Several critical components need to come together to form a machine vision system. This includes the sensor (typically within a camera) that captures a picture for inspection, the processing hardware (a PC or vision appliance) and software algorithms to render and communicate the results. In addition, lighting, staging, and lenses are required to set up a machine vision system.
Machine vision systems can automate complex or mundane visual inspection tasks and precisely guide handling equipment during product assembly. Some of the many machine vision applications for quality inspection include positioning, identification, verification, measurement, and flaw detection. Unlike human inspectors who can process only so much information at a time, a machine vision system will work tirelessly performing 100% online inspection, resulting in improved product quality, higher yields, and lower production costs. High quality, together with consistent product appearance and functionality, drive a positive customer experience and ultimately market share.
This article will focus on machine vision inspection, and how different applications can benefit from 1D, 2D, or 3D sensors and cameras. We’ll also explore how 2D and 3D inspection are converging for solutions to more complex inspection applications.
1D Vision Systems
Line scan cameras use 1-dimensional image sensors to analyze the digital signal one line at a time, essentially inspecting a straight line. One-dimensional vision systems are generally looking for variances from line to line, building a large 2-dimensional image from the accumulation of lines, much like a photocopier. Common applications for line scan cameras include web inspection, where materials such as plastic or paper are inspected in a continuous sheet or web, and large object inspection where multiple cameras compromise inspection accuracy, as well as all other inspections like 1D bar code reading or optical character recognition (OCR).
An example of a line scan quality inspection is Integro Technologies’ automated inspection of paper, huge rolls measuring 2 meters in diameter and 1.5 meters in width. The inspection system both reads the linear barcode on the label and inspects the paper roll for any smudges, specks of dirt or other debris in the shrink wrap. To meet the specifications of the customer, Integro utilized Teledyne DALSA’s Piranha XL Multi-line CMOS TDI color camera and an Xtium-CLHS PX4 frame grabber for high speed, high data throughput, and low noise.
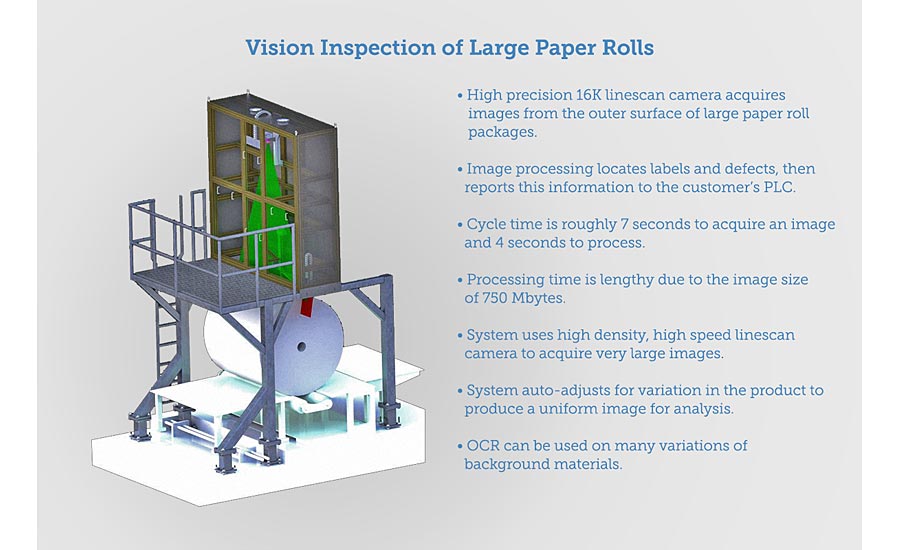
Line scan (1D) inspection of paper roll. Source: Teledyne DALSA
The camera’s time delay integration (TDI) feature is highly useful for Integro’s inspection system, due to the need for maximum sensitivity. TDI is a method of line scanning that permits greater scanning speeds in low light or at reduced lighting levels and allows for the accumulation of multiple exposures of the same moving object, making it ideal for high-speed web inspections.
