The perfect part. The Holy Grail of manufacturing today is to produce parts with absolutely no quality defects, zero scrap rate, and no time required for changeover to new product builds when required. This basic driving force behind manufacturing has now transformed into the Industry 4.0 concept of the ultimate flexible manufacturing line. A supply model where the end customer places an order, the factory immediately begins the manufacturing process to fulfill that request, the end product then ships directly to that customer and, of course, is delivered via a large drone launched out the top of an Amazon electric van.
Seemingly farfetched, does this notion bring to mind a science fiction movie where robots are building more robots? In truth, smart manufacturing technology is developing extremely rapidly. At FANUC’s robotics factory in Japan, robots are actually assembling their own motors in a lights out facility. Raw material arrives at the receiving bay, and finished, assembled and boxed product ship out the same bay. While the robots are not fully assembling themselves, the level of sophistication and intelligence in the process is truly a major achievement.
Advanced OEMs are creating similar semi-intelligent solutions powered by an array of sensors with the ability to harness the acquired data more effectively than ever. The aerospace industry is using robotic systems to measure mating contours to automatically calculate and create the necessary shims to ensure the seamless assembly of the two components. In automotive assembly lines, robots use a net-form and pierce process to precisely measure the gap between the door and the door frame to predict exactly how to attach the door hinge to create the best possible fit.
First Part – Perfect Part Concept
As a quality professional, it is fascinating to realize that one key component of this First Part-Perfect Part concept is to determine whether the part or final assembly is good or defective. How do you ensure a cell phone is the correct color red, or a welded door is the nominally designed overall shape, or a gear shaft will fit into the gearbox properly? The answer is an embedded or in-line quality and measurement system that is an integral part of every manufacturing process. This scenario might take the form of a physical dimensional inspection or the measurement of various key parameters in the process that ensure the end product is 100% correctly built to specifications.
This concept of inline quality control, which by definition occurs within the production process and ensures every part is inspected, is certainly not new to manufacturing. Industries such as medical implants and aerospace powertrain have organizations (FDA and FAA) that impose strict requirements of 100% inspection. Automotive body-in-white, vehicle powertrain, appliance, consumer electronics, and HVAC manufacturers have also utilized some type of inline gaging for decades to better control their processes and quality.
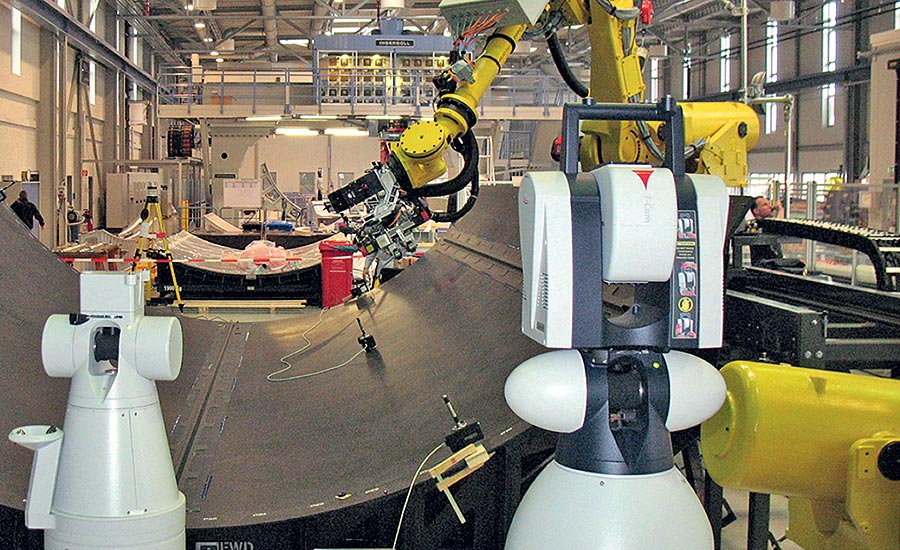
A Leica Absolute Tracker with FANUC robot in use for a stringer placement project.
Are We There Yet?
Do these examples of inline quality control offer proof that we are on the verge of supporting an Industry 4.0 fully flexible manufacturing line? Are manufacturers 100% satisfied with their inline quality control capability for their various processes today? The answer is no for both. Currently, the vast majority of manufacturing industries are constantly looking for better ways to ensure their quality
In aerospace powertrain, the “inline” inspection tasks are often executed long after the part has been manufactured. It is not unusual to hear from industry leaders that their quality Takt time is longer than their actual machining process! Every blade or blisk, for instance, must go through a full dimensional inspection, NDT process, and a visual inspection for surface defects. You might even refer to this course of action as “after line.” Although they are part of the procedure, quality is not “inline” with the production process. But what if the solution instead had multiple sensors and cameras located in the machining or grinding center that perform the above inspections in less than one minute just after the blade is completed?
