Thermal imaging can be used for quality control in many industries. It is a nondestructive inspection method, which is especially used to detect flaws that are not visible on the surface. These days the main industrial task for thermal imaging systems is to monitor the temperature of industrial facilities. Thanks to the development of powerful sensors this technique is gaining in significance for quality control.
One inspection method is the heat flow thermal imaging, which can make invisible flaws visible. Because each material has different heat conductivity, invisible flaws below the surface in component parts can be detected. The infrared thermal imaging is only one example of many. The result of the heat flow thermal imaging can be directly implemented in the rejection of a faulty product.
The heat flow thermal imaging is still a relatively new inspection method for quality control. Until now the military, medical applications or construction industries for the detection of heat loss in houses or plumbing were the usual application fields for thermal imaging.
Mode of operation
All bodies emit a spectrum of electromagnetic waves, depending on their temperature. As those are infrared rays, they are not visible for the human eye under normal temperature conditions. But a thermal imaging camera can make the infrared light visible. The newest technique has already progressed a good deal and there are several sensors on the market.
Controlled Heating with a Thermal Controller
A thermal controller makes it possible to realize not only passive but also the different active thermal imaging applications with almost any thermal imaging camera. This means impulse as well as lockin thermal imaging.
For the passive method the thermal controller can control reference objects. This means it compares the temperature of the reference object and determines if the process temperatures of the materials, which emerge from the process, have the expected temperature. If they don’t and the material has not the temperature of the reference object, then the software can issue an alarm or warning or the faulty product can be immediately rejected via communication with the machine. To achieve that a simple inspection program in the software and a communication protocol such as Profinet, Modbus, Ethercat, Ethernet, etc. are necessary to communicate with the machine.
For the impulse thermal imaging the controller takes over the control of the heat source. The thermal controller can have different control outputs to control either flash, infrared light, or halogen light and to initialize the image capture at a defined moment.
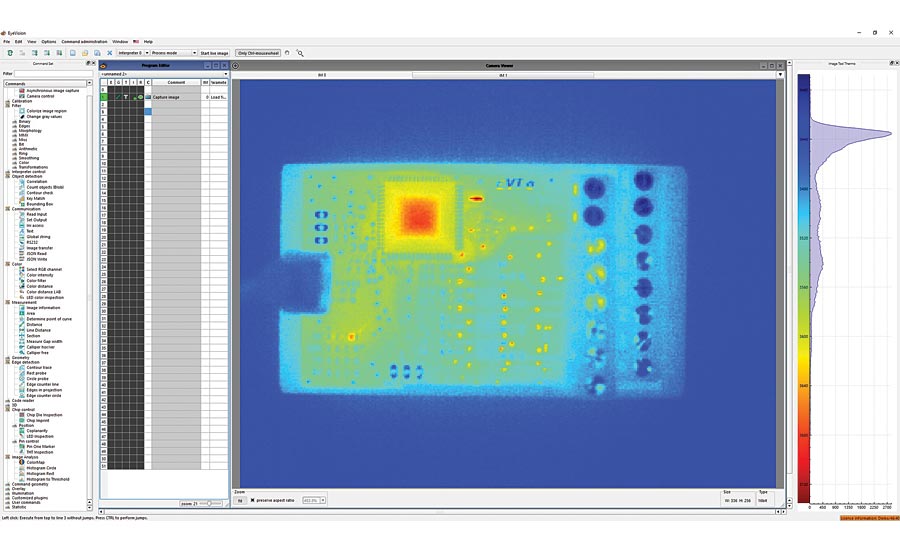
A PCB board captured with a thermal imaging camera (active thermal imaging).
For the real lockin thermal imaging are sinusoidal heat sources as well as rectangle heat sources available. As the thermal controller takes over the heat stimulation, it also controls the image capture process either via a protocol or via an integrated trigger input and output for the direct control of the camera. But only a few cameras have such control possibilities.
The timing plays an important role for a successful thermal image data acquisition, for lockin and also impulse thermography. With a thermal controller even a computer without real-time capabilities can fulfill operating system combinations such as Windows thermal imaging evaluations.
1. Active heat flow thermal imaging
In case of the active heat flow thermal imaging the surface of the object is heated with a heat source. This heating does not have to be very strong. A few tenth of degree Celsius are sufficient, for example with an infrared light or UV-light or ultrasound. After that the heat goes from the surface into the inside of the object. If an error with a different heat conductivity is under the surface, the heat dissipation is affected. This means that the surface stays longer warm. The thermal imaging camera can capture those hot areas and detects errors such as holes and voids.