2D Vision Systems
Area cameras use 2D sensors to view an area based on the two dimensions of length and width. This type of system can inspect an area such as a matrix code, labels, and is ideal for looking at discrete parts. With area cameras, the vision system essentially takes a two-dimensional snapshot of the object to inspect (line scan cameras can also build 2-dimensional images by building an image line by line).
An example of a 2D vision system is Comm Port’s under-vehicle inspection system (UVIS). Comm Port uses state-of-the-art color area cameras to inspect for explosives, contraband, or hidden compartments. The cameras are capturing images of the underside of vehicles or other equipment entering and exiting a facility. This ensures the safety and security of a facility, and acts as a deterrent toward terrorist attacks and sabotage. The challenge is to provide high-resolution images captured at driving speeds, with real-, or near-real time processing, and to transfer necessary information to authorities without delaying entrance and exit to and from the facility. Teledyne DALSA Genie cameras form the backbone of this Comm Port system.
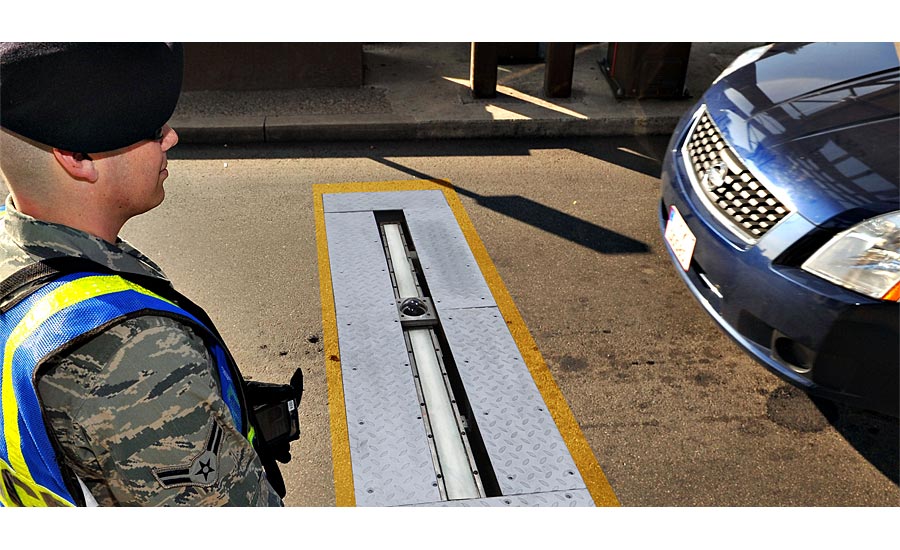
A fixed setup of the Comm Port system at a checkpoint. Source: Teledyne DALSA
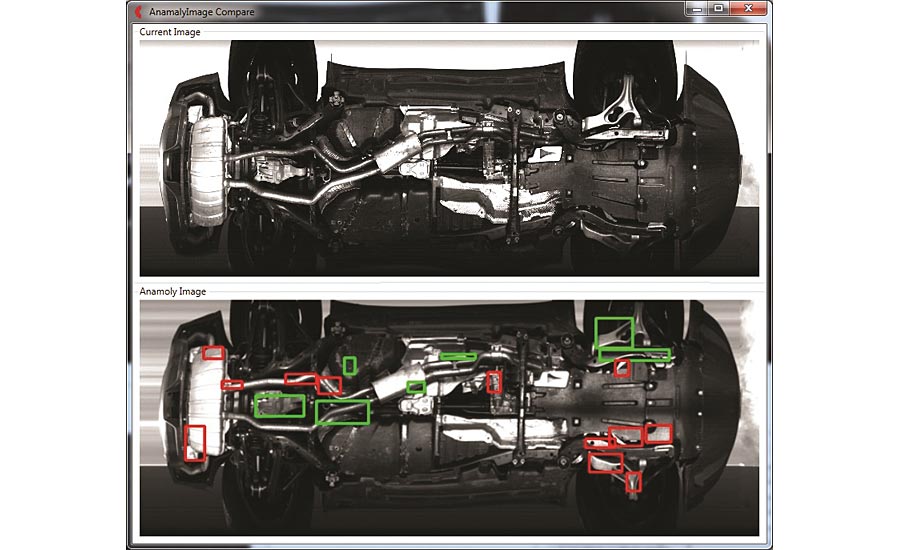
The advanced software technology provides instantaneous results. Source: Teledyne DALSA
The Addition Of 3D Vision Inspection
Three-dimensional quality inspection is now being added to the lineup with powerful, innovative 3D sensors that look at length, width, and height. Using laser triangulation, high-resolution, real-time height measurements are captured for industrial imaging and factory automation. 3D inspection is ideal for in-line metrology, volumetric measurements, parts inspection and identification, and bin-picking applications for semiconductor, electronics, factory automation and logistics.