In automotive body-in-white (BiW), as a second example, these inspections are often restricted to only critical characteristics and utilize a simpler and quicker process of comparative measurement or gaging. Instead, a small sensor could be used to measure the mounting location of the engine bracket or the cross-section depth and size of a weld spot and compare them to the previous inspection results. Gaging, as this comparative methodology is referred to, ensures the manufacturing process is not varying but requires additional quality measurements to confirm the product is consistent with its engineering specifications.
In another example, some BiW sub-assemblies must undergo additional dimensional measurement and visual inspection that is removed from the production line to ensure product compliance. What if the solution instead had sensors in the assembly line that could measure the exact, absolute location of the engine bracket in relationship to where the wheels would mount, and also pick up 100% of the weld spot sizes and locations to guarantee conformity? What if the whole operation could be accomplished in less than the Takt time of the full manufacturing process?
Obstacles and Breakthroughs
There are many obstacles to such concepts, but a variety of technology advancements are taking these ideas closer to fruition. These breakthroughs are often bundled into the Industry 4.0 conversation, but they all have real proof-in-action as evidenced in released and functioning manufacturing solutions.
1) Improvements in optical and digital camera technology which encompass hardware, software, and electronics continue to lead the way in measuring objects more quickly and more precisely. Higher megapixel cameras, improvements in CMOS technology, better and brighter light sources, and new signal processing algorithms are all factors in creating improved sensors. These improvements not only affect the simpler 2D systems, but also the 3D projected light solutions such as structured light and laser line scanning. New sensors in this area of metrology allow for measurement of black, extremely reflective and even translucent surfaces heretofore not seen in dimensional metrology.
2) Significant computational advancements enable standard engineering computers to handle very large data sets, which further expands the boundaries of inline metrology. This progress is not limited to GPU improvements in manipulating large CAD models or visualizing large dimensional inspection point cloud data sets. These enhancements include quick simulation of collision-free robotic paths, moving a very large amount of data from the sensor to the computer, calculating detailed surface mesh information from huge point cloud data sets, and calculating surface boundary information from several merged images. In the past, these operations took many hours of computational time to properly simulate processes or simply process tens of millions of data points. Now the process time is compressed into minutes or even seconds.
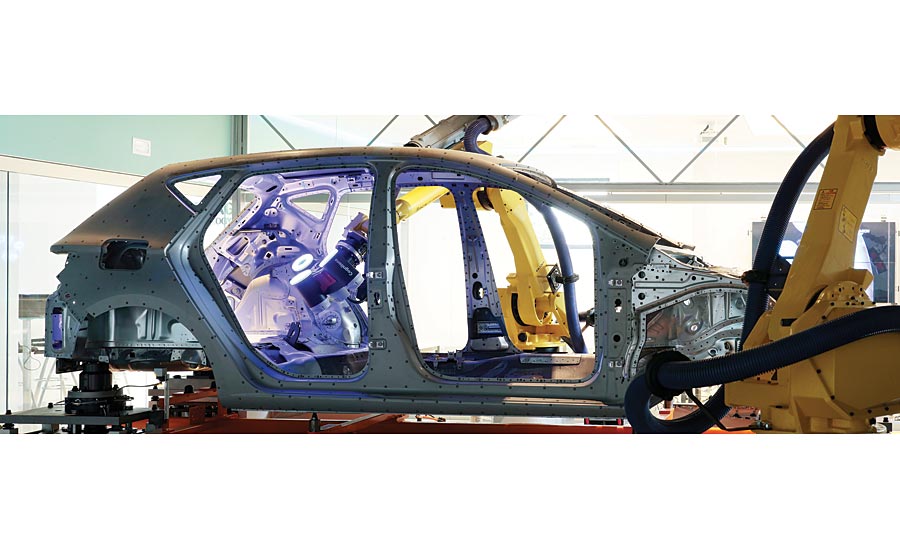
Hexagon’s WLS (white light scanner) system is a 3D optical measurement solution for measuring an body side or door.
3) Artificial intelligence is starting to make an impact. This is not a reference to Alexa or Siri interpreting our everyday commands, but to the subset of machine and deep learning in manufacturing. Both terms are intimidating at first, and the differences can be difficult to digest. Machine learning is being used to process incoming sensor data from the manufacturing process combined with the result dimensional data to enable companies to predict, and therefore prevent, what situations create non-conforming parts. Deep learning is being used to process thousands of surface defect pictures taken by cameras to automatically determine via digital analysis what parts have defects. This process is in its infancy, but is being used and tested in many different applications with quite good initial results.
From cell phones to airplanes, manufacturers are moving toward the ultimate goal of full inline quality control including dimensional inspection. Will this lead to a red four-wheel, four-door SUV built for Joe, followed by a yellow, two-door EV convertible for Sue, all moving down the same assembly line and delivered to your door in two weeks? Time will tell, but it is important to emphasize how much closer we are to these concepts in this digitally transformative age.