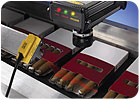
Unlike a simple proximity switch, which is essentially a single pixel, digital imagers contain tens of thousands of microscopic light meters. Often, the only output required of a vision sensor is the simple go or no-go commonly found on most proximity sensors. Some processes, however, require words or images collected from vision sensors. Vision sensors can connect with other industrial control devices to deliver this information in several different ways. The three output types found in most vision sensors are discrete, RS232 serial and 10/100 Ethernet.
Discrete is the oldest style, but it also is the simplest and most commonly deployed output type used on vision sensors today. An inspection or recipe resident on a vision sensor analyzes its digital image and renders a simple pass or fail decision-applying voltage to a programmable logic controller (PLC) input or directly powering a control mechanism such as a solenoid. Sensors are equipped with numerous outputs that can be configured for controlling specific devices.
RS232 serial protocol is a relic from the previous millennium, yet it remains a simple way to communicate with a control device, such as a robotic arm. Vision sensor communication tools are easily configured to send information over RS232, including measurement values, brightness information or centroid locations critical to a manufacturing process.
The most modern and flexible communication output for vision sensors is the 10/100 Ethernet interface. Simple pass/fail information, location values and other metrics, as well as full-resolution bitmap pictures, can be sent to controlling devices over the 10/100 Ethernet port.
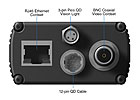
Industrial Ethernet Connectivity
When connecting a vision sensor to a PLC, operators can use the sensor’s discrete digital outputs, as mentioned earlier. However, it is easier, more flexible and much more powerful for the vision sensor to speak with the PLC in its native language. Industrial Ethernet standard protocols such as EtherNet/IP and Modbus TCP facilitate PLC communication, allowing the sensor and PLC to interact by reading and writing to a common set of memory registers. Vision sensor inputs such as trigger (when to initiate snapping an image for analysis), remote teach (instructs the vision sensor to learn the next image and make this image the new golden template) and product change (changes operating inspection files or recipes on the vision sensor) can be controlled by the PLC. The PLC also can tell the vision sensor what barcode data, optical character recognition (OCR) matching or American Standard Code for Information Interchange (ASCII) string it should expect to see on the next inspection.Outputs sent from the vision sensor to PLC via industrial Ethernet commonly fall into two broad categories. System health data includes information such as pass/fail status, frame count and error status. Inspection-specific data includes operator-defined variables such as measurements, centroid locations, colors and the data read in a text string or barcode symbol
