The renewed interest for vision guided robotics (VGR) for the manufacturing of parts and packaging of goods is much in part to the number of advances in sophisticated technologies over the last decade. Improvements in size, speed, precision, flexibility and price for a variety of devices have created a technological awareness that is rebuilding confidence for the use of high-quality vision technology in robotic automation.
Well-suited to meet unique application requirements, robots are now able to perform tasks without operator intervention and reprogramming. And, advancements in precision for machine vision have created next-generation imaging systems more capable of finding an object and subsequently providing an accurate and acceptable location to the robot, providing the functionality needed to efficiently and economically fulfill demands for diverse markets.
The Importance of Vision Guided Robotics
Vision guided robotics today encompasses all the technologies needed to recognize, process and handle objects based upon visual data, including lighting, cameras and the necessary software to provide reference points for the robot. These reference points are either X, Y coordinates for two-dimensional (2D) vision, or X-Y-Z coordinates for three-dimensional (3D) vision, which are then used by the robot to accurately pick, handle and orient an object.
Robots, especially for assembly and welding, have consistently excelled at repeating predefined tasks against rigid well-defined objects that are always in the same location. However, once those objects vary in shape, or are not always in the exact same location, robots fail. For this reason, VGR is required to mitigate the problem. If the robot does not “know” where the object is, it needs to be able to “see” it to find it. In essence, without some type of assistance, the robot is “blind.”
Moreover, VGR is a continuum, and the right solution depends on the specific application. Two-dimensional systems, except for a few caveats, can recognize the location of an object and provide the X, Y coordinates for picking. Three-dimensional vision is required for more random situations, where items are located haphazardly, or stacked in a bin with varying orientation.
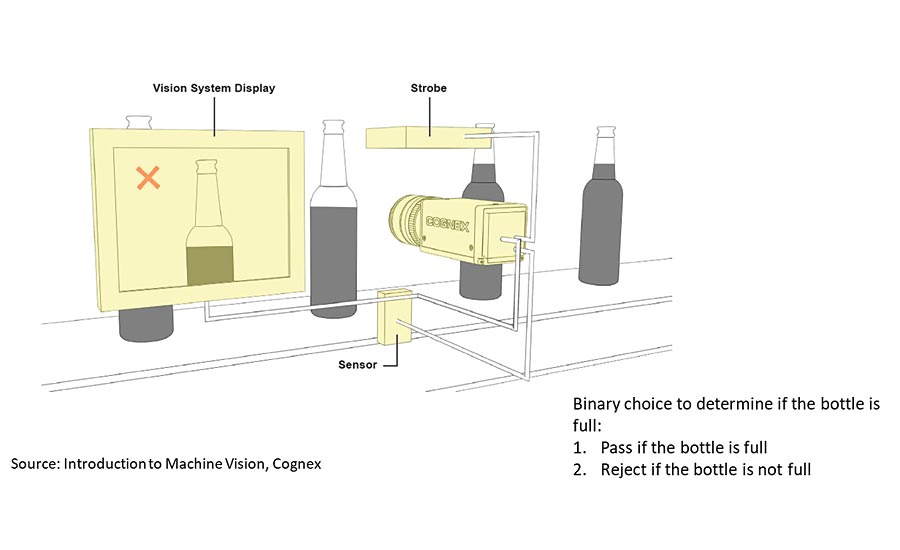
Bridging the Gap with 2D Machine Vision
Many early vision systems were purpose-built and offered little room for flexibility. The cameras and sensors used were slow to perform, sensitive to extraneous light and costly to implement. Likewise, the tools to work with these systems were virtually nonexistent. All of this resulted in systems that were expensive and unreliable, leaving manufactures discouraged and doubtful. This created a need and opened the door for 2D machine vision.
Two-dimensional machine vision uses grayscale or color imaging to create a two-dimensional map to show anomalies or variation in part contrast. Moreover, for 2D vision technology to work, objects must be on a flat surface, and be of a consistent size and shape.
Occurring in a single plane (X, Y), where part depth data is not required, 2D solutions tried to bridge the gap between a rigid part always located in the same position, and that same part that could possibly be varied in its actual location. Similar to a guide dog assisting a visually impaired person, 2D cameras helped to notify the robot of the proper part location.
