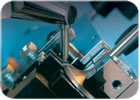
Technology advances have helped make hardness testing equipment easy-to-use, faster and more reliable. Source: The Zwick Roell Group
The use of hardness testers as a relatively simple and economical method of testing mechanical properties dates back more than 100 years. During that period trains, planes and cars have become faster, safer and more reliable. Material science, biomedical and nanotechnology has progressed at a tremendous pace. In addition, the world continues to strive to develop cleaner energy technologies.
Through all these advances that continue to improve day-to-day safety and quality of life, material testing equipment has played a critical and often understated role. For those not involved in the realm of manufacturing or product development, the contribution of hardness testers is mostly overlooked. However, 2010 was a stark reminder of the importance of such quality control measures in the wake of expensive and widely publicized industrial disasters and product recalls.
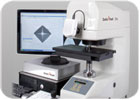
The market is witnessing a trend toward automatic hardness testers in order to reduce operator influence and uncertainty of measurement. Source: Zwick Roell
Opening Doors to New Opportunities
As the saying goes, when one door closes, another one opens. This is particularly true for the hardness test equipment market, with some of its biggest users-such as the automotive and steel industry-going through one of the most difficult periods in recent history. Although the market has gradually recovered, in North America and Europe cost control and budget issues still remain a key concern; evidence that the lingering effects of the 2008-2009 downturn still poses a challenge for hardness test equipment vendors.However, many of those concerns have been alleviated by opportunities arising from different parts of the globe. Countries such as India and China have been almost recession-proof and are driving a considerable level of innovation and growth of hardness testers.
China and India are the two fastest growing economies in the world and in line with this economic growth, energy, infrastructure, manufacturing, construction and transportation demands also have greatly increased, creating a massive requirement for hardness testing equipment in these countries.
Russia is another market with huge potential. Although Russia is considered a difficult market in which to do business as conflicts with American standards still exist, the country has undergone several economic reforms and is expected to demonstrate strong and resurgent growth over the next five to eight years.
“What we’ve seen specifically since the downturn started is growth for orders in India, China and Russia,” says John Piller of Indentec, Zwick Roell’s hardness testing division. “So, we haven’t really seen any downturn. In fact, in the last two to three years we’ve seen nice growth in all of those three emerging economies, primarily supplying European and American companies who have invested in setting up manufacturing facilities in those regions.”
The leading companies in the hardness testing business, such as the Mitutoyo America Corp. (Aurora, IL), The Wilson Hardness Group (Norwood, MA) and The Zwick Roell Group (Ulm, Germany) among others, have been quick to respond to evolving conditions to capitalize on market opportunities. With a strong financial backing and network of sales, support and distribution operations across the globe, these companies have been successful, to a certain extent, at weathering the storm.
On the other hand, companies with core customer bases restricted to certain geographies, primarily North America and Europe, have found it difficult to cope and will be looking forward to 2011 and the new opportunities ahead.
Another segment of the hardness testing business that has witnessed a spike in interest following the economic downturn has been the services market. The unfavorable economic climate has caused end users to rethink their capital expenditure strategies. So rather than buying a brand new hardness tester that can set the operator back anywhere between $2,000 to $50,000 for a fully automated instrument, customers are turning to their equipment suppliers for service, repair or refurbishing of their existing equipment.
According to Bill O’Neill, director of business development and sales for The Wilson Hardness Group, a division of Instron, success in this industry is defined by working closely with customers. “A lot of our market is automotive or automotive supply-based,” he says. “Therefore, everyone from the big automotive suppliers to the people that feed them took a big hit in 2009. However, that translated to end users doing more services on their machines. Also helping people do more with less people. Customers had to trim their employee base but often had to continue the same level of testing. One of the challenges we met was to help people work efficiently with less.”
Automation-the Decisive Factor
A common misconception among testing circles is that hardness testing equipment has not embraced technology to the same extent as some of its other test and measurement counterparts. Although the fundamental measurement technique remains relatively the same, leading hardness test equipment manufacturers are now offering their customers the most sophisticated quality control solutions out there, integrating the latest advances in computing, software, X-Y table and stepper motor technology. These technology advances have helped make hardness testing equipment easy-to-use, faster and more reliable.“Currently, close to 50% of what we supply has a computer attached to it and that number is growing,” Piller says. “The other 50% is still a manual environment but those customers are really not carrying out too many tests.”
This opinion is echoed by others in the industry. “Demographics are changing and we are moving toward a demographic that insists on having automated data collection, manipulation, storage and computerization,” O’Neill says.
A key force behind this drive toward automation of hardness testing equipment is the need to ensure accurate and high quality results. Bodies such as ASTM and ISO continue to modernize and evolve standards and specifications in accordance to changing market conditions.
Moreover, with the continuing trend toward outsourcing of manufacturing operations, auditing bodies such as NADCAP have been set up to ensure compliance with the latest hardness testing standards for aerospace manufacturers and their supply chains. Conformity to the highest levels of quality particularly in safety critical applications is of primary importance to customers and, as a result, the market is witnessing a trend toward automatic hardness testers in order to reduce operator influence and uncertainty of measurement.
Another important factor to consider is that the skill sets of current operators is nowhere close to what it was about 10 to 15 years ago. Customers are now happy to have their measurement parameters met by a mere push of a button rather than relying on the data interpretation capabilities of an inexperienced operator.
However, according to Piller this has had little bearing on the automation trend, highlighting that it is quality driven rather than being about lack of skilled operators. “Yes, there are some skill shortages. However, it’s not rocket science. And with some good training from the supplier of the hardness tester, you can get just about anybody to get good quality results.”
Small is the New Big
Everything seems to be getting smaller these days, and subjecting miniaturized components to material tests poses some of the biggest technical challenges for hardness test equipment vendors but at the same time is one of the fastest growing application markets. “Micro Vickers is where we see the biggest increase in potential orders for the next five years,” says Piller. “That’s the area that we put in most of our research and development (R&D) capability because that’s definitely a fast growing market and customers want to test smaller parts; thinner coatings; and thinner, smaller and cheaper processes, and they expect the same level of accuracy of results.”The continued drive toward smaller, faster and cheaper materials in industries such as semiconductor, biomaterials and fibers has created the need for more accurate and standardized test equipment. The challenge for hardness test equipment vendors lies in creating a cost-effective platform to meet the specialized needs of a wide range of customers. As a result, in many cases, test equipment vendors are unable to meet necessary requirements and customers depend on in-house developed testing solutions. This segment of the market, however, is in a state of continuous improvement with ever-evolving technologies broadening the scope of hardness testing equipment beyond its traditional markets.
The Future
The past two to three years has been a period of adjustment in the hardness test equipment market. Vendors were required to re-align and reorganize their strategies to help customers do more with less in tough economic times. As global markets climb out of the recession, 2011 promises interesting times.From a technology perspective, automation will drive the market for the next few years with a significant percentage of product introductions expected to follow this trend. There are still certain applications where traditional instruments will continue to play a role, but as technology and the market needs evolve, the shift toward automation of hardness testing is a strengthening and undeniable trend.
Quality Online
For more information on hardness testing, visitwww.qualitymag.comto read the following:“Easier Hardness Testing”
“Hardness Testing Gets Automated”
“Hardness Testing Help”