Tensile testing is one type of physical testing that is performed on a test specimen to measure mechanical attributes, primarily to indicate whether it is fit for purpose. The specimen may be either a finished product (component or assembly) or a sample of raw material used to make a finished product. The tensile test places the specimen under controlled tension by pulling it apart or stretching it to a certain load, elongation, or a relevant event—often its destruction.
Applying tensile loads indicates much about performance in service when a product will be put under stress in use. Therefore, tensile testing is carried out to measure such functionalities as the operational effort on medical devices, the break resistance of welded connectors and fastenings, the strength of adhesive joints and seals, and the opening force of packaging flip-caps and pull-out stoppers.
Testing objects under compression, bending, torsion or dynamic loading are methods which are also relevant to checking product quality, but the tensile test is particularly valuable in almost all manufacturing industries—and is fundamental in raw materials benchmarking.
More demanding sustainability objectives and resource challenges are driving new materials usage. Manufacturing still requires the material to have appropriate ductility, toughness or other properties to match the replaced material and to be accurately profiled to inform production processing modifications. In order to compare and quantify the performance of a material, a very specific tensile test procedure is carried out to:
- prepare the specimen,
- apply the tensile force,
- measure the data and
- report the calculated properties.
Test samples of the material are produced in a dumbbell (or ‘dogbone’) shape of known geometry, to enable the salient properties to be accurately calculated from applied tensile force and measured elongation. For example, the familiar terms, stress and strain are used to calculate the fundamental materials property of elasticity, Young’s Modulus.
Stress (σ) = Force (F) / Cross-sectional Area (A)
Strain (ε) = Elongation (ΔL) / Original Length (L)
Young’s Modulus of Elasticity (E) = σ / ε
Other properties pertaining to ductility, toughness, brittleness and ultimate tensile strength are also able to be calculated from these measurements.
Universal Application
Although the two groups of test specimens—finished products and raw materials—are handled in different ways in their lifecycle, there are universal practices applicable to performing an accurate tensile test on either. In fact, the equipment used is often termed a universal testing machine (UTM), being capable of a variety of test types that the organization may need to perform. The components required to perform a test procedure are:
- fixturing to hold the test specimen,
- a test frame and loadcell capable of applying the desired load,
- instrumentation to capture the data, and
- a means to calculate results and display the output.
Simple, manually operated test stands are available through to highly automated test systems, enabling testing for quick production checks, legislation necessity or innovation in product development. Portable, handheld gages are also used where circumstances dictate. Whatever the implementation, optimizing the quality of results is vital to reap the benefits of investment. Beyond choosing a suitable test frame and loadcell to handle the expected loads with acceptable accuracy, it’s the selection of appropriate accessories that goes a long way to ensuring this.
