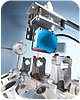
Shown here is inspection of machining tolerances on an engine block using an OD sensor. Source: Sick
Typically, photoelectric applications are for simple presence detection to confirm whether a target is present. Many applications in today’s market now require confirmation that not only is the target present, but the distance of the target in relationship to the sensor must be determined as well. An example would be if the target is a metal sealing ring that must be inserted into an assembly in a specific position rather than simply to confirm the ring is present; a distance measurement sensor would give an analog value relevant to the actual opposition.
The demand for these types of applications in manufacturing has resulted in the introduction of many distance measurement sensors, primarily using optical principles. These sensors produce outputs, which are most often analog values that are correlated to the distance to the target. Depending on the level of performance required for each application, operators can choose from a variety of distances from submicron to mile.
Many distance measurement sensors use Class I and Class II lasers as their light source as opposed to older sources, such as infrared (IR) and light-emitting diode (LED). The long life expectancy and small spot size of these lasers have greatly improved over the years. Low average wattage makes these lasers safe in all factory automation and quality inspection processes.
The distance to the targets can be identified as short-range (<700 millimeters); medium-range (700 millimeters to 30 millimeters); and long-range (30 meters to 120 meters).
Short-range distance measurement sensors, often referred to as optical displacement sensors, are typically used in quality control processes to measure dimensions, positions and shapes such as width, height, thickness, curvature, diameter, deformation, position and vibration.
Short-Range Basics
Short-range distance sensors are an ideal alternate in many applications to linear variable distance transducers probes (LVDT) and are cost competitive when motion of the probes is required.LVDT probes require contact with the target material, which could damage the probes and also require regular calibration of the probes. While many quality managers believe that probes are more accurate than noncontact sensors, this has been proven incorrect with the advent of new receiver technologies.
Optical displacement sensors are available in two styles of operation. The first is standalone where the sensors are self-contained in a single housing and allow individual measurement capabilities.
Sensor systems are the second style and are designed so that individual sensors interface with a common controller. This controller allows more functionality in the selection of various filters, output functions and easy programming compared to interfacing with a programmable logic controller (PLC) but at a much lower cost. Some controllers have the capacity to interface with up to three sensors to obtain calculated formulas between the sensors or receive individual measurements values from each sensor.
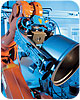
An OD sensor confirms accurate positioning of target in a robotic application. Source: Sick
Applications
Quality inspections primarily focus on the short-range distance measurement products that deliver the best resolution, repeatability and accuracy. In applications where parts are measured to tolerances in micron and submicron levels, quality inspectors understand that conditions must be conclusive to support these high levels. Therefore, fixturing of parts/targets and environments must support the process for accuracy. Inspectors should not find high accuracy measurement sensors at the bottom of the punch press or in areas of heavy coolant/cutting oil presence.Definitions
In selecting the best distance measurement sensor for an application, consideration must be given to certain issues in addition to the basic distance to target requirement. A general principle to follow is that the closer the sensor is mounted to the target material, the higher the performance.The ideal solution also will need to consider three sensor specifications that are unique to distance measurement:
1. Resolution. This is the unit of measurement that the sensor is capable of measuring. For example, with a simple ruler for linear measurement, the resolution is 1-millimeter or 1/16-inch. The resolution goes from 1-millimeter, 2-millimeter, 3- millimeter and more.
If the sensor considered has a specified resolution of 10 millimeters, then the next unit of measurement in the scale would be 20 millimeters, 30 millimeters and up. In the shorter sensing distances, resolutions of 0.02 micron are achievable.
2. Repeatability. This is defined as the deviation of several measurements performed under the same conditions. If the sensor measures and sends an analog value every millisecond, these values should be very similar and consistent if the repeatability is good. This specification is the most critical of these three variables. In the shorter sensing ranges, repeatability of 0.06 micron can be utilized.
3. Accuracy. This can be explained as the maximum expected measuring error between the determined and the actual distance. Differences in accuracy can be stated in either millimeters/microns or in percentage of full scale measurement range. If the accuracy specified is ±1% of full scale and the sensor has a full scale of 20 millimeters, then the accuracy would be ±0.02 millimeter.
Some manufacturers do not specify accuracy but refer to this as linearity. This is defined as the maximum deviation between the output signal and an ideal straight characteristic. Offset and gradient errors can still exist and must be considered. With shorter ranges, accuracy of ±1.6 microns can be maintained.
In addition to the three characteristics defined, consideration in the application must be given to response time-time between the actual measuring tasks vs. output changes. If the application is to measure the machining tolerances of a metal surface, the response time would not be critical as opposed to measuring the thickness of postal mail travelling at 6 meters/second.
Other considerations are type of interface outputs. Generally, simple switching outputs with high and low set points would offer uncomplicated logic to indicate pass and fail in the process. Analog outputs in either 4 to 20mA current or 0 to 10VDC voltage signals allow monitoring and easy adjustments to process tolerances and variables. The best solution can be determined by the personnel who oversee quality.
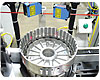
In an automotive application, a steel ring is inserted into transmission part. The ring must be assembled in a specific position (and not upside down) to ensure quality assembly. The OD sensor measures the part position by using the switching output for go/no go indication. Source: Sick
Technologies
By understanding the technology used in the sensor, the operator can easily apply the product in the most beneficial manner. Two primary optical technologies are used in distance measurement sensors. There are positive attributes with each method and other unique characteristics of which operators must be aware:Triangulation. This takes place when a laser light spot is projected onto the target. The reflection from the light is then mapped onto a light-sensitive receiver element. Based on the position of the mapped light spot and the known geometry of the sensor optics, the distance is determined.
This method requires the light spot’s return to the receiver to be angled and cleared of any obstructions. When an application requires the measurement of the depth of a narrow hole, caution must be observed since the entry path is often too narrow for the returning light to clear the hole at an angle. In other words, the light is allowed to enter the hole but cannot exit it without striking the side of the hole. Sensors that utilize triangulation offer high accuracy performance at short distances.
Even though all optical displacement sensors use triangulation, the receiver technology varies depending on the manufacturer. Some vendors will use position sensing detector (PSD) receivers which is a simple photo diode similar to baseline photoelectric sensors. This older receiving method can output different measurement values dependant on the color/remission of the target, such as dark vs. light, and a colored target equals different values.
Some vendors use charge-coupled device (CCD) receivers, which are commonly used in digital cameras.
Both receiver styles are particularly prone to being blinded by shiny targets when the returning light exceeds thresholds in the receiver. This effect is called blooming and can be experienced in digital photography when the receivers are blinded by bright light. As a result, many manufacturers prefer complementary metal-oxide semiconductor (CMOS). CMOS receivers feature natural anti-blooming characteristics and measure dark remission and light remission targets with high accuracy.
Time-of-flight. In general terms, time-of-flight measures the time it takes for the light to return to the receiver rather than the amount of light as in baseline photoelectric sensors. There are several benefits to this method, which include severe angles to the target and very long distance measurement capabilities. Caution must be applied to the remission color of the targets though and most manufacturers will specify sensing ranges for various color remission levels.
Benefits
Regardless of the market segment, the importance of producing quality products is not undervalued in today’s competitive markets. High accuracy, noncontact measurement sensors are utilized in automotive, packaging, machining, robotics, tooling and generally all manufacturing areas.With a wide variety of measurement sensing ranges, interface styles and easy-to-set up programming, these distance measurement sensors can help ensure quality inspections and processes.V&S