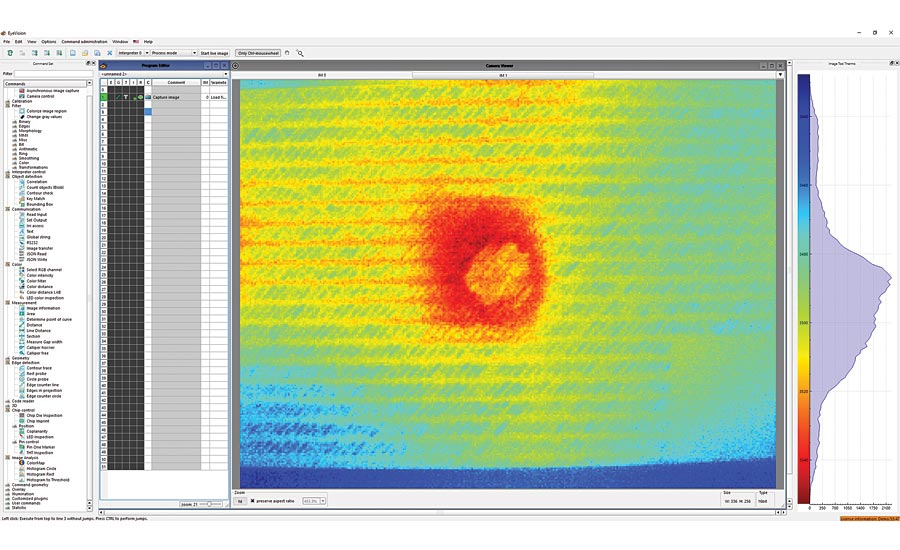
A thermal image of a defect in a fiber reinforced material.
Heat sources:
The following active thermal imaging methods are already established nondestructive inspection methods in image processing:
- Optical lockin thermal imaging
- Impulse thermal imaging
- Laser-stimulated thermal imaging
- Induction thermal imaging
- Ultrasound thermal imaging
1.1. Lockin thermal imaging and infrared microscopy
The Lockin thermal imaging is a method for increasing the measuring sensitivity in the active thermal imaging. This procedure is a method of the active heat flow thermal imaging. Therefore the heat flow is analyzed, whereby the time lapse of the measured temperature signals in relation to the heat source is determined and displayed.
The surface of the inspected object is heated with a halogen light. The Lockin thermal imaging requires continued heat stimulation.
This procedure can be combined with the microscopic analysis of the infrared microscopy to determine even the smallest structures with a resolution of a few micrometers.
1.2. Impulse thermal imaging
The impulse thermal imaging is similar to the lockin thermal imaging because it is also a procedure of the active heat flow thermal imaging. But the impulse thermal imaging only needs the heat source for a short time. The surface of the object is heated with flashes for only a millisecond for a few degrees (less than 5°C). In many cases the impulse thermal imaging leads to a fast, qualitative error detection. Especially for strongly homogeneous inspection object the impulse thermal imaging is a good choice.
Industrial application areas
The active heat flow thermal imaging can be used for different industrial applications, especially where a nondestructive inspection is necessary to detect structural error, such as e.g. adhesive weakness, cracks, delaminations, voids, air entrapment, corrosion as well as inspections for stability of weld seams, adhesive joints, solder connections. In addition an essential application is the coat thickness measuring on lacquer, film and inlays as well as the recognition of subtle material differences.
But also for the inspection of food the thermal imaging can be very helpful, e.g. when looking for foreign material, such as plastic and wood in coffee beans. The heat dissipation of the materials differ so that the foreign material of plastic and wood can be detected. The thermal image shows a clear difference.
Typical application areas for lockin thermal imaging
With the lockin thermal imaging fiber-reinforced plastic material and other fiber-reinforced composites can be inspected for delamination, impacts, enclosures, porosity, etc. Also leather can be inspected for wrinkles or mending, corrosion inspection, wall thickness measurement, inspection of adhesive joints, plastics weld seams, usw.

Different light sources can be used for the lock-in thermal imaging method.
Passive heat flow thermal imaging
In case of the passive heat flow thermal imaging there is no need for an external heat source as the object is heated during the production process. Usually the nondestructive inspection is carried out directly after the production, in rare cases the thermal control is happening during the production process.
The passive thermal imaging inspection gives results about different quality characteristics, even during the production process. For example, component parts and their joint patches gives the geometric temperature distribution on the surface information about the heat dissipation into the inside of the joint patch. Therefore inline production is possible. Because the passive thermal imaging promises results about the connection characteristics in ultimate vicinity of the jointing process.
Possible application areas
Passive thermal imaging can be used during ultrasonic welding. The ultrasonic welding is part of many branches of the plastics industry. During the welding process differences in the weld seam quality can occur even when machine and parameter settings did not change. Among the most common error sources are changing production conditions, formed part thresholds or storage influences. The process monitoring during ultrasonic welding is carried out by the threshold monitoring of the machine control. A reliable quality control is not always guaranteed with only the machine control, as it does not inform how the verberation and inserted energy is spreading in the component part.
The passive thermal imaging would help with the control of the heat dissipation.
Availability and user friendliness
The heat flow thermal imaging offers a new application spectrum for the material testing. The essential point is that with the use of thermal imaging for material testing a new base is resulting from the measured temperature relation.
The user friendliness of this technology depends on the availability of exact, fast and robust sensors. If one decides to use thermal imaging, it often depends on more than one not so easily definable parameter and therefore a detailed preliminary inspection should be made. The advantage is that errors below the surface can be reliably detected. Often large and fast moving objects are also not a problem. This thermal imaging also can be used for 100% on-line control. V&S