Many new products entering the market today are based on new materials and are manufactured using novel processes. These new materials are playing increasingly important roles—supporting innovation and boosting competitiveness in technology-driven industries. Identifying the potential for material failure has never been more essential and modern testing capabilities deliver the insights quality managers need to assess material performance.
Exposure to loads, pressures and extreme temperatures in manufacturing has the potential to affect the performance of parts comprised of metals and metal alloys. Due to complex sample geometry and linear correlation between hardness and tensile strength in metals, hardness testing is often the best way of establishing that components will survive and perform in their intended applications. Hardness testing is also applicable to evaluations of ceramic and plastic materials. The relative simplicity of hardness tests, in combination with the ease in which results may be obtained and reviewed, makes them an essential component of the quality control process.
Hardness is the mechanical resistance of a material to the indentation of another harder specimen. Hardness testing is typically undertaken to assess resistance to plastic deformation, a value of tremendous importance to the determination of part quality in a wide range of industries and applications.
Rockwell hardness testing is a method of determining the relative hardness of a material. In a Rockwell hardness test, hardness is measured by determining the depth of residual penetration by a steel ball or a diamond point under load. Rockwell testing is the most commonly conducted hardness testing, as the testing procedure is simple and the readings can be directly attained from the testing machine.
Accurately determining the hardness of a material for any given application involves several factors including the type of material, specimen geometry, surface conditions, exposure to heat treatment processes and production requirements. A range of different hardness tests may be applied to determine different hardness values for the same test specimen. Selection of the type of hardness test is often influenced by end-customer requirements, as hardness measurements are commonly reported values on spec sheets accompanying the delivery of manufactured goods.
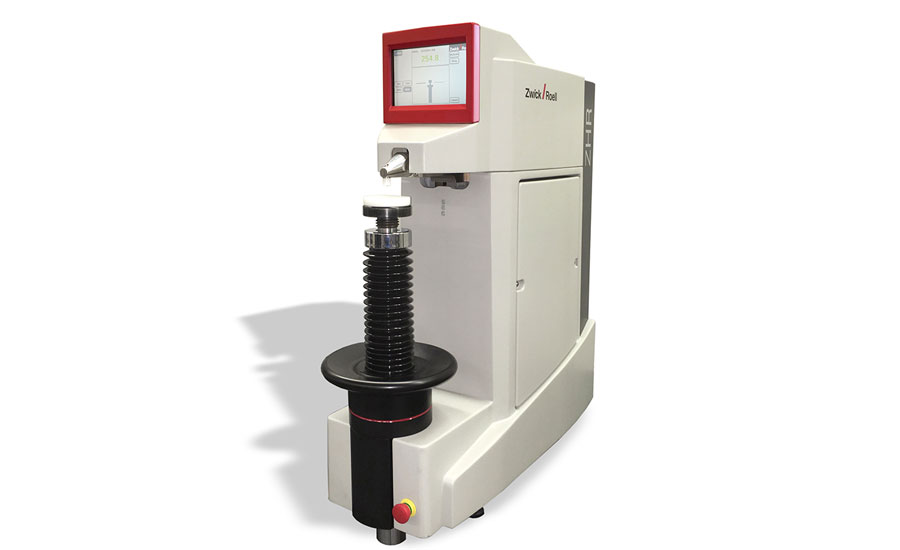
A nose-mounted indenter on this Rockwell hardness testing system accommodates a wide range of sample geometries and offers visibility of test points eliminating the need for test sample sectioning.
The Rockwell hardness test is a measurement based on the net increase in depth of impression as a load is applied. In the Rockwell method of hardness testing, the depth of penetration of an indenter following application of a minor load and a major load is measured. The indenter may either be a tungsten carbide ball of some specified diameter or a spherical diamond-tipped cone of 120° angle and 0.2 mm tip radius, called a Brale indenter. The type of indenter and the test load determine the hardness scale which is expressed in letters such as A, B, C, and so forth.
High throughput testing environments call for solutions that deliver value beyond standard expectations of testing system performance. Depth-sensing test procedures offer additional insights into material behavior that support predictive failure analyses. New universal Rockwell hardness testing systems delivers depth-sensing capabilities across more than 30 measurement applications. Depth-sensing methods are of particular interest in evaluations of plastics and polymer-based consumer and household goods.
The Rockwell hardness testing system incorporates closed-loop force application and supports test forces between 0.5 kgf and 250 kgf. As a result, quality managers and test lab staff can conduct both Rockwell and Rockwell Superficial tests on a single test machine. The latest technology guarantees a high level of test point repeatability and reproducibility for result output of the highest integrity. The testing system is also capable of performing Brinell tests, where a portable microscope measures the remaining indentation.
A nose-mounted indenter enables access to and visibility of awkward test points, eliminating the need for time consuming and expensive test sample sectioning. Overall, sample preparation is minimal, as a nose-mounted indenter enables access to and visibility of test points that would conventionally pose a challenge or require test sample sectioning. As sectioning adds time and cost, the unique positioning of the indenter in the testing system streamlines the testing process.
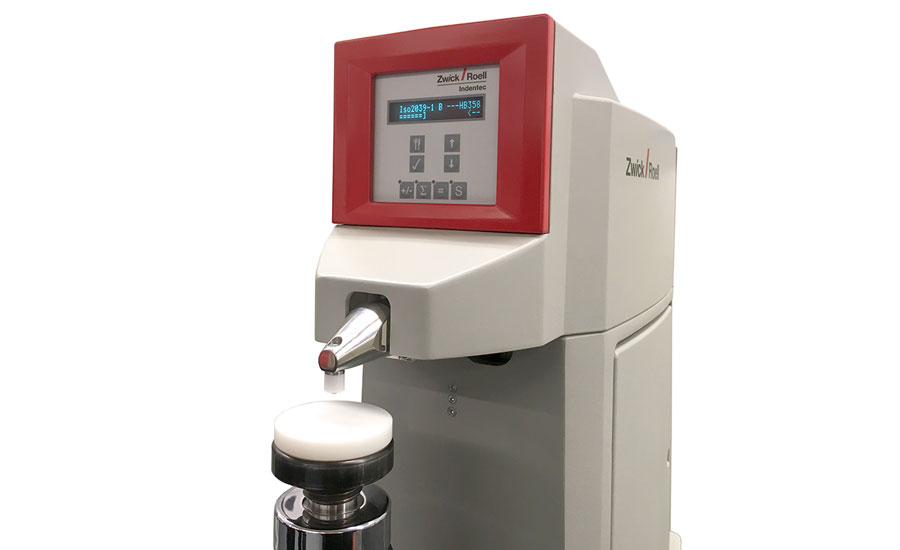
An intuitive touchscreen allows operators to rapidly set up Rockwell hardness tests and review results. Results may also be retrieved via a serial port for further analysis and statistical reporting.
A color touchscreen user interface simplifies the selection of test methods, test configuration and result output, minimizing the potential for operator error. The user interface also supports selection of the testing mode—from manual tests to user-defined automatic cyclic testing functions. User-defined testing functions provide the opportunity to define the number of tests as well as the interval between tests such that the time required for testing is held to a minimum. The introduction of a modern user interface that minimizes eye strain and enables operators to rapidly and intuitively review test results supports throughput and subsequently enhances ergonomics in the testing environment. The latter is essential, as high volumes of testing often call for completion of repetitive tasks that, over the course of a manufacturing shift, can cause operator fatigue leading to sources of error. As error sources are minimized, accuracy in measurement increases and reliable test results may be achieved.
Measured values determined on the hardness tester can be transferred to testing software via a serial port for logging, data archiving and processing. NDT