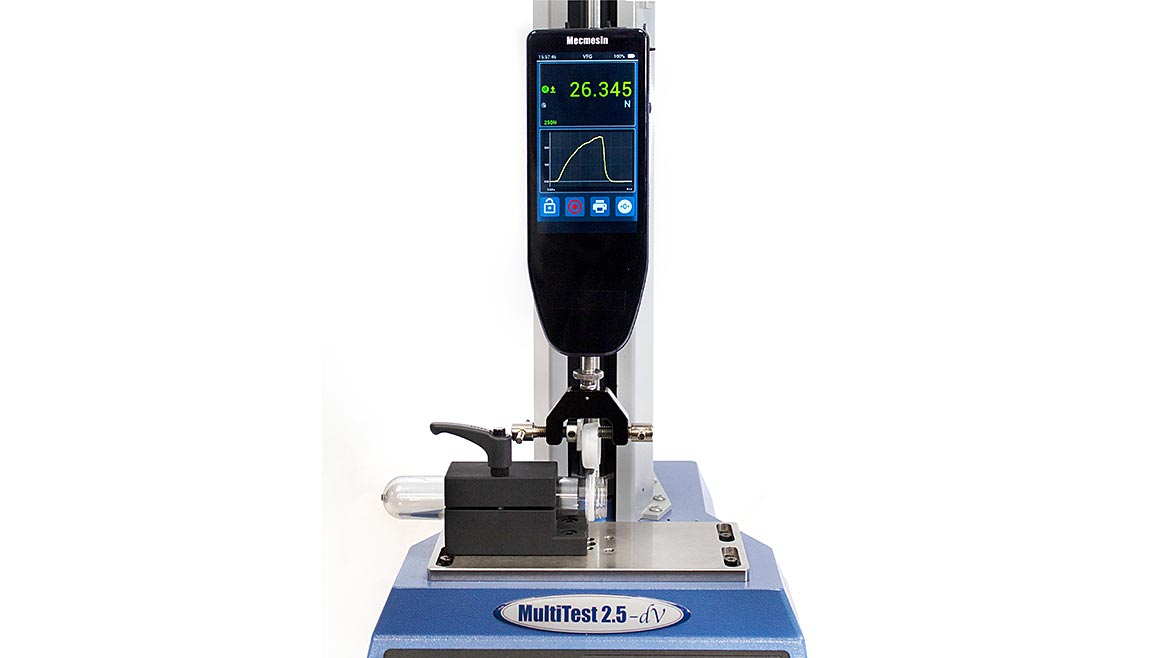
A simple handheld gage connected to a test frame measuring the break resistance of a plastic tethered closure design of bottle cap. An upper standard vice grips the cap and a custom 3D printed lower fixture ensures exact fit and alignment to the preform, to optimize accuracy. | Image Source: Mecmesin, a PPT Group company
Specific Accessorization: Grips, Fixtures And Instrumentation
The quality of results is heavily dependent on the correct setup of the apparatus to minimize errors. In a tensile test, the application of the load along the appropriate axis and elimination of sample slippage or damage is of primary importance. The grips used to hold the test piece should ensure these conditions are met.
As with any quality assurance function, consideration of international testing standards is a prerequisite and in many cases, the type of grip is specified, emphasizing the importance of this component of the testing equipment in achieving valid results.
Under tension, the specimen is more likely to pull out, so eliminating slippage with ‘self-tightening’ wedges, levers, eccentric cams/rollers and pincer-scissors in the upper grip (attached to the loadcell) is best practice. Other standard ‘off-the-shelf’ types of grip; vice, pinch, toggle, claw and chuck varieties may still do a perfectly good job, and interchangeable jaw faces, from soft rubber to serrated and diamond-coated steel add versatility to the setup.
The lower fixturing may use the same grip if the specimen geometry allows (raw material dumbbells), otherwise an alternative standard grip or a specialized and more complex multi-part fixture may be needed. Some industries utilize dedicated, adjustable clamping jigs to hold down the test product—grasping a low-friction or shaped plastic container without deformation whilst the cap is pulled off, for example.
Some specimens may warrant a completely custom-designed gripping system, either due to proprietary geometries or for efficient test piece interchangeability. Advances in 3D printing have enabled equipment manufacturers to offer that service, bringing costs down and enabling smaller companies to perform their own in-house testing.
Some fixtures may even require machine compression to apply tension correctly to the test piece—the flexibility of a UTM.
Measured data is most often presented on a display and obtained from sensors within the device itself, such as a strain gage in the loadcell for force and an encoder on the moving crosshead for distance. In situations where the result of interest is only the force needed to cause an event (yield, break), by pulling at a certain speed (distance/time), this configuration may be 100% suitable. In the specialist application of materials tensile testing, this displacement data may not be good enough. The simple reason is that the displacement of the crosshead may not represent the actual elongation of the test sample, rendering the calculations incorrect.
The accessory that deals with this issue is the extensometer. This instrument, in ‘contact’ type variety, lightly clamps the dumbbell at each end of its gage length and as the material stretches, the arms move apart, sending the correct displacement data to the calculation.
