If you’re looking for more data in less time, 3D scanning may be a good choice for your application.
Consider a CMM. If you need to get information for 100 measurements, that takes a certain amount of time. But with 3D scanning, this same information would be available after one scan. The accuracy is not a fit for precision machining applications, but the tradeoff in speed may make up for it.
Ian Scribner, portable 3D scanning product sales manager, industrial metrology business group, Carl Zeiss Industrial Metrology LLC, explains the differences in technology.
“The overall advantage to traditional metrology equipment, CMMs, gages, calipers, is painting an entire picture,” Scribner says. “Three-dimensional scanning captures more information.”
With some technologies, “it may be possible to identify that a feature is incorrect, but hard to identify how the material came to be incorrect,” he says. The part may be out of spec, but the important thing is to trace back how this happened, Scribner says. “How did it get there?” Perhaps warpage led to it being the wrong size, but this is hard to determine unless you scan the entire part, he notes. Once you do, then you can undertake a root cause analysis.
“It’s just about more information as well as speed,” Scribner says. “Scanning a part vs. a traditional CMM, it’s a bell curve. For every feature that you inspect on a CMM, 100 features takes X amount of time. For 3D scanning, as you scan, as long as the computer can crunch the data, you get more information, faster. You sacrifice a little on the accuracy, but with more information faster, this can help you change something in the manufacturing process. It’s proactive vs. reactive.”
Along those lines, integrating metrology and 3D scanning can help reduce tooling design time and recuts. In terms of tooling design, with smaller plastic components, particularly those with multiple cavities, cavity #1 is often not the same as cavity #2, Scribner notes. In this case, if you’re creating a new tool for a new component, it’s important to note if tool #1 creates good parts and tool #2 doesn’t.
In order to speed up the process, companies will machine a tool to an analysis model that’s automatically calculating for mold flow, inspect the part, and if it’s inaccurate, recut the tools and go through several iterations. With every recut costing $10,000 to $20,000, the expense can add up. “With 3D scanning, companies can cut the tool once, produce the part, scan it, then take that 3D scan data and use the virtual data to create a tool that will create an accurate part,” he says.
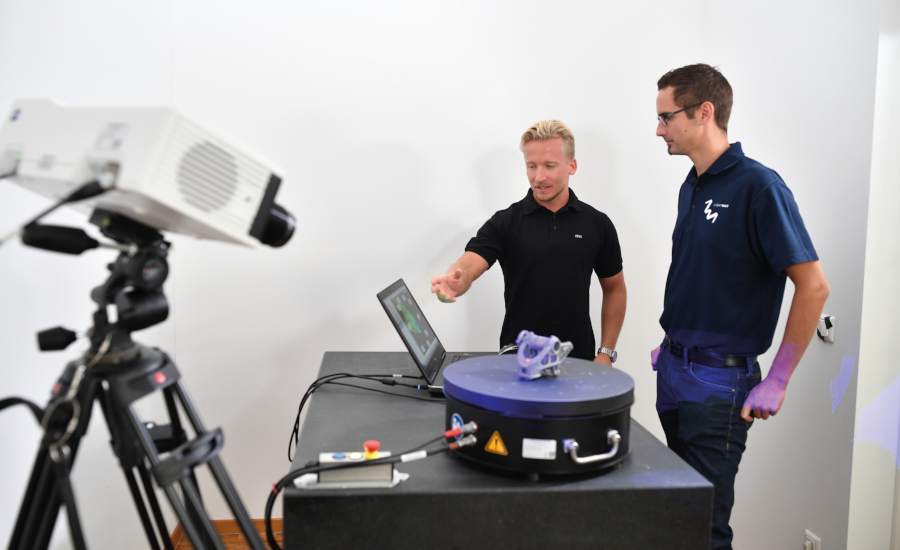
One of the biggest learning curves relates to software, Scribner says. “It’s a misnomer that when people 3D scan a part the scanner itself creates close to a watertight STL that can be used for reverse engineering. Basically you have to get a reverse engineering software to get the STL file.”
When customers see the information inside the scan software, they often think there are no additional steps. “A lot of times it’s not just about the hardware component of 3D scanning. Hardware is only half the story,” he says. “You really have to get the correct software, the right software for doing what you need to do.”
A range of applications are suited to 3D scanning, including any sort of reverse engineering application, root cause analysis, and trying to find a quicker solution to dimensional stack-up issues, Scribner notes. It can be used in industries such as medical, automotive, aerospace, packaging, and apparel.
But it’s not the best option in every situation. “Precision machining is not where it’s going to shine, due to accuracy requirements,” he notes.
Trends such as Industry 4.0 have also reached the 3D scanning market. Companies are looking to automate their processes, and 3D scanning is no different.
For the early adopters of this technology, they are looking for higher accuracy, precision and resolution, as well as automation. While arms necessarily require an operator at each one, other technologies do not.
With projected fringe or laser trackers, companies can automate scanning on the shop floor and make adjustments to the manufacturing process in real time or close to real time. These modifications are all part of the push to be more proactive.
If the technology sounds like something that would work for your application, be careful about selecting the right device. In the quality world, when companies are going to purchase a CMM, they look for repeatability studies, gage R&R, and assurance that the technology is able to repeat very accurately, Scribner says. They may not do this for 3D scanning, however.
“This could result in purchasing a system that is inaccurate and inadequate for their needs,” Scribner says, “so they think 3D scanning as a whole is not a good solution. It is, it’s just selecting the right one.”
His advice? Push for gage R&R and repeatability studies.
After almost a decade working in the 3D scanning, inspection and reverse engineering, Scribner says he’s seen dramatic improvements in accuracy and resolution as well as lower prices. In other words, the value for customers is better.