An application where inspection combines 2D and 3D inspection is toilet production, which is surprisingly complex and difficult to automate. Due to the curvature of the porcelain and its reflective quality, toilet bowls present a unique set of quality-control challenges. With human assembly, it takes as many as 20 people five to six minutes to assemble and inspect a standard toilet. These quality checks occur at several points during the manufacturing process. To automate the production line, this manufacturer used 20 cameras to complete the inspection tasks and robotic functions, the bulk of which were Teledyne DALSA BOA smart cameras. These smart cameras validated quality, located parts, confirmed label placement, or guided robotic pick-and-place actions. A Teledyne DALSA Z-Track 3D laser profiler performed the final inspection with help from a software platform able to apply both 2D and 3D algorithms to its image data.
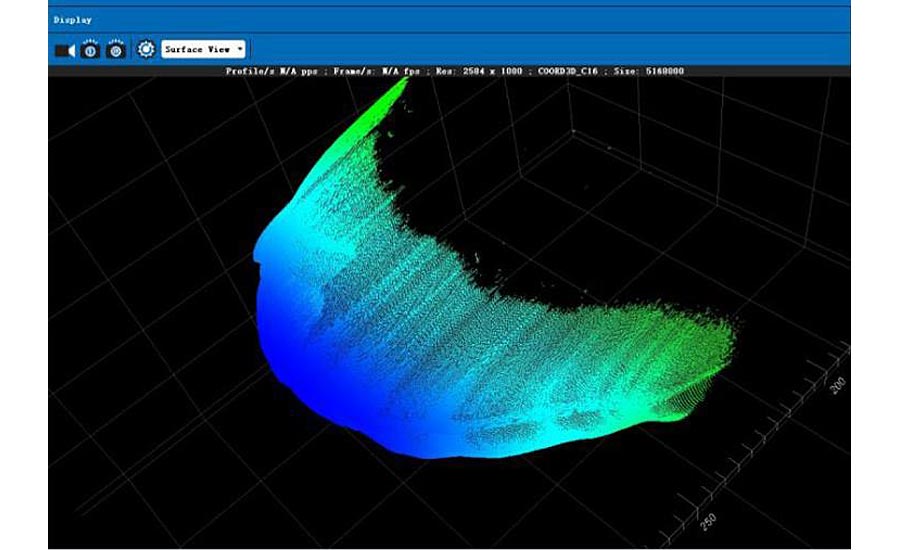
3D inspection of a toilet for real-time height measurements. Source: Teledyne DALSA
The combined use of 2D and 3D machine vision was instrumental to automating this production line and achieving significant benefits in terms of time, labor costs, and increased quality. With automation, it now takes 65 seconds to assemble a toilet on this line instead of five to six minutes.
Conclusion
These real-world applications demonstrate how 1D, 2D, and 3D imaging, together with processing and software technologies can enable higher quality, reduce costs, and increase speed, via machine vision quality inspection. In addition, with machine vision inspection, defects are found early in the manufacturing process, and components can be rejected or fixed before final product assembly, saving both money and time.
For more information, visit http://www.teledynedalsa.com/