What is tension? The application of tension involves stretching or pulling a piece of material. Tensile tests are conducted to help specify materials for engineering applications. Engineers are interested in learning the strength of a material to ensure product quality, to develop new materials, and to predict the behavior of a material under other types of loading. Besides the strength of a material, engineers will often study the stress required to cause plastic deformation or the maximum stress a material can withstand.
The term tensile testing can be used broadly to include applications such as wire pull testing, peel tests for film/paper packaging, and the testing of plastic or rubber “dog bones,” or “dumbbells.” An example of wire pull testing is the use of fine wires, such as those utilized in the microelectronics industry. These are often used for connecting integrated circuits and printed circuit boards. To ensure proper functioning and reliability, the tensile strength of these wires must be tested. Another example of a tension testing is related to the quality of packaging material. Peel tests of food packaging seals need to be tested to determine if the package meets industry standards—easy enough for a consumer to open, but strong enough to withstand transportation. Lastly, rubber and plastic samples often require tensile testing. They are often cut into the
shape of a “dog bone.”
What is a dog bone sample?
A dog bone sample is a piece of material, wider at their ends and narrower in between. The shape is defined by organizations such as ASTM, ISO, DIN, etc. The ends are wider into order to concentrate stress in the middle of the sample when loaded in tension. This stress concentration causes the sample to rupture away from the ends. If the rupture of a specimen occurs in the midsection, the material has reached its maximum tensile strength. If the specimen were to rupture close to the grip or in the grip itself, the failure could be attributed to improper loading or a defect in the material.
How do we conduct a tensile strength test?
To perform a tensile test, insert a sample of a material between two fixtures or grips. Begin the test with a specimen of known dimensions, including length and cross-sectional area. Apply force to the material through the use of a universal test machine (UTM), sometimes referred to as a test stand or force tester. Increase the force while measuring the change in length of the sample. Typically, tests are performed in accordance with an internationally recognized standard procedure so that results are consistent between labs. A procedure will often specify an extension rate and the type of equipment needed to perform a specific test.
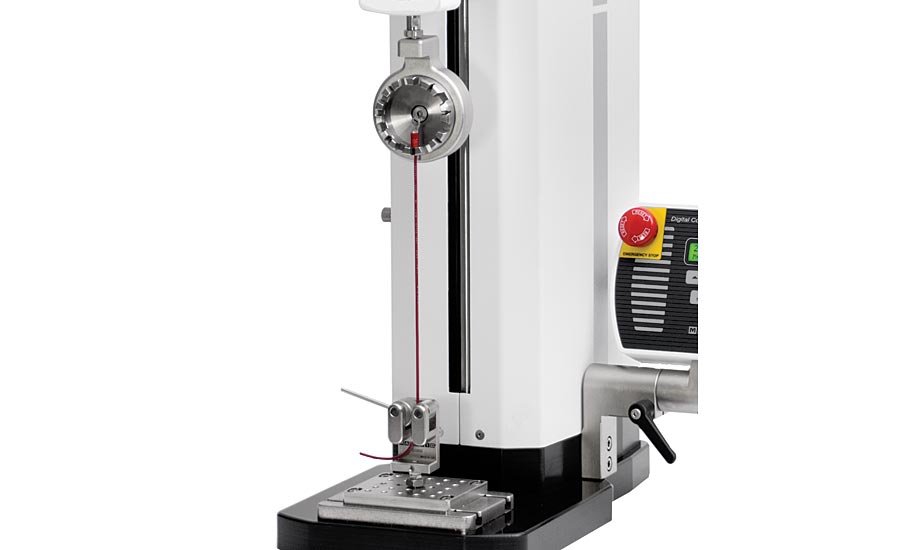
Wire terminal testing is a popular tensile test application.
A complete measurement system incorporates several components: a load cell or force gage to measure tension or compression, the test frame, grips to secure the specimen, and software to analyze the results.
Components of a Universal Test Machine (UTM)
Force gage/load cell
The load cell is the center of every measurement system. Load cells translate force into an electrical signal. Strain-gage based load cells are based on the Wheatstone bridge concept which employs a network of four resistive legs. When a change in strain is applied to a specimen, a change in resistance will occur, resulting in a signal that can be processed and converted into digital form. The result is presented in terms of force units such as lbF, kgF, N, or kN.
A load cell is often integrated into a force gage in some UTMs. A force gage is an integrated instrument that combines the function of a load cell with that of an indicator, or display device.
