In the early 2000 era, companies were happy just to have a website. Then the emergence of cloud-based applications driven by web browser technologies brought about SAAS (software as a service), and the business environment underwent a paradigm shift toward digital infrastructure—one that could improve production and increase profit.
As the web evolved further with a virtually free supply of Linux servers, cloud storage, and large-scale database support, companies introduced e-commerce systems that required real-time access to manufacturing data (current inventory levels that customers could query, work in progress status, B2B supplier transactions, shipping services).
At the time customers were driving the commerce experience with online shopping, online product feedback, and online shipping and tracking. Manufacturers needed greater information at the factory floor level and real-time feedback on transaction fulfillment. Cloud services were in place, but was the factory floor ready?
The Limitations of Cloud Computing
Early cloud usage involved sensors sending raw or minimally processed data to the cloud for processing. Despite the benefits of this approach, it would prove to have limitations in a factory setting. While useful for serving customers with real-time status on orders and facilitating operations across factories, cloud computing in the plant was unsuitable in applications where:
Rapid data sampling and low-latency are critical (such as high-speed, closed-loop inline inspection of manufactured parts) and
Large amounts of data or significant bandwidth constraints (causing bottlenecks) make it inefficient or impossible to send all data to the cloud, all the time.
Securing and protecting vulnerable data against cyber threats in factories connected to the internet.
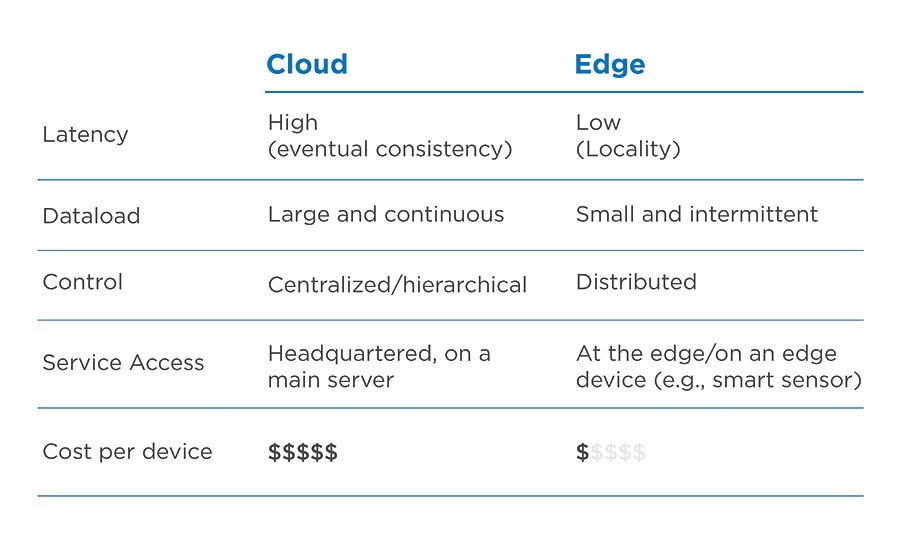
Fig. 2. A brief comparison of cloud-based vs. edge solutions.
The Answer? Computing at the Edge
The cloud-based move to SAAS and e-commerce drove the need to generate and process data directly from the factory floor, and it was at this point that bandwidth and latency issues became a roadblock to real-time reporting. In response, smart sensors were introduced to efficiently perform computing at the “edge” of the factory network.
Edge devices reduced data loads and reported meaningful, high-level results that supplied e-commerce systems with real-time information. This approach allowed industrial organizations to analyze essential data faster by processing machine-based data closer to the source.
Industrial machines, industrial controllers, data processors, and time-series databases that aggregate data from a network of equipment and sensors are all examples of early edge technology.
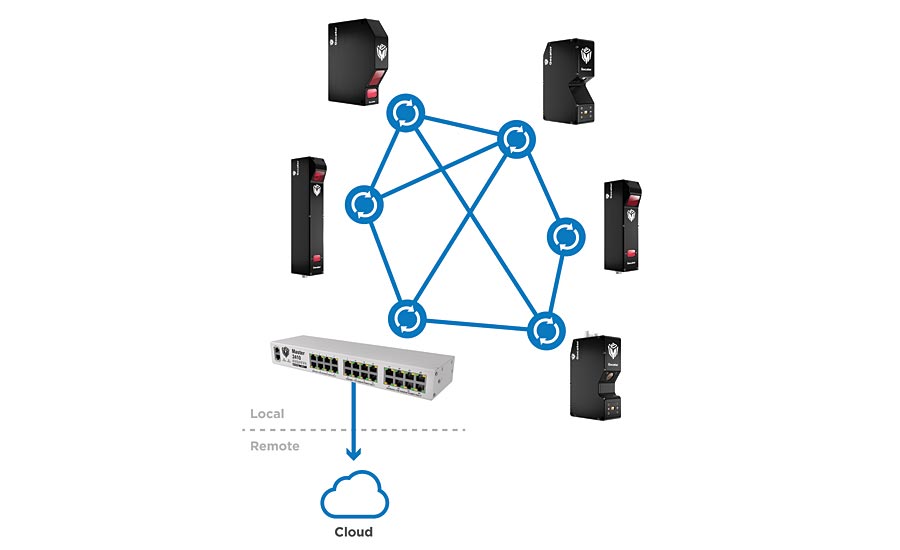
Fig. 3. Edge devices act both independently and as part of a network.
