Have you ever noticed how many manufacturing companies include the word “quality” in their taglines?
Based on our research, the short answer is obvious: a lot, including “Quality Matters,” “Quality is our Top Priority,” and “Quality Starts with You”—just to name a few.
Quality is certainly a point of concern when it comes to releasing new products. Unfortunately, the assurance of a company being in compliance does not ensure the products they deliver are in compliance.
For many suppliers, attaining and retaining customer and industry compliance is primarily a paper chase. Anyone can say they are compliant if they’ve paid money to earn the certification. But simply slapping a certification on a product can potentially mislead the customer into thinking the compliance goes further than it actually does.
When that happens, you can begin to see where the trouble lies.
Companies can mitigate compliance risks by operationalizing requirements into their processes so that compliance comes from performance, not just a piece of paper. It’s this digitization of quality compliance that can reap immediate benefits, and many manufacturers rely on modern cloud software for this kind of assurance.
Keeping up to date with changing requirements while keeping the business operating profitably and in compliance is critical. It’s imperative to find a system that minimizes the risk of being out of compliance. It can provide peace of mind for company leaders who are accountable, but are not necessarily in control of, compliance procedures. And a consistent workflow engine can enforce procedures and approvals that force compliance in real time before other steps can be taken.
And it doesn’t matter what industry you’re working in either.
Whether you are working toward certification via the Food Safety Modernization Act (FSMA) or the International Automotive Task Force, you must commit to what you tell your customers you are going to do by exposing your documentation process, as well as do what you committed to do, proven through reporting, audits or the like. They sound the same, but there is a subtle difference: you have to ensure you do the work you promised. This is what most compliance auditors look for.
Of course, the inherent challenge is that the people who submit and manage the compliance documentation are not necessarily the same people who perform the work that must comply with the documentation on record. This is where the possibility exists for a disconnect. By turning to software to govern operational behavior, you can take many critical items off your worry list, freeing up the compliance team to do better work.
When auditors begin a task, they determine how your procedures link to the specifications in the relevant standards. Ideally, the documentation is linked directly within the quality management system already. This perfect scenario allows the auditors to easily follow the breadcrumbs that get them from incident to documented procedure to evidence in the least amount of time. If you’re on the path to digitization—or you’ve already arrived there—this process becomes reality.
When we dive deep into compliance, there are really two areas of compliance where the greatest change can come through digitization: industry and customer.
If we break down how you can digitally transform your compliance, it’s imperative that we look at it from these two angles.
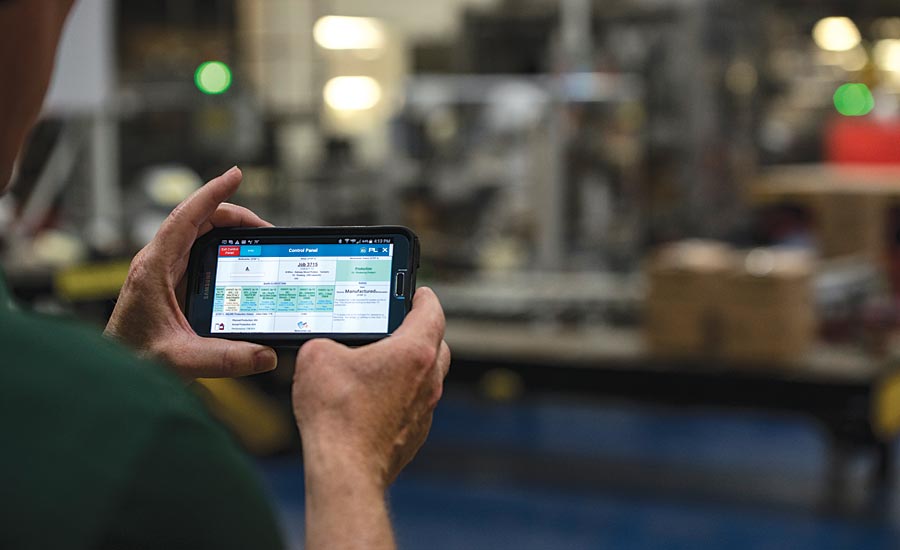
Operationalizing quality enables control plans to actually control the order of operation, the material that is required, and when inspections should occur.
Industry Compliance
Operationalizing quality enables control plans to actually control the order of operation, the material that is required, and when inspections should occur. In a sense, compliance comes for free with pre-determined procedures controlled by software.
If you haven’t met all of the requirements, you can’t move ahead until all protocol is met.
One of the quickest ways to see the benefit of digitally transforming your quality compliance is when it comes to traceability. This means having the ability to quickly scan reams of documents in the event of a recall or audit.
In the past, this involved an all-hands-on-deck approach to sift through paper documents that were stored away in cabinets in a dark, forgotten corner of the office—sometimes for days.
With a digitized system, it’s as simple as building a search query to pull the necessary information, which is invaluable when a request for information comes with a quick turnaround timeframe. (The Federal Drug Administration, for instance, requires a written response in four hours.) Reducing search time from days and hours to minutes makes everyone’s lives easier. This includes Hausbeck Pickle Company.