Over time, improvements in speed for the acquisition of images and recognition of parts facilitated vision systems to process moving objects (i.e., parts on a conveyor). Because of these improved capabilities, a variety of applications are now possible. Tasks such as inspection, barcode reading, surface marking detection and basic positional verification can occur, making 2D machine vision the most commonly used VGR method used today.
Inspection through vision determines the quality of parts by examining the parts against some set criteria. These systems are better suited than humans because of the repetitive nature of the task, and it can be done faster and more objectively. Unfortunately, inspection systems are sometimes thought of as a cost of doing business, since their objective is to discard parts that do not pass.
Guidance systems on the other hand compensate for randomness, improving throughput and accuracy. This is always viewed as a key benefit to the organization.
While these innovations in vision technology greatly optimized functionality, quality, reliability and usability of vision systems, their two-dimensional nature was still very limiting for certain applications, especially for picking and placing. After all, how can a part truly be detected, if the entire part cannot be “seen”?
The Introduction of Integrated Lighting
While some manufacturers have found success with robotic arms equipped with two cameras for picking and placing, these systems can be challenging to program and set up. Three-dimensional vision technologies today have the capability to overcome these obstacles and more. Advances in 3D technology have worked their way into improving three-dimensional vision, which some call the “holy grail” of VGR. This is especially true for random bin picking.
When objects are presented randomly in a bin, particularly when they are stacked upon each other, an automation solution is now able to sense randomly placed parts and determine how to handle them using structured, integrated lighting and 3D CAD matching. Continual improvements in camera technology and processing software have made this a reality, equipping a robotic system with the complete ability to find, recognize and pick an object—all without user programming.
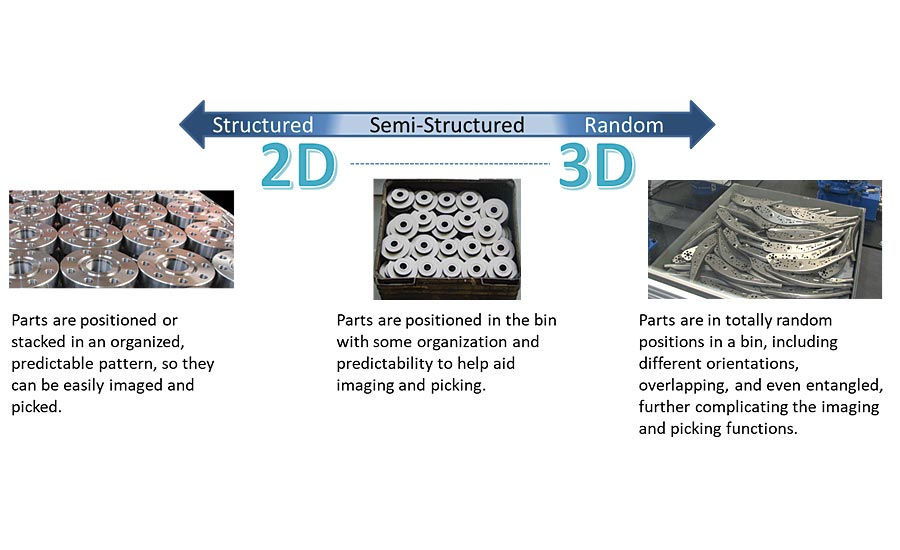
The Current State of Machine Vision Technology
Technology continues to improve on all fronts. Current trends reveal a giant increase in the diversity of applications, especially for inspection and guidance for material handling. While inspection systems are sometimes perceived as “adding to cost”—because they discard bad parts while improving quality—the increased throughput that comes from guidance can directly impact the bottom line.
Complete vision systems are also becoming more integrated and prepackaged by vendors, relieving companies from having to assemble an erector set completely on their own. Vision systems have no trouble combining 2D data with a 3D point cloud and image of the object, so that the part location and orientation can be understood in just seconds.
As software progresses to match the speed and diversity of camera hardware, vision systems continue to be easier to install, use and maintain. Likewise, increased performance and greater flexibility enable robots to perform tasks with better precision and speed, while artificial intelligence allows vision systems to learn and adapt based upon previous “experiences.”
Today, 2D and 3D vision-guided systems are effectively bridging the gap for many applications in diverse industries, and the chances are very high that if an application challenge is present some type of robotic vision capability is now available to help. And remember, if a solution is not currently available for a given application, the technology will continue to evolve and improve, introducing a “new world” of high-quality, value-adding robotic solutions in the future.