Manufacturers use materials testing to determine the mechanical properties of materials, components, and products. By stressing a specimen in tension, compression, or flexure, its properties can be measured against recognized performance standards such as those published by ASTM, ISO, and other organizations. Since materials testing is used to verify that materials and products perform as expected in their end use applications, a robust testing program is a vital part of any quality assurance process. Disruptions to your testing program can result in delayed shipments, upset customers, and lost revenue. For this reason, it is crucial to ensure that measures are being taken to prevent system downtime when planning the introduction or evolution of your testing program.
To avoid the costs and risk associated with testing downtime, companies often outsource their testing to third party labs. However, third party test facilities are highly expensive and come with other associated risks, such as higher chances of incorrect test procedures being used and a greater risk of compromised data integrity. In-house testing is generally preferred, but many manufacturers are concerned about the costs and downtime risks of an in-house program. In order to make an informed decision, they must take into consideration the quality of the testing equipment and the ability of their equipment provider to service and upgrade their equipment.
If you are interested in purchasing new equipment to bring your testing in-house, increase your testing capacity, or update your lab, it is important to ensure that you are investing in a quality system. Outsourced testing is an expensive operation; however, the cost of a new system may lead you into exploring more budget friendly options. It’s important to note that budget model systems come with hidden costs, and while a cheaper device may save money upfront, this equipment is likely to have a shorter lifespan and performance limitations that can ultimately lead to downtime.
A system’s physical durability and design specifications are key measures of excellence. High quality systems will have well-engineered performance specifications and features tailored to optimize usability. Simple features such as a durable work surface and ingress protection to prevent internal electronics from failing can be critical for ensuring reliability and longevity in your system.
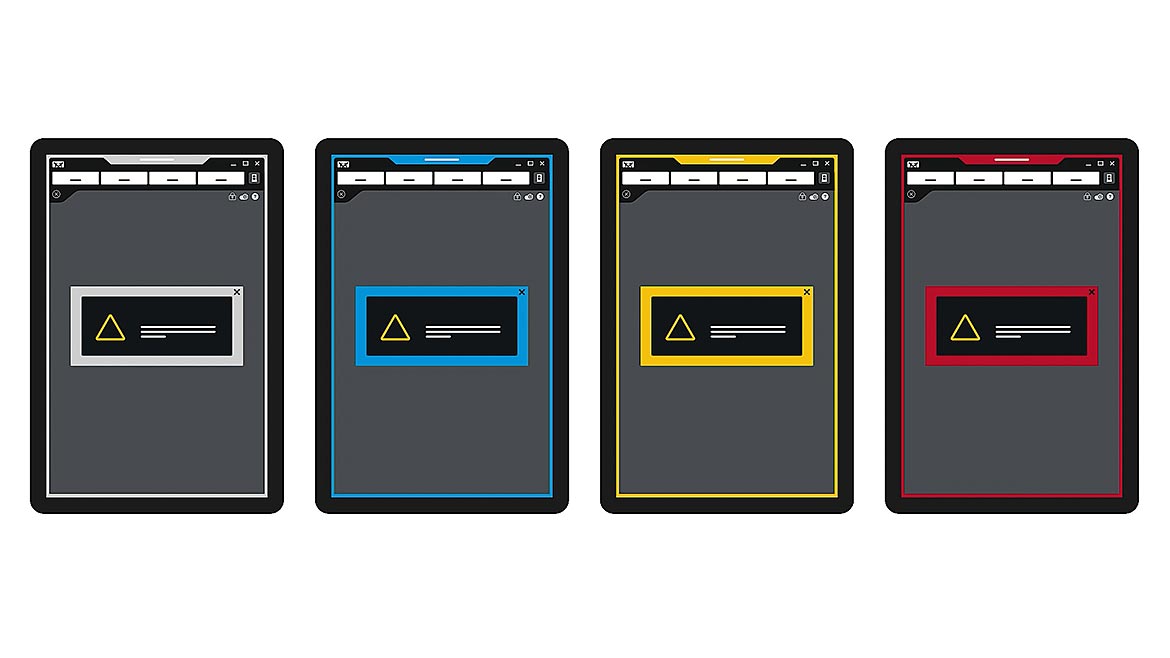
Material testing software that includes built-in safety coaching provides clear visual feedback regarding system status at all times, making it easy to know when it’s safe to interact with the system.
Another potential cause of unexpected downtime is safety-related accidents involving the test operator. Flying debris and fast-moving parts can be a hazard for operators in a destructive test environment. Some test systems include features that are designed to help mitigate the risk of these incidents. Safety features allow test operators to work with confidence, and help to avoid dangerous and costly accidents. Be sure to ask your operators which features would help them operate the machinery safely and with confidence. There is a good chance that your equipment supplier can provide additional options to meet these needs or elaborate on details that may be already integrated into the product. Some examples of these features include operator protect, limit stops, collision mitigation, and enhanced ergonomics.
Testing equipment should be able to be supported for the majority of its lifespan, as a provider’s ability to proactively service their equipment is critical for preventing downtime. When considering a machine, ask if you can review its product life cycle - a document that outlines the evolutionary stage of the device – designed to help you plan for the evolution of your lab and take preventative measures to mitigate downtime events before they arise.
