Thickness measurement is the gauging of coatings or films on surfaces—such as paint on metal parts. Manufacturers are increasingly using thinner and higher-performance coatings these days, with tighter applied thickness tolerances and an increasing need for more accurate and precise tools.
As demands on production processes become increasingly rigorous, manufacturers are faced with the need to optimize raw materials and adhere to numerous compliance standards all while measuring with precision.
Although thickness measurement requirements have not changed, per se, the level of desired precision has become more exact and the materials that are measured have become more complex, says Peter Joshua, CEO of Solarius Development.
This requires manufacturers to invest in coating thickness measurement technologies that are highly accurate, repeatable and reproducible, says Vivek Komaragiri, CTO, Sensory Analytics.
Fortunately, measurement technologies that were initially only used for off-line thickness measurements have evolved to measure coating thickness applications in real-time during production, Komaragiri says.
“The ability to measure coatings in real-time during production has addressed much larger needs as plants can now capture defects before [and] as the product is being made,” he says.
“During the manufacturing process, some coatings are applied wet and then cured in an oven which could take anywhere from one to 15 minutes to dry,” he adds.
Now, certain systems can measure wet coating thickness, helping manufacturers address coating defects and improve quality at the point of application.
“This saves manufacturers significant money per-year by minimizing coating over application and reducing the amount of scrap material produced, while creating a permanent quality record of each web, coil or component measured,” Komaragiri says.
As thickness measurements transition from analog to digital records, manual logging of measurement values are increasingly replaced by digital thickness gages, which offer extended data logger capabilities, says Krystian Rostkowski, application manager at Sonotec GmbH.
These gages “can save the point into memory by [a] single press of a button and export [the information] in very easy way for reporting or for further processing,” Rostkowski says.
While automated gages help to more quickly and reliably collect measurements, there is a downside: those collecting the measurements aren’t passing along as much institutional knowledge.
“The level of ultrasonic knowledge between operators is not necessarily increasing,” Rostkowski says.
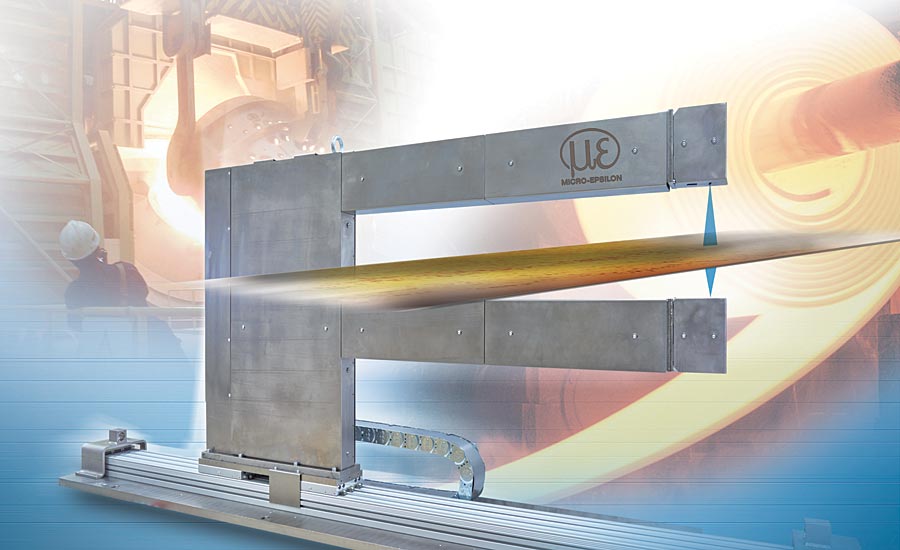
The level of desired precision has become more exact and the materials that are measured have become more complex. Source: Micro Epsilon
Contact and non-contact thickness measurement
A distinction must be made between contact and non-contact thickness measurement, says Martin Dumberger, managing director, Micro-Epsilon America.
Certain equipment can indirectly determine thickness via the use of isotopes or X-ray radiation—the non-contact approach—or, many applications are solved by measuring thickness geometrically using displacement sensors, Dumberger says.
“Due to a sum of advantages, the second approach is becoming more and more important,” he says. “Optical metrology in particular has brought some significant innovations.”
They include sensors with improved performance, which use algorithms for signal processing and also utilize procedures for compensating disturbing effects of temperature gradients or harsh environments.
Komaragiri says that coating-and-film weight tools are rapidly being replaced by more precise, optical thickness measurements in multiple manufacturing sectors.
