Hardness tests are commonly used to check material uniformity or processing treatment. Most hardness tests yield results based on a material’s ability to resist indentation while under test. A material’s ability to resist scratching also is considered a hardness test, as is the measurement of the amount of energy absorbed by a material when struck by a falling object.
Macroscale hardness testing determines the hardness of a material as a whole. The Brinell, Rockwell, scleroscope and Vickers hardness tests are examples of such measurement. On the other hand, microscale hardness testing functions on a very small scale and can be thought of as determining particle hardness. The Knoop hardness test is an example.
Specimen thickness must be considered when selecting a hardness test method. The tester’s anvil, on which the specimen rests, must not affect the indentation made by the indenter. If there is an imprint on the underside of a specimen after a test has been performed, the specimen was too thin for the test method.
The Brinell test is applicable for large parts such as castings and forgings of low to medium hardness. A Brinell test applies a known load for a specified length of time to the specimen under test. The diameter of the mark left by the indenter-a hardened-steel or carbide ball-is measured and usually converted to a Brinell hardness number.
Rockwell and Vickers tests are used for small parts, as well as parts of low, medium or high hardness. The Rockwell test makes two indentations; the indenter applies a minor (initial) and major (final) load to the specimen. The different depths affected by each load are then compared. The Vickers test is very similar to the Brinell test, except that it uses a pyramid-shaped diamond indenter.
Scleroscopes are portable hardness testers used for routine inspection and shop tests. The test is based on the height of rebound a steel hammer experiences after colliding with the specimen from a fixed height. The hammer falls through a graduated glass tube, and the rebound is measured by eye or an indicator.
A Knoop test applies a known load for a specified length of time to the specimen under test. The indenter is a diamond having unequal longitudinal and transverse included angles. In addition to determining particle hardness, the Knoop test can be applied to very small as well as very thin specimens.
Hardness testers are made as both handheld and motorized devices. Motorized testers are advantageous for high-volume testing and can help eliminate operator fatigue when heavy parts require testing.
What follows are hardness testing products available today.
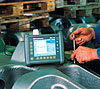
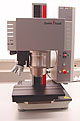
The tester’s instrumented indentation testing in the macro range covers a range of applications and has hardware and electronics made to the requirements of hardness testing. In addition to instrumented indentation tests to determine hardness and other material parameters, the tester can perform all the classical hardness testing methods used for metals.
Whichever method is used, the testing system records the load-indentation depth curve to provide additional material assessment. The instrumented indentation test includes elastic and plastic deformations in order to obtain the elastic and plastic material characteristic values.
The core of the testing system is a hardness measuring head, into which the measuring systems for test load and indentation depth, plus an indentor with hold-down device, are integrated. For optically based hardness testing methods to Vickers, Knoop and Brinell, an add-on unit with measuring microscope is available. Indentation setting, microscope positioning and optical measurement of the indentation are all performed automatically.
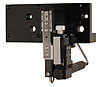
The higher loads are well suited for testing hard coatings, such as those used in the tooling industry. However, the more sensitive loads of the micro range are ideal for the characterization of industrial coatings, ranging from plasma processed layers used in semiconductor and optical technology, to decorative and protective coatings used for automobile parts and consumer goods. The module uses independent force and depth sensors to obtain depth vs. load curves used in instrumented indentation. True load feedback control ensures stable scratch and wear testing.
The module uses a noncontact white light sensor directly connected to the diamond mounting, which enables direct measurements of the depth of the diamond. This technique allows quick tests and eliminates depth errors caused by surface roughness or sinking of the reference on soft materials when a physical reference is used to determine the height of the surface.
The company’s micro technology also provides true depth measurements during scratch testing or wear testing. The light sensor performs as a full 3-D noncontact profiling tool that gives 3-D images of scratch tests, indentation tests or wear tests and can be used for other types of profiling work, such as measuring surface roughness or height of steps.

The tester has an optional advanced analysis module with complete impression coverage of a sample, as well as pattern support for welding studies. An available color hardness/contour map displays sample hardness and location with a color representation of hardness variances. The tester includes case-depth analysis, surface analysis, weld profiles, decarburization and coating hardness. The tester supports both microindentation and macro/Vickers hardness testing in fully automatic and semi-automatic configurations.

Hardness numbers are displayed from 1 to 1/100th point on an illuminated digital control. To comply with ASTM E-18 tolerances, the system provides preset dwell times and automatic cylindrical correction. The system has built-in electronic conversion charts for cross-referencing hardness scales and approximating tensile strength, eliminating the need for mechanical or electronic adjustments.
The tester includes closed-loop NTEP load cell technology that removes the need to use the conventional weights method. The system includes a rigid, modular base assembly, RS232 output and a detachable clamping device for oversized or irregular parts. A self-contained head assembly is adaptable for special applications. The tester also includes upper and lower limit alarms and a fitted tray for indentors and anvils.
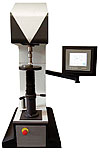
The system uses a principle based on the continuous measurement of the electrical resistance in relation to the working load applied. The stand enables the testing of large work pieces with overall dimensions up to 550 millimeters in height and 350 millimeters in depth.
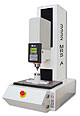


Each model comes with a set of anvils, penetrators and certified, serialized test blocks for confirming the tester’s continued accuracy. Most models read directly in all standard and superficial Rockwell scales. Charts are provided to convert the readings into other Rockwell scales or Brinell, Vickers or Knoop equivalents.

The tester has a standard automatic turret and eight dial-selectable test forces ranging from 10 grams to 1,000 grams, with an optional 2,000-gram test force available.
Having optics with a magnification of 100X and 400X, measurements are automatically made through the high-resolution USB digital video camera system. The fully automatic stage provides 100-millimeter by 100-millimeter travel for multi-sample testing. The tester is ASTM and ISO compliant.

The manufacture of these hardness test blocks includes the stability of closed-loop load cell technology. Brinell test blocks are calibrated with tungsten carbide ball indenters. Each test block comes with NIST-traceable certification and is compliant to American and international standards. WESTport is accredited to ISO/IEC 17025, ISO 9001, ISO 6506 and ISO 6508.
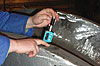
Because of the single loading/release mechanism, metal hardness testing can be done in less than two seconds. To simplify the testing of metal hardness, the testers come with an automatic compensation for impact directions.
The Equotip Bambino 2 is particularly suitable for on-site hardness checks. It has all the measurement capability of the Equotip Piccolo 2, but the Equotip Piccolo 2 additionally offers real-time monitoring and operator-defined hardness conversion curves, and comes with Piccolink software, which allows analysis of recorded data and the ability to edit and export data to reports.
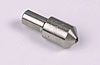
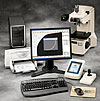

The tester has a wide test force range-0.1 to 1,961 millinewtons full scale-and a low test force with measurement resolution of 0.196 micronewton, allowing measurement of material strength properties in micro regions and in the outermost surfaces of specimens. Specimen indentation depth can be measured in units of 0.0001 micrometer for depths up to 10 micrometers, and operators can perform precise evaluation of the elastic modulus using correction based on instrument rigidity and the shape of the indenter tip.
The tester supports a range of testing methods, such as depth setting, unload and load processes, cyclic and step load/unload tests and the Vickers hardness test. Numerous data processing functions enable the display of test force, displacement and strength for graphical comparison and analysis. Optional accessories include a length measurement kit and slender specimen holder.