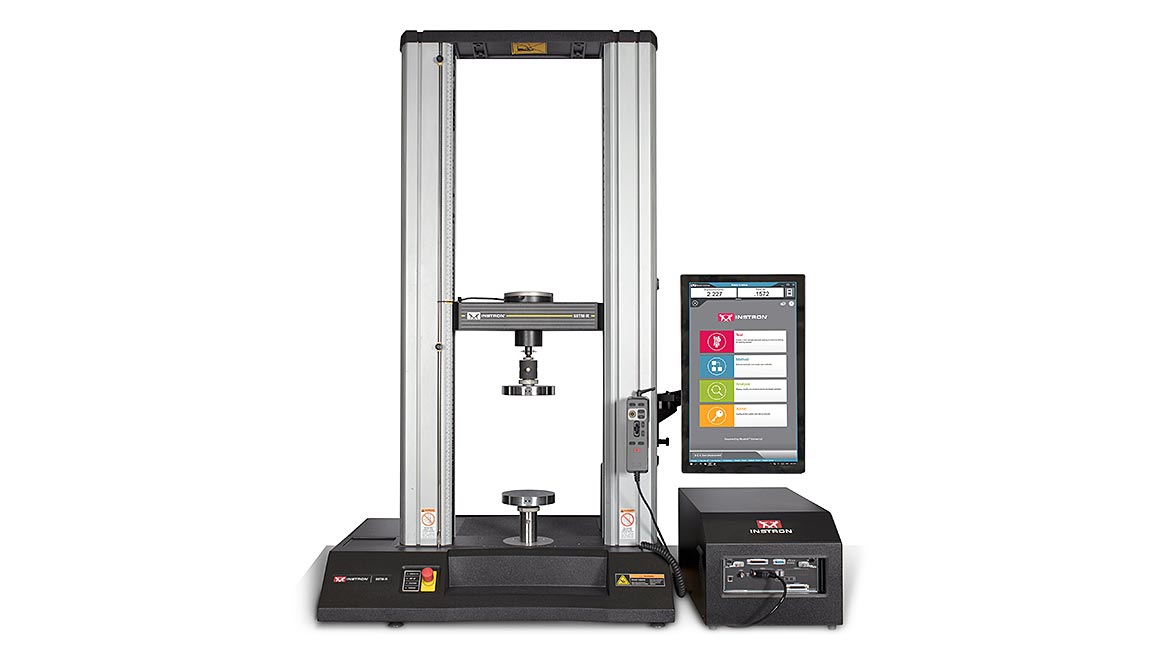
Some legacy testing equipment can be retrofitted with modern control electronics and software, extending the life of the testing system and allowing labs to take advantage of the latest features and accessories.
Maintenance or repair-related downtime can be frequent or unexpected, which makes service turnaround time critical. Many manufacturers test extremely high volumes of material, and the impact of downtime can be significant in terms of shipment delays and lost revenue, even if only a single testing system is taken offline. Your provider should have highly skilled service engineers local to your facility who can quickly and efficiently get your machine up and running again. When considering providers, be sure to inquire about the local service engineers and the estimated time it takes for their representative to arrive on site. It’s even better if that service provider can offer a lab inspection that reports on the lifecycle status of your system’s key components. Lifecycle reports also create a risk assessment profile and recommend upgrades to improve the reliability, productivity, and overall capabilities of your testing lab.
If you choose to move forward with a premium provider, you will receive a high-quality system built to last for more than a decade. Because of this, many testing machines remain in use well into their later life cycle stages. Though hardware-related downtime can often be avoided with quality equipment and robust service support, trying to acquire electronics for outdated devices can be very challenging, and while a premium quality device may allow for extensive long-term use, their extended lifespan can eventually make some of their components obsolete. Should your outdated electronics or software fail, you may be left with a nonfunctioning system that needs a complete retrofit or replacement. For this reason, it is important to use preventative measures for equipment in its later lifecycle stages, as critical components – if available - can have very long lead times, as can new systems themselves. Manufacturers who find themselves in this position are in a very challenging situation, as they will need to outsource the testing during this downtime and obtain funding for new systems or large upgrades.
Equipment providers who offer high quality service support and tools such as lab health checks are key to helping you understand the risks currently facing your system and take preventative measures to keep your lab up and running. Often the solution is to perform a system upgrade, or retrofit, which repurposes the functional components of your systems while upgrading many of the components that are subject to aging, such as software and electronics. By modernizing the core components of your system, you can remain in an early lifecycle stage, utilizing modern features that would otherwise only be available by purchasing a new system. Retrofits allows a system to continue functioning while maintaining supportable lifecycle parts, features, and software.
Testing system downtime causes shipment delays, upset customers, and lost revenue. Failed components, operator safety incidents, and serviceability all play a role in the expenses related to system downtime. To prevent and reduce these risks, any new testing system should be vetted not only for its upfront cost but also for its long-term ability to perform, for the provider’s ability to service the equipment, and for the potential for the system to be upgraded in the future. Choosing a provider who focuses on these areas will ensure that your investment will be able to withstand many years of use. By knowing your options, you can be confident that your device will be capable of preventing the undesirable side effects from testing downtime.