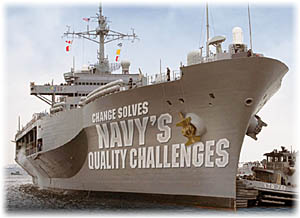
In describing the role of the Navy's Interface Assessment Division of which his lab is part, Michael Wheeler, manager, Gage and Standards Laboratory says, "Some people call us the ‘Consumer Reports' of the Navy."
The Interface Assessment Division, a unit of the Naval Surface Warfare Center (NSWC, Corona, CA), uses its precision measurement capabilities, traceable to national standards to ensure the form, fit and functional requirements of physical interchangeability and mechanical interoperability as specified by the Navy. Wheeler says, "Our efforts support the warfighter by providing structured, proven interface control practices and precision measurements for maximum efficiency, flexibility and safety of battlefield weapons systems. The idea is to solve mechanical interface problems before they happen, that is, to ensure that interchangeability occurs as intended."
Interchangeability is a critical element of product quality with far-reaching implications for the safety, performance and cost of weapons systems. The purpose of interchangeability is to ensure that weapon components work together seamlessly, without selective assembly or modifications. The Interface Assessment Division ensures the interchangeability of weapon systems and sub-systems, solving problems before they happen in combat. Ensuring interchangeability through interface control is essential for successful deployment of battlefield weapons systems.

Standards ensure interchangeability
To ensure the standardization of measurements necessary for interchangeability of weapons and combat systems subassemblies and components, the Navy's Product Engineering Assessment Department operates the Measurement Science & Technology (MS&T) Laboratory comprised of the Standards Laboratory and the Gage Laboratory operating out of a 39,000-square-foot facility featuring state-of-the-art environmental controls and precision measurement instruments directly traceable to the National Institute of Standards and Technology (NIST).
The two laboratories employ some of the most accurate optical, dimensional, force and gage measurements in the Navy and play critical roles in maintaining interchangeability through gage certifications and standards calibrations.
Because of the MS&T lab's capabilities, the Navy, Marine Corps, Air Force, Army, Coast Guard, NASA, the National Science Foundation and others also come to the facility for specialized interface assessment and calibration services. In addition, calibration services are provided to fleet and field labs, shipyards, Fleet Ballistic Missile shore-based facilities and defense contractors.

Systems complexity
The Gage Certification Laboratory is responsible for the Special Interface Gage Program that supports and provides certification of interface gages and tooling, master tooling and other associated tooling requiring dimensional certification.
Certified gages are shipped daily to front-line field units and deployed ships, including the supply of more than 750 Marine Corps units across the globe with certified and calibrated gages. As many as 12,000 light weapons gages are shipped per year, as well as several hundred ships and defense contractors. Driven by the procurement of ever more complex systems, the volume and diversity of certification measurement work is on the rise.
Wheeler says, "We need to measure a wider variety of special interface gage sizes than ever before-from gages a couple of inches in length that you can hold in your palm calling for a tolerance of
± 0.0001 inch-to large gages in excess of 10 feet in diameter and weighing 7,000 pounds and calling for a measurement tolerance of 0.0005 inch to 0.001 inch.
"We do first-article inspections on new procurements as well as periodic re-inspections of gages returning from the field where the end user may be a defense contractor using our gage to assemble or inspect a weapon system or subassembly," Wheeler says. "Alternatively, the end user might be the warfighter, requiring a gage to validate the safe operation of a weapon, for example to check an infantry weapon or a large gun barrel to check for wear which would make the weapon unsafe to fire."
The typical life of gages varies, but there have been some that have been in use for more than 20 years. There is a regular recertification cycle for each type of gage; most are not used just once, but come back roughly on an annual basis to be remeasured and recertified. Infantry weapons gages experience high turnover, especially those used in Iraq and Afghanistan. With the gritty, sandy, abrasive conditions, gages are subject to a lot of wear. Consequently, when the gages come back for recertification, many have to be replaced. Other gages, such as those used in sophisticated manufacturing environments, experience less wear so the recertification cycle is longer.
"The need to increase gage lab throughput caused us to seek ways to increase efficiency while maintaining accuracy. In other words, we needed to increase productivity," Wheeler says. "Examining our options led to realization that an effective way to advance the lab's metrology operations was to replace our old CMM (coordinate measuring machine), with its 20-year-old technology, hard-to-maintain through-hole circuit boards and vintage software, with a state-of-the-art CMM."
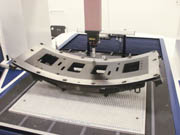
Seeking the optimum solution
To determine the best CMM for their requirements, the Gage Lab conducted a market survey of potential vendors. Next, they reviewed candidates on-site and in vendor showrooms, as well as entertained presentations from five different CMM manufacturers.
According to Wheeler, "As a result of our selection process, which included extensive testing, we believe the Mitutoyo Legex 12128 was the best value, offering optimum flexibility to measure the wide range of gage types and sizes while maintaining the ultra precision critical to our requirements. As a matter of fact, the Legex's ISO accuracy specification (ISO-10360-2, 0.6+1.5L/1000µm) was a deciding factor. Once we made our choice, we handed off the results to our procuring agency-the Federal Industrial Supply Command-where they confirmed our purchasing recommendation with an independent review. In total, the procurement process required a nine-month effort from research through procurement and delivery."
After installation, the Gage Lab measured the uncertainty of the Legex CMM's probing performance, which was found to exceed the published specification.

