
Locating markers on a casted part is one capability machine vision offers. Source: Tordivel AS
PC-based machine vision became the industry standard 15 years ago, and today these solutions live side by side with vision sensor solutions. Ten years ago it seemed strange that all the innovation was concentrated on vision sensor systems. This seemed certain to change, but the same paradox is true today. A number of factors are now rapidly changing the position of PC-based solutions.
The most important are the following:
Many reasons to choose PC-based solutions to vision sensors exist, but the most important are:
GigE Cameras
With GigE cameras it is easy to connect multiple cameras to one computer without worrying about cables and cable lengths. Standard Cat5/6 cables can be 100 meters without a repeater. Using standard cabling makes vision system deployment much easier. The second-generation GigE cameras now feature Power over Ethernet (POE), further reducing cost for cabling and power.GigE cameras are true machine vision devices and the operator can control every aspect of the cameras from the machine vision software statically or dynamically.
A serious drawback with the GigE standard is that the cameras use User Datagram Protocol (UDP) and not Transmission Control Protocol (TCP). The implication of this is that it is not recommended to send the image data on an IP-network used for other purposes. The design focused on maximum image throughput and minimum latency. Losing images and getting the system going after network drop is not handled by the standard. In most cases a single retransmit is the only measure.
One could conclude that GigE cameras are very similar to FireWire cameras; the only real difference is the cabling and transport protocol.
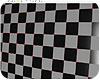
This is a 3-D chessboard camera calibration. Easy-to-use 3-D calibration based on reference objects or chessboard patterns will form the basis for accurate machine vision solutions. Source: Tordivel AS
Network Cameras
Network cameras or IP cameras designed to be used in surveillance applications are using file transfer protocol (FTP), a secure protocol. These cameras handle network drop and can be configured to reduce the bandwidth requirement when needed. This makes these cameras suitable for wireless machine vision. Another important feature is the built-in image compression. Image compression can be used without losing information content in most machine vision solutions. The last significant feature for network cameras is the built-in Iris control. This can be used to make unshielded or even outdoor machine vision solutions.Multi-core and GigE means that multiple systems run on a single computer. A machine vision server can run multiple vision systems on one multi-core computer. With the right software, standard IO and standard GigE cameras, there is a great potential in hardware savings.
Impact of Multi-Core Processing
The impact of multi-core processing is big. In addition to running multiple systems on a single computer, it will improve real-time capabilities of PC-based solutions by, for example, using a separate core for IO or dB access.Three-dimensional stereo vision is three times faster with multi-core. In 3-D, the stereo-vision feature location is computer intense. To make a robust system, the same feature has to be located in three images. By processing the images on separate cores, the system is three times faster with a quad-core processor. If it takes 750 milliseconds to locate the features in each image, the cycle time without multi-core software would be 2,250 milliseconds, with the proper software less than one second or 750 milliseconds. This performance improvement is very significant.
Multi-core increases machine vision speeds up to 10 times. Intel and AMD are continuing to develop more and faster cores. This has increased the performance benefit of using a PC-based solution and will in the future make having multi-core aware software a requirement.
In addition, PC-based smart cameras have been around for a couple of years. The most important feature of these devices is the form-factor, which is related to size. The devices’ compact size is critical. All one needs to get a system running is to mount the camera on a robot or over the conveyor. This saves a lot of space and thus cost, compared to a standard PC solution.
A PC allows one software solution for all vision systems. The existence of open and PC-based smart cameras removes the link between proprietary vision sensors and their companion software support. PC-based hardware covers the requirements from vision sensor to high performance machine vision servers. It is now possible to use one standard machine vision software platform to develop all one’s vision solutions.
By combining PC-based smart cameras and GigE cameras, cost-effective vision systems are possible. This is the power of combining standards such as TCP/IP, a PC and cameras. Three-dimensional stereo vision is available by using a multi-camera vision sensor and 3-D machine vision software.
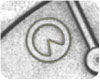
This sub-pixel marker location improves 3-D stereo vision accuracy. Source: Tordivel AS
What will the future bring?
Today a revolution is taking place in the field of industrial inspection and automated camera systems. The revolution is driven by software on computer-based systems or on vision sensors. This is a critical ingredient in numerous cutting-edge manufacturing or automation solutions.With software-driven vision, it appears software will be used to create tools for users. In these tools configurability, customization capabilities, image analysis and process insight are important but presented so that operators can use vision systems without special training. Today, numerous opportunities are ready to be exploited for those who know the best machine vision frameworks.
The Rise of True Non-Programming Libraries
The library approach of making machine vision solutions is old-fashioned. PC-based vision rapid application development tools for 2-D and 3-D machine vision are available that produce better and more reliable applications-five to 100 times faster from idea to working application than systems based on a standard library approach.
3-D Machine Vision
Three-dimensional machine vision is a natural evolution of 2-D machine vision. Robot vision adding 3-D capabilities will just make the solution more accurate and reliable. In 3-D, it is important to have the ability to validate the result and to detect that the estimate is wrong.
Easy-to-Use 3-D Camera Calibration
Easy-to-use 3-D calibration based on reference objects or chessboard patterns will form the basis for accurate machine vision solutions. The calibration describes the camera’s intrinsic and extrinsic parameters.
True Sub-pixel Measurement
The typical root mean square (RMS) value for a good 3-D calibration is 1/10 of the 2-D pixel resolution, providing the basis for sub-pixel 3-D stereo vision.
In modern manufacturing, the concept of flexible automation is particularly important. This is the interaction between machine vision, robots and IT-driven automation. On this basis one can realize flexible production lines where the time for adaptation is almost eliminated. The machine system’s primary task in the modern factory is to locate and identify objects so that the robots can grab them and know what to do with them. By connecting the systems to the Internet, it is possible to enhance and maintain the systems without being in the factory. V&S