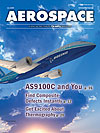
The credibility and professional worth of nondestructive testing (NDT) inspectors depends on their understanding of current and future quality management systems. Recent revisions to the ISO 9001 and AS9100C standards as characterized in ISO 9001: 2008 and AS9100C expand and define the need to control risk, critical items and key characteristics. The need to possess a better understanding of configuration and risk management also is covered under these revisions.
First, it should be understood that these changes have come about as a result of globalization and “outsource mania,” which has made manufacturing organizations more liable for product reliability. The toy recall of 2007 is just one example where the principles of configuration management should have been relied on more thoroughly, but were not, as evidenced by the millions of dollars lost by toy manufacturers as a result of the massive product recalls.
NDT inspectors have an opportunity to take the lead in ensuring that companies are following the standards set forth by quality management systems such as ISO 9001: 2008 and AS9100C. By driving quality management within the organization, they also will demonstrate the need and value visual inspectors trained in specific tasks can offer the organization, which in turn means greater job security. By leading the organization in this way, they also are helping to position the company as an industry leader when it comes to quality and product reliability.
The Impact of AS9100C
When it comes to the AS9100C quality management revisions, it is important that NDT inspectors are fully aware of the impact on what could mistakenly be perceived as a minor title change.The new standard states the intent and rationale for the changes that have been made. What differentiates it from previous AS9100 standards is the use of ISO 9001: 2008 in its entirety, with added clarification and specific evaluation attributes to be incorporated by aviation, space and defense organizations. Note that the change from “aerospace requirement” as used in previous versions of the standard, to “aviation, space and defense organizations” is intended to broaden the application of the standard.
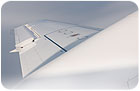
The Role of Configuration Management
It is likely that the most significant area of focus for AS9100C is its requirement that organizations establish, implement and maintain a configuration management process that includes, as appropriate to the product, configuration management planning, identification, change control, status accounting and auditing of the effectiveness of the program.Configuration management monitoring, verification and validation are the functions of a field visual inspector, also known as a project manager or verification inspector. As stated in section 6.2.1 of the AS9100C quality management system: “Personnel performing work affecting conformity to product requirements shall be competent on the basis of appropriate education, training, skills and experience.”
Section 6.2.2 of the standard also states that in the competence, training and awareness each organization shall: “Determine the necessary competence for personnel performing work affecting conformity to product requirements; where applicable, provide training or take other actions to achieve the necessary competence; evaluate the effectiveness of the actions taken; ensure that its personnel are aware of the relevance and importance of their activities and how they contribute to the achievement of the quality objectives; and, maintain appropriate records of education, training, skills and experience.”
To meet the education and training requirements imposed by AS9100C, the only guidelines that make sense as a foundation for visual inspectors are those as outlined in ASNT TC-1A.
The Recommended Practice No. ASNT-TC-1A document provides guidelines for employers to establish in-house certification programs for the qualification and certification of visual testing personnel. Since 1966, employers have used the ASNT-TC-1A document as the general framework for their nondestructive testing (NDT) certification programs. There are three levels of certification: Level I, II and III.
For example, the ASNT-TC-1A requires a Visual Level II candidate with a high school or equivalent education to receive 16 initial training hours and then two months or 140 days of experience in his or her discipline to be certified. There are also requirements on his or her test questions, such as 30 general questions, 20 specific questions, and a composite grade of at least 80%, with no individual examination having a passing grade less than 70%.
Granted, the depth of ASNT TC-1A may seem like overkill but as stated in the standard “the training program shall meet the needs and complexity of the organization that uses it.”
The AS9100C standard identifies the need for project management in section 7.1 Planning of Product Realization and states: “The organization shall plan and develop the processes needed for product realization. Planning of product realization shall be consistent with the requirements of the other processes of the quality management system” and “In planning product realization, the organization shall determine the following, as appropriate: Quality Objectives and requirements for the product; the need to establish processes and documents, and to provide resources specific to the product; required verification, validation, monitoring, measurement, inspection and test activities specific to the product and the criteria for product acceptance; records needed to provide evidence that the realization processes and resulting product meet requirements; Configuration Management appropriate to the product; and, resources to support the use and maintenance of the product.”
Product Manager Equals Visual Inspector
When the AS9100C in section 7.1.1 defines project management as being appropriate to the organization and the product, and that the organization shall plan and manage product realization in a structured and controlled manner, to meet requirements at acceptable risk, within resource and schedule constraints, it seems it is really talking about the visual NDT inspector. A visual inspector by any other name is still a visual inspector.Also, when AS9100C addresses customer and applicable statutory and regulatory requirements, and then goes on to give the definition of risk, special requirements, critical items and key characteristics in section 3, it shines a light on identification, verification and testing. The only way to make sure that customer, applicable statutory and regulatory requirements are met would be to understand customer contract requirements. Who better to do this than a visual inspector?
NDT: An Integral Part of AS9100C
AS9100C section 7.1 identifies requirements for processes in project, risk and configuration management. In this section, it is clear that visual inspections must be identified during the planning stages, and followed by documentation and verification inspections on the production side. Most companies today view NDT inspections as dye penetrant, magnetic particle, radiography, ultrasonic and eddy current inspections.Today’s NDT inspectors must rethink their place within the organizations that they work for, and reinvent themselves so that they may be recognized as a greater asset to the organization. That can easily be achieved when the NDT inspector is included in the planning process (see AS9100C Section 7).
However, in order for this to happen, the visual inspector must be retrained so that they are able to identify customer contract and applicable statutory and regulatory requirements, along with configuration management. This is a big opportunity for NDT personnel, and at all costs, they should avoid being pigeonholed within the mindset that NDT is only inclusive of dye penetrant, magnetic particle, radiography, ultrasonic and eddy current or they may be replaced by an outsourced agency. In AS9100C, the visual inspector’s main function is to ensure that configuration management is maintained through the life of the product.
Today’s NDT inspector must take advantage of the biggest reason that ISO 9001 and AS9100C were revised, which as stated in the quality management system is “the globalization of the industry and the resulting diversity of regional and national requirements and expectations have complicated this objective. Organizations have the challenge of purchasing products from suppliers throughout the world and at all levels of the supply chain.”
Suppliers are challenged in delivering products and maintaining configuration management relative to multiple customers who have varying quality requirements and expectations. The Mattel lead paint and tainted Chinese drywall problems are just two examples of quality management issues faced by global companies. Because configuration management is now required by AS9100C, similar challenges can be avoided because such issues, as faced by these two companies, are easily identified through visual inspection methods.
Visual inspection does not just mean looking for defects and discontinuities in a product; it also is used to ensure that configuration management principles are in place.
As seasoned inspectors know, the first step is to perform a visual inspection on the documentation and recorded results to identify any anomalies. In both problems mentioned earlier, “the fox (subcontractor) was watching the chicken coop (subcontractor),” yet where were the visual configuration management inspectors? How much did Mattel save by having inexperienced and untrained personnel manage the product configuration? Not a penny. In fact, they lost money due to the product recall.
Remember, as NDT inspectors, job security lies in the ability to understand and implement both current and future quality management systems. Under no circumstances should inspectors underestimate the power they have to lead the company into a future of manufacturing practices that produce high quality products conforming to statutory, regulatory and customer requirements.