a manual machine this simply means that the operator positions the stage to the desired coordinates as displayed on the digital read-out (DRO). A computer numerically controlled (CNC) system would direct a stepper, servo or linear motor drive system to position the transport using various voltage, current and frequency variables but would adjust and confirm the final position by referencing the linear encoder.
In years past most encoders were primarily constructed of glass, housed in aluminum spars and anchored to the machine on two standoffs. While this type of scale is still common, some system designers have switched to adhesive backed “tape” scales. These are as accurate as the glass scales, and in many cases more so, as they can be directly affixed to the structure of the machine-which is often granite. Moreover, they are more immune to damage and misalignment and can be much less expensive than their glass counterparts.
This is just one example of purchased component optimization that improves performance while decreasing costs.
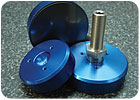
Porous carbon air bearings provide quiet, frictionless motion and require no lubrication or maintenance. Source: Starrett
The most obvious advantage on a measuring machine relates to the design of the granite base-plate and bearing ways. The bulk of the cost on these items is confined to their precision flatness and squareness. FEA allows the completed structure to be synthetically driven and the resultant distortion to be displayed and analyzed in a range of modes. Small modifications to the support structure often can result in a dramatic decrease in the thickness, weight and cost of the structure.
Computer-aided design (CAD) offers another advantage with the advent of parametric modeling. This capability retains the relationship of specific entities so that design changes can be accomplished quickly and with less likelihood for error. This makes scaling of subassemblies possible and with that, the efficient expansion of a given line of measurement systems.

A massive granite base and bridge provide mechanical and thermal stability. Source: Starrett
Video, laser and touch probes can all be integrated into one multisensor system with the tools identified above. The interaction of these devices can be plotted, studied and stored. Magnifications can be increased, accuracies can be improved and resolution can be enhanced using these techniques. Expect to see a focus on the volumetric measurement and compensation characteristics of these machines as they are exposed to a wider variety of applications and with more emphasis on 3-D accuracy. Multisensor systems are ideal for complex, multi-featured parts that may require noncontact, contact and 3-D probing measuring routines.
With increasing magnification, vibration isolation will become more important as systems exceed 1,000X, and expect to see accuracy and repeatability figures in the near future that rival machines of the highest caliber at a fraction of the cost. Modern measurement machines map the inherent errors in the operating envelope and store the correction data in a lookup file. These corrections are applied at machine start-up and require no operator intervention. In addition, periodic re-calibrations can be accomplished quickly, efficiently should the machine warrant it.
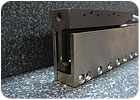
Ironless core linear motors provide high speed, smooth precision motion and require no lubrication or maintenance. Source: Starrett
Design Examples
Let’s look at some examples of design optimization for longer travel systems. Some systems utilize ball screw drive systems. They can be noisy, expensive, maintenance prone and difficult to install properly. They also are slow compared to competing technologies. The leader in drive systems is the linear motor drive which offers nearly silent operation and zero maintenance. When coupled with an air-bearing stage and noncontact linear scales, the system is nearly friction-free which leads to better repeatability. A further benefit is the absence of lubrication and therefore, their use is more compatible for clean room environments.Another no-cost method to increase repeatability is to center-drive the moving axes of a system. This eliminates the inherent hysteresis of off-axis drives and contributes to system performance. This is most easily achieved with the use of a split-axis transport system. A compound transport nests one axis within the other. This makes interaction between the axes unavoidable and generally locates the drive system outside the measuring envelope, or off-axis. A gantry system fixes the part to the granite base and drives the probes from the side, often mandating the use of dual encoders.
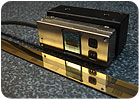
Noncontact linear encoders offer backlash-free submicron accuracy. Source: Starrett
Finally, there is feature illumination, an area where enormous benefits can be obtained while decreasing costs. Earlier measurement and inspection systems used direct lighting and in many instances delivered it to the part via fiber-optic bundles. While there are still applications for this technique, there is the acceptance of LED lighting which offers the advantages of no-heat, long lamp life, even distribution of light, flexibility for all types of illumination and low cost.
Thanks to these new components and design techniques, the seemingly unrealistic goal of attaining higher performance while lowering costs is being achieved by the astute lead of today’s metrology systems manufacturers.Q
Quality Online
For more information on video measurement, visit www.qualitymag.com to read the following articles:“Select the Right Video System”
“Video Is Versatile”
“Video Measurement: 30 Years of Technological Innovation”