“These advanced technology methods facilitate more accurate real-time measurements to be made either on-line or off-line in varied industrial markets that have never had the opportunity before,” he says.
Optical metrology tools that are based on laser triangulation have advantages, Dumberger says.
“They measure without contact and therefore without wear,” he explains. “Moreover, independently of the condition of the material, it is possible to carry out an exact geometrical measurement in relation to the strip surface.”
In essence, he says, optical metrology can accommodate more measurement values over a larger area, which when averaged give greater precision.

As thickness measurements transition from analog to digital records, manual logging of measurement values are increasingly replaced by digital thickness gages, which offer extended data logger capabilities. Source: Sonotec
Challenges with variation
Speaking of harsh environments, variations in manufacturing environments and digital infrastructure can present challenges, experts say.
Although measuring instruments are designed to be stable and highly accurate control units in the manufacturing process, deviations from specified dimensions can occur in both hot- and cold-rolling processes. If the thickness levels change too much, quality can falter, which could cause major issues down the line.
As the demand for in-line thickness measurement grows, metrologists must often grapple with measuring in-line within manufacturing environments that lack the stability for sub-micron
metrology measurements.
“The big challenges are in the environment of the supported customer processes,” says Dumberger. “Mostly the material is hot, in steel applications up to 1200°C. Then there is steam, emulsion and things like that. All this is very unfriendly for an optical gage.”
Measuring a broad range of coating types, measuring in-process with quickly moving products, and temperature and humidity variations can all present difficulties. In addition, not every manufacturer’s IT setup is the same.
“The challenge is to integrate [digital gages] to every customer’s IT infrastructure,” Rostkowski says. “The standards how to do so are not defined and in many cases an individual approach is needed to fulfill customer needs.”
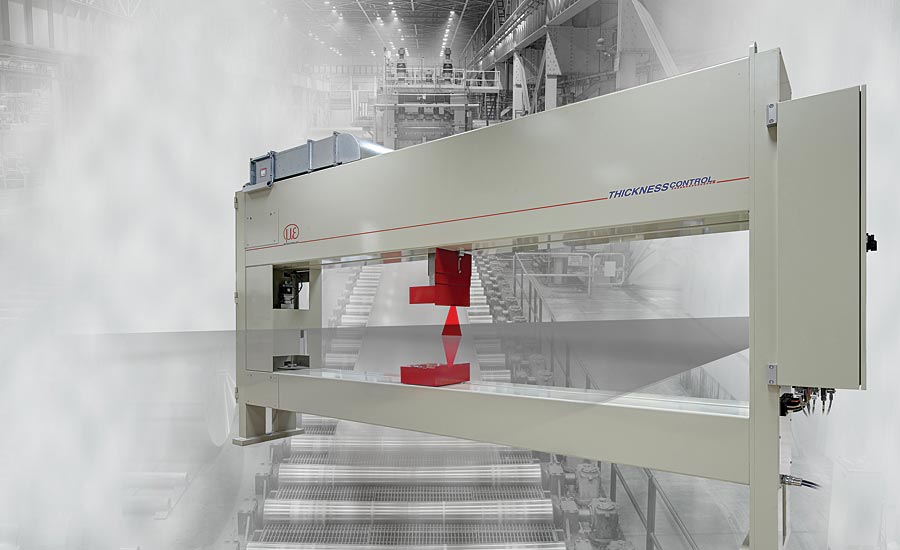
Manufacturers should invest in coating thickness measurement technologies that are highly accurate, repeatable and reproducible. Source: Micro Epsilon
Trends in the field
The measurement of complex structures is becoming more commonplace, as is an appreciation for sustainable approaches, experts say.
With greener testing options available, many businesses are seeing the value in shifting towards these alternative thickness measurement technologies, says Komaragiri.
“The trend in most markets seems to be having an environmentally friendly thickness measurement solution,” Komaragiri says. “Nuclear gaging for measuring coating thickness/weight and the destructive test methods generally relied upon in major industries, like film packaging, [can] add waste and administrative burdens.”
In addition to the move toward Industry 4.0, Rostkowski is seeing manufacturers integrate robots and drones to overcome rope access or scaffolding limitations. They’re also mounting stationary sensors under insulation to monitor assets without having to remove insulation, he says.
And because of the increased demand for measuring complex structures and of exotic materials, confocal and interferometric measuring sensors—typical lab technologies—are migrating onto the factory floor, Joshua says. Q