Hausbeck produces an average 400,000 pounds of pickles or peppers a day for some of the world’s largest fast food restaurants including Subway, Burger King, Domino’s Pizza, Taco Bell, and KFC. Their traceability requirements include sourcing back to the cucumber seed, and the farm it was grown on. Prior to adopting a cloud software system, the company would have to look through pages of paperwork, taking up valuable human resources and time. Now, they can complete a mock recall from store to seed in minutes.
Customer Compliance
We are finding it increasingly common for OEMs to build their own compliance reports on top of what the industry demands to address specific business demands. This makes compliance a bigger priority, but also can increase the level of complexity.
The automotive industry, for example, follows the Materials Management Operations Guidelines/Logistics Evaluation (MMOG/LE) which outlines best practices for the supply chain to align with the expectations of their customers. The goal is to institutionalize processes as much as possible versus simple documenting procedures that must be trained and policed in order to be effective. The goal is to not only streamline delivery of predictable quality, but mitigate the supply chain risk as well.
This is a particularly important area of approach. When thinking about a risk strategy, one should consider how Industry 4.0 will have an impact. The adoption of the Industrial Internet of Things (IIoT) has accelerated in recent years, and with it, many initiatives for quality improvement. In a recent report by LNS Research, all of this is wrapped up into what they call Quality 4.0.
LNS Research urges suppliers to “think risk performance, not compliance.” A supplier’s capabilities and performance, when it comes to quality and risk, may be monitored closely by its customer base as a scorecard to assess the supplier’s status and suitability for contract awards. In fact, quality data is one of the most-shared pieces of information externally. Increasingly, a supplier’s risk profile can impact sourcing decisions and audit plans. If the supplier’s scorecard is trending in the right direction, it will have a positive impact on operations, customer oversight, and new contracts.
When it comes to quality and risk, this information should be conjoined from initiation through to the end of its lifecycle. By doing so, you’re allowing lessons learned to influence future sourcing decisions. Having all of this information digitized along the way is a sure path to gleaning information and keeping it in one easy-to-reach place.
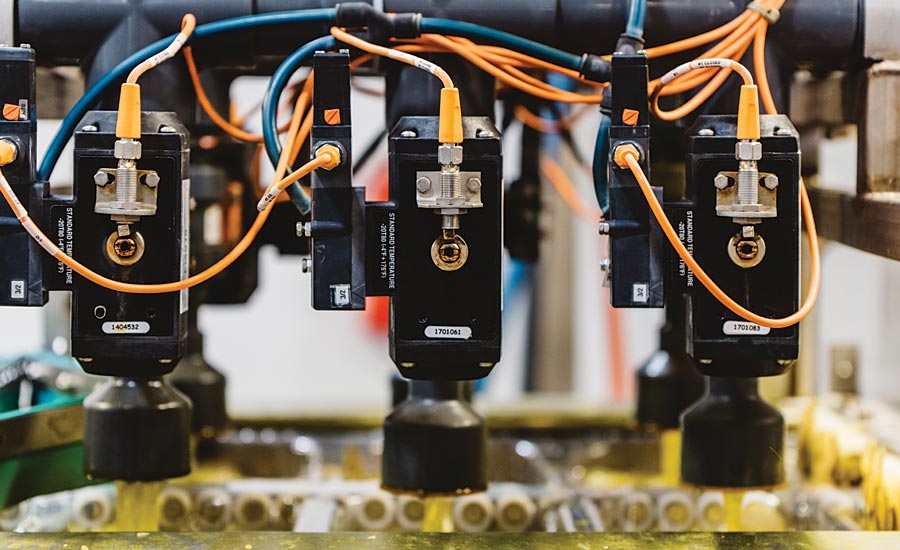
Digitization of quality compliance can reap immediate benefits, and many manufacturers rely on modern cloud software for this kind of assurance.
How to Build a Culture of Compliance
It’s important to ensure leadership is on board and aware of any and all digital transformational efforts so that they feel involved in the development and oversight of the quality system. With a compliance system in place, these important individuals will be notified of quality plans that need reviewing before re-certification requirements are due. This saves time and money, and ensures the company isn’t scrambling at the last minute to comply with customer or auditor requests.
And because no one can envision every possible scenario, a robust compliance system includes a well thought out contingency plan. If you are digitizing your quality process, these plans can be documented directly within the compliance framework to ensure critical steps are not overlooked when something doesn’t go as planned. You can clearly outline customer communication procedures such as through text messages and email alerts that are set up ahead of time. This reduces setup time and ensures everything is in place where and when it needs to be.
Finally, it makes more sense to back up your historical data in the cloud than it does to store everything in a place that could be destroyed by natural disasters or some other calamity. Imagine coming to the realization after a tragedy that your historical documentation will never be recovered. If that’s not a case for digital transformation, I’m not sure what is.
If you’ve given thought to digitizing your quality compliance, but have been shy about pulling the trigger, perhaps what we’ve outlined above will help push you toward making the decision.