Edge Computing - From Thin to Fat Clients
Edge computing devices started out as thin clients (i.e. strictly capable of receiving, storing, filtering, and communicating data to ‘parent’ cloud systems). However, the explosion of raw data generated in industrial environments and the need to minimize latency caused edge devices to evolve into fat clients—providing increased computational and analytic power to process and act on data at or near the machine location.
Today, edge devices are widely used in factory environments to improve production. Examples of such devices include machine vision sensors and sensor networks that collect or produce 3D and 2D data for automation, inspection, and optimization.
Benefits for Industrial Production
Smarter Manufacturing
Edge computing dramatically reduces system complexity by providing customization of production modes. As a result, small-quantity and multi-batch modes can replace high-volume manufacturing.
Multi-model and batch methods are leaner and yield higher quality products, with fewer errors, less downtime due to cell and tooling changeover, as well as reduced waste. Also, flexible adjustments to production plans and rapid deployment of new processes and models offer significant cost benefits to smart manufacturers.
Energy and Cost Efficiency Management
Edge computing decreases energy consumption and maintenance costs while increasing system reliability.
Sensor Design (with an Edge)
Smart sensors are a vital component of edge systems, providing a range of abilities that improve productivity in the factory. Here are some of the ways these sensors are helping drive IIoT today.
Smaller Form Factor
Production systems now require smaller and more autonomous edge devices (i.e., smart) that can run for extended periods of continuous use at the perimeter of the network, where diagnostic and monitoring resources are scarce.
Solely from a hardware perspective, compact smart sensors increase ease of system integration and device usage—both beneficial to edge system deployment.
Network Connectivity
On top of being compact and ruggedly constructed, edge devices need to be network aware. Smart sensors address this need by having an IP address and support network communication protocols that enable direct communication with other factory equipment such as robots and PLCs, or for the transfer of measurement data to factory databases.
In a network-enabled smart sensor that digitizes and measures a target object, smaller packets of high-level data are communicated to the cloud at select intervals—rather than transferring raw scan data continuously for processing elsewhere. This capability alleviates pressure on network connectivity and minimizes latency and bottlenecking, all by providing distributed processing on the edge of the factory network.
Software
Configuration and maintenance of many production systems leveraging smart sensor technologies can lead to network management challenges. This challenge is why edge computing requires all devices in the network be handled in a uniform manner—ideally as a fully automated process controlled with built-in software.
As previously mentioned, today’s advanced smart sensors are fat clients, meaning they have software that can perform data processing onboard. This functionality enables the hardware devices (and their extensions) to become a virtualization platform where processes can be emulated, tested, and tuned offline then deployed to real hardware on the factory floor.
In a smart paradigm, the edge device (in this case a sensor) cannot only acquire data but process data and communicate control decisions to factory equipment—directly from the edge, without having to send data back to a centralized location or local computer racks. The software allows smart sensors to carry out computing and storage onboard so that select applications can be executed locally at very high speeds.
Distributed and Scalable Network Architecture
Edge computing relies on the seamless cooperation of distributed peers. There is no centralized controller anymore; instead, a collection of devices acting independently yet communicating cooperatively.
Smart sensor networks built on a distributed architecture facilitate scalability and empower process engineers to develop specific measurement and control solutions for each manufacturing cell. Applications are implemented by using “snippets” of code that can securely run edge devices, requiring minimum interaction with coordinating elements. This prevents unnecessary or undesired uploads to servers in headquartered data centers.
Security and Privacy
In today’s factory, proprietary information can easily be leaked through any connected device, platform, or even the network itself. Consequently, manufacturers are becoming more and more concerned about the exposure risk to their proprietary data.
In addition to the technical challenges introduced by a large number of devices running in a factory, there is now another demand for smart sensors to support security such as user profiles (e.g. technician vs. administrator), encrypted firmware and settings, and secure protocols to exchange data with cloud storage.
In Summary
Edge computing improves time-to-action and reduces latencies down to milliseconds while minimizing network bandwidth. In combination with cloud computing and powered by smart sensor technology, these edge systems can have a profound impact on industrial system performance and ultimately increase productivity and profit for manufacturers.