Test frame
UTMs can test materials in tension or compression. A load is applied with an electromechanical or hydraulic test frame. These machines are based on a variable-speed electric motor, a gear reduction system and one or more screws that move the crosshead up or down. Single column testers are typically employed for applications requiring lower forces, commonly up to 1,500 lbF (6.7 kN). These testers are suitable for bench mounting and can be used in a lab or production environment. Double column testers can be used in some low force applications, but are generally specified in higher force applications. A double column test frame can be configured for bench mounting or floor mounting. Test frames are often driven by one or two lead screws, while heavy duty machines are actuated hydraulically. Customized test frames may be available where column height may be increased to allow the testing of large samples. Control functions to measure distance, return at a limit, or to stop at a break are often integrated.
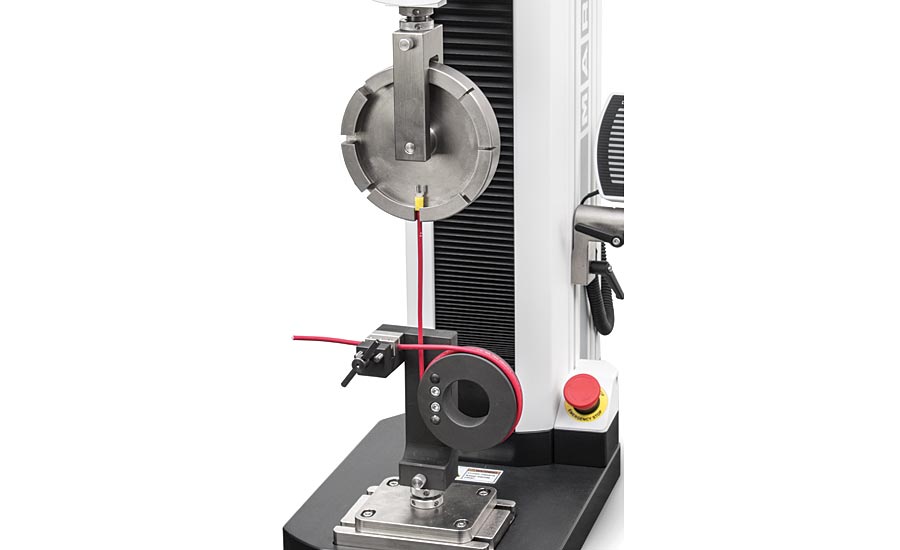
A wire terminal test is performed with a turret-style grip and a bollard-style grip.
Encoder/Linear Scale
In order to calculate stress, strain, or percent elongation, a method of measuring distance, extension, or deformation is required. An integrated encoder or linear scale is employed to measure the travel or response of the sample to the movement of the crosshead of the test stand. In the case of small deflections, an extensometer is used to provide accurate measurement and better resolution by physically clamping onto the sample, or using laser or video to track its deformation. In so doing, extensometers compensate for errors caused by mechanical deflection in the test frame and load cell.
Grips
Selecting the correct grips or attachments is vital to the success of any tensile test. It is important for the grips to properly fit the sample. Precise load alignment during force testing is dependent on the grips, attachments, or fixtures used to retain the sample. Additionally, grips with sufficient force capacity must be selected so they are not damaged during testing.
During the test setup, it is important to watch for sample misalignment and worn grips. Any off-center loading will exert bending loads on the sample and may induce measurement error. Worn grips may also contribute to off-center loading. Uneven tooth marks across a specimen might reveal this problem. Grips should be inspected for wear prior to beginning any tensile testing. The type of grip chosen depends on the type and dimensions of the sample. Grips must be chosen which prevent the sample from slipping or breaking at the grip faces. Non-standard or unusually shaped samples may require custom grips or fixtures.
Pneumatic grips are often selected for tensile testing. A distinct advantage of pneumatic grips is that samples can be clamped tighter, while pressure can be adjusted. After the pressure is set, the air pressure is kept constant throughout the test, preventing slippage. Thinner materials can be tested in this manner. Pneumatic grips require tubing and a source of clean, dry air for operation.
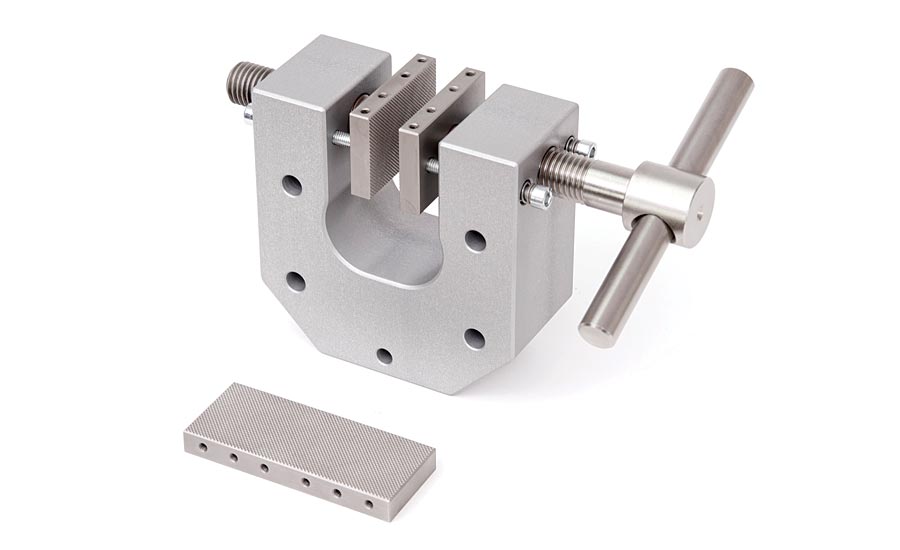
Shown here is a rugged parallel jaw grip with a serrated jaw face.