One golden rule of metrology is that the equipment used to measure the result should not interfere with the result. In many situations, this is unavoidable, but the effects are negligible compared to the measured values. Video extensometers are the next-level solution here, being noncontact, they record accurate elongation data without touching the test specimen itself.
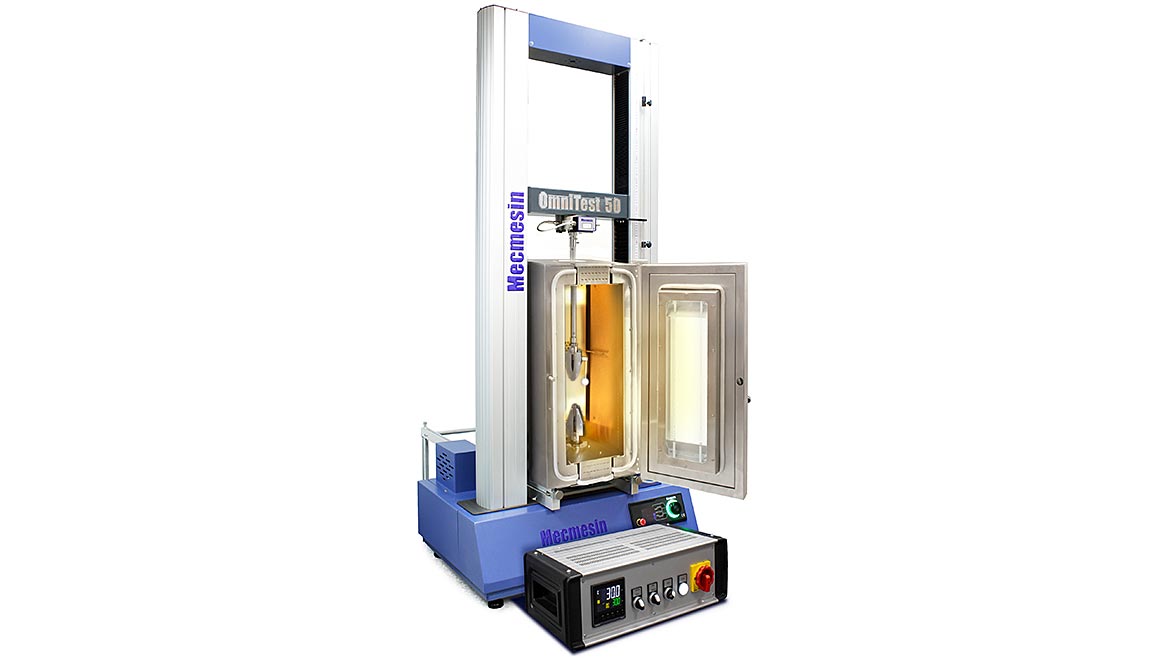
Environmental chamber enables the testing to be performed under controlled temperature conditions in scenarios where the test standards stipulate. | Image Source: Mecmesin, a PPT Group company
The final upgrade element to the complete materials testing system is the ability to test in the representative real-world temperature environment, should the final product application or obligatory test standards dictate. An environmental chamber (or thermal cabinet) provides enclosed ambient conditions for the test space, which may be at elevated or sub-zero values. Temperature-resistant grips must be used.
Software To Enhance The Hardware
Once the hardware has been selected and the desired levels of accuracy, precision, resolution and repeatability for a single machine have been achieved, consideration may be given to enterprise-wide data sharing. Cloud-enabled software can now enable seamless sharing of test programs, optimizing repeatability across sites, as well as sharing results with customers. Furthermore, implementations in highly regulated industries can support audit trails and e-signature security functionality.
The End Result
The theory, objectives and benefits of tensile testing processes remain constant and with a good understanding of your organization’s relevant quality assurance requirements—and selection of the most appropriate equipment—the tension of dealing with evolving external factors can be relieved.