Advanced CMM operations
The Legex CMM is used with a Renishaw PH10MQ/TP7 EP indexable touch-trigger probing system, as well as a Renishaw SP25M scanning probe. The Legex also could be fitted with a vision system, but according to Ken Harrell, Gage Lab technician, "Before we deploy vision systems on the Legex, we'll want a set of methods and standards able to associate vision data together with touch-probe data. We're still in the ‘looking' stages on that.
"The CMM is efficient," Harrell continues, "because we need to compare gage features located in terms of the design datum structure vs. actual geometry. In a single setup, we get a three-dimensional picture of a gage-a picture that is difficult to achieve with multiple, open setups. The advantage of the CMM is that it reduces uncertainty, especially for more complex geometries. One reason is that the staging requires less clamping pressure, which translates to less of a need to compensate for distortion. And compensation can increase the chance for error and thus, for uncertainty. Also, since the CMM ‘flies' all around the gage, measurements usually do not require multiple stagings, again reducing uncertainty. Because the gage can be staged in the orientation in which the actual article will be used, the force of gravity will act on the gage in the same way it will on the article, again reducing, or even eliminating, compensation for that factor."
Citing an example, Harrell describes a Trident submarine missile door gage recently certified: The door gage is used to measure the access hatch door to the missile loading tube used both to transport Trident missiles and to load them into a sub. "The article has a radius of 45 inches but our gage provides only 20 degrees of arc available for measurement, and we have to maintain the profile to less than 0.002 inch. The gage is about 38 inches across and has 14 hole-features that are at precise angular relationships to the radius, and with positions that must be located in relation to the radius with a tolerance of less than 0.002 inch."
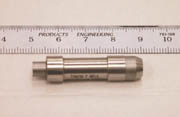
Productivity
Mitutoyo supported start-up of the Gage Lab's Legex operations with a one-week training course on MCAT, their metrology software package. Characterizing the software, Dave Nelson, another Gage Lab technician, says, "MCAT software is very intuitive, and after about a month, maybe less, we were able to get programs rolling and gages certified. Consider that now we are able to measure 50 Marine Corps M-4 rifle head space gages at one time in batch runs."
Wheeler agrees that the new CMM has boosted productivity, "So far, taking into account all measurement activity undertaken on the Legex, we are calculating savings of more than 40% compared to open set-up methods."
The team at the Gage and Standards Laboratory of the Navy's Interface Assessment Division is small, just 17 people, but it leverages every technology to achieve the highest levels of performance. It has to.
"People's lives depend on the work we do here," Harrell says, "Consequently, we take it very seriously. When the fighter in the field pulls the trigger or activates a system, we want to make sure it works, to help keep our guys on the winning side. Everything that goes out of this building has to be right." Q
Chris Bonnett is a CMM product manager at Mitutoyo America Corp. (Aurora, IL). He can be reached at [email protected] or (630) 723-3643.
Tech tips
• Interchangeability ensures components work together seamlessly, without selective assembly or modifications.
• The Gage Certification Laboratory is responsible for the Special Interface Gage Program that supports and provides certification of interface gages and tooling, master tooling and other associated tooling requiring dimensional certification.
• There is a regular recertification cycle for each type of gage; most come back roughly on an annual basis to be remeasured and recertified.
Issues Affecting Interchangeability
• Items are acquired from multiple sources, possibly various countries.
• Acquisitions involve numerous production contracts.
• Acquisitions have lengthy periods between production contracts.
• Numerous configuration items within the system are produced separately.
• Items are assembled away from the production site or after periods of storage and handling (shipboard, depot, etc.).
• Items may, over their life cycle, be assembled to several different systems due to strike-up and strike-down operations.
• Items require repair and maintenance for the life cycle of the system.
• Items interface with hardware in existing inventories.