While fairly new to the metrology world, multisensor machines are becoming increasingly popular on shop floors for their unparalleled versatility. Unlike traditional vision machines or regular CMMs, these hybrids can quickly, accurately, and interchangeably measure 2D and 3D parts in a single run.
One such machine is the O-INSPECT from ZEISS Industrial Metrology. A multisensor CMM with 2D optical and 3D tactile capabilities, the O-INSPECT uses the same scanning probe and software as ZEISS CMMs— because it’s calibrated the same way. Instead of being looked at and calibrated as a vision machine with a touch probe, the O-INSPECTs are looked at and calibrated as multisensor CMMs, the camera being just another sensor, explains Jay Elepano, CMM/SFG product manager at ZEISS IM.
Solving the Calibration Problem
Originally, vision machines measured flat, two-dimensional parts with a camera, then evolved to measure more complex, three-dimensional parts with a touch trigger.
“Here’s the problem with that,” Elepano says. “When you calibrate a camera to a vision machine, you really only calibrate in two directions. You don’t calibrate up and down; you only calibrate left and right, X and Y. But once you use a touch trigger, you’re calibrating in Z—and everything that you’ve done for decades to calibrate a machine well in X and Y gets thrown out of the water when you introduce Z.”
For decades, manufacturers have been wrestling with the question of how to calibrate their vision machines in Z as accurately as X and Y. Enter the multisensor CMM.
“While everyone was struggling with how to get a touch trigger to correlate with the camera, we saw the problem: that they were treating the camera as the most important sensor, calibrating the camera first and doing an off-set to the touch probe,” Elepano explains.
Since the camera is only anchored in X and Y, and not at all anchored in Z, we decided to approach it in the opposite way: to calibrate the touch trigger first, and make the camera an off-set to the touch probe. That way, the most accurate sensor in three dimensions is the most important.”
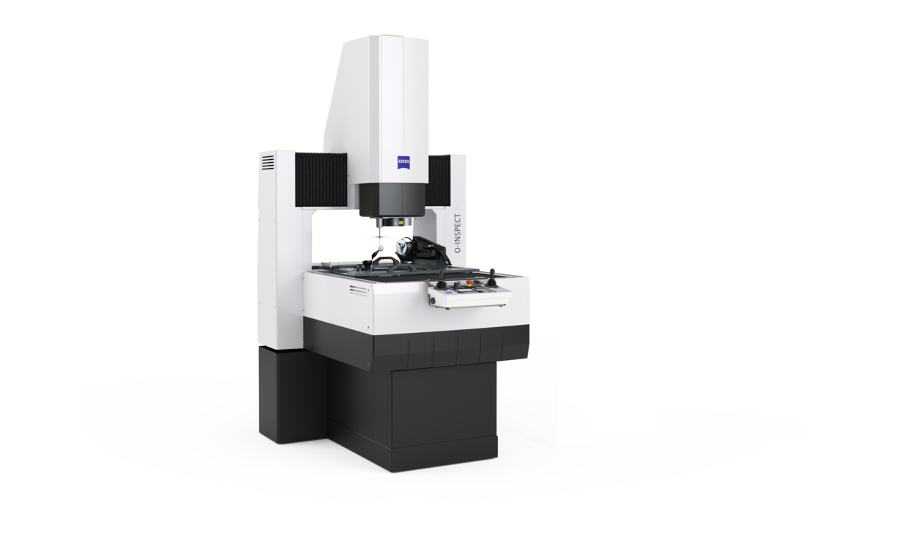
One Machine, Three Sensors
The first and most important sensor in the O-INSPECT, Elepano says, is the VAST XXT scanning probe. The second is the Discovery V12 lensing system, designed and manufactured by the ZEISS Microscopy group, that includes a ring light, coaxial light, and telecentric backlight. The third and optional sensor is confocal white light that can be attached to the side of the machine, and gives an accurate Z dimension height without having to touch the part.
“If the part is three-dimensional, we can put a TL1 on there, which is a very light force less than a gram’s worth,” Elepano says. “So with even the most delicate parts, you can take measurements, tap, and scan—just like you would with a CMM.
That’s how this single machine with multiple capabilities works. Not only are these tools present, but we’ve integrated them in such way that you can use them interchangeably. If they exist, you increase ROI. If they exist interchangeably, it exponentially accelerates ROI.”
Improved Speed, Cost-Effectiveness, and Other Benefits
For manufacturers of complex 2D and 3D parts, investing in a multisensor CMM makes sense. As Elepano puts it, “Instead of buying a CMM and a vision machine, why don’t you buy one that acts like both?”
First, a multisensor machine with 2D optical and 3D touch capabilities can handle 3D work when not being used for 2D applications, which can significantly speed ROI. Second, utilizing one machine instead of two frees up space on the shop floor. It also requires fewer utilities, less training and service costs, and minimal handling and fixturing.
Finally, the automation inherent in multisensor measurement offers multiple advantages. It provides time efficiencies by following a routine based on the program for each workpiece, and eliminates the transition from machine to machine for different types of measurement. It also allows one programmer or operator to choose and set the best sensor strategy for each measuring task, and then makes multiple measurements in a single run.
Finally, choosing a shared software platform like CALYPSO for all machines, rather than buying separate systems for optical scanning and contact measurement, can solve two common and costly problems: hiring two operators to program a CMM and a vision machine, for example, and programming twice to do the same job on two machines.
However, according to Elepano, simply offering a software platform that works on all machines does not automatically translate to cost-savings.
“Anyone can put the same software on multiple pieces of equipment and say it has high ROI value capability,” Elepano says. “But it’s harder to calibrate a vison machine like a CMM; it requires infrastructure that not everybody has or wants to do.
So you need to go a level deeper and ask, ‘Do they really calibrate these machines the same way?’ And unless the answer to that question is ‘Yes,’ it’s just surface-level stuff. It’s just box-checking. They need to walk the walk.”