Plastic dog bones, composites and metals can be tested with wedge grips. Spring-loaded wedge grips work by gripping a material continuously while it thins out as it elongates. The downside is that as the sample thins, the grip automatically tightens further, which will affect the distance measurement. This is not a problem for applications not requiring distance measurement. For force-distance measurements (or stress-strain), parallel jaw grips are a better choice. They do not self-tighten like wedge grips, but are an easy-to-use solution.
Wedge grips and parallel jaw grips can be fitted with various jaw surfaces. If the wrong jaw surface is used, samples may slip from the grips even if the capacity of the grip meets the test requirements. Plain jaws are blank with no coating and can be used with samples that could get damaged with coated jaws. Serrated jaws are recommended for metals and plastics. Diamond coated jaws can be used for paper and board samples, while interlocking wave jaws are often used for fabric. Rubber faced jaws provided the needed friction to secure glossy or slippery materials.
Wire, rope, yarn and tubing require specialized grips to secure each specimen. Wire turret grips are available for wires with terminal or connector ends. These grips have an indexing wheel that contains grooves of varying widths to accommodate a wide range of sample shapes and sizes. For wire or cable without terminals, a bollard-style grip can be used. The wire can be wound around the bollard and through a small vise to secure it. Medical sutures are similar to wire and can also be tested this way.
Specialized grips for film or paper can have interlocking jaws to secure the material. The jaws allow the material to be held without tearing it prematurely. And, last but not least, a pair of hooks, while simple in design, might be the best option.
Software/Analysis
Modern UTMs incorporate analysis software so that data can be collected and organized through tables, charts, graphs, and reports. Typical graphs include representations of force vs. distance or stress vs. strain. Spring rate, Young’s Modulus, and other parameters can be extrapolated for further analysis. When working with a high volume of samples, automated software reduces operator-to-operator error, saving time and repetitive work.
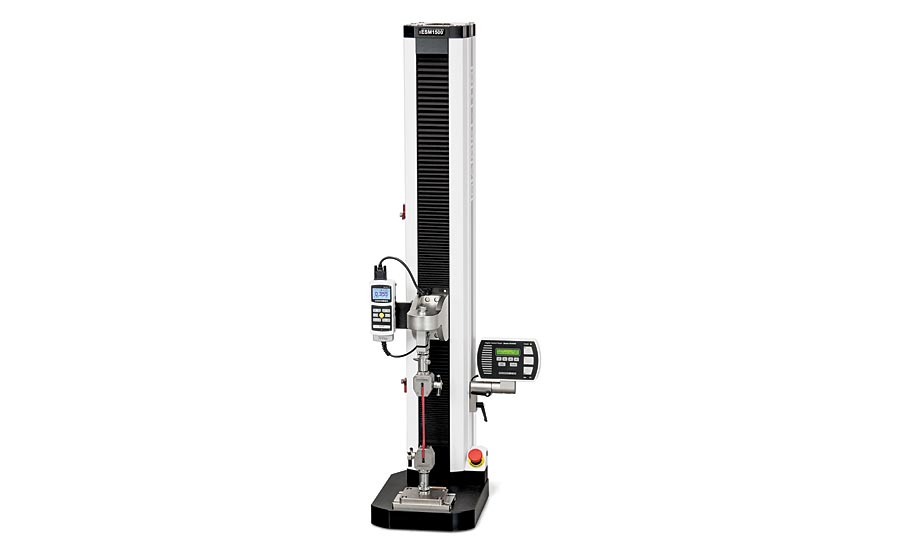
A plastic dog bone tensile test
Conclusion
Tensile strength is an important parameter of engineering materials that are used in structures and mechanical devices. With proper grip selection, engineers and quality personnel will be able to rely on their data to improve their designs, ensure batch quality, reduce material costs, bring products to market quickly, and ensure products are manufactured to international and industry standards.