We probably all remember the one or other advertising poster that we have been passing by for some weeks. For example, the one at the travel agency with the golden-tanned couple walking the white sand beaches, the azure blue sea and waving palm trees, with pillowy-white clouds floating in an aquamarine sky. After several weeks though, that idyllic poster is no longer nice, because some colors obviously are heavily faded or changed.
The effects of weather - sunlight, temperature, and moisture - can make printing inks change appearance caused by pigment and paper degradation. The same can happen to polymers used in outdoor or indoor applications. Product aging caused by weather stress sometimes appears faster than expected – a very unpleasant experience. A typical reason for premature product failure can be wrongly selected or insufficiently levelled UV-stabilizers. An impressive example of premature failure had been the red seats of the Raymond James Stadium, home of the Tampa Bay Buccaneers football team, which degraded much too fast due to missing UV inhibitors. “The original red seats, designed to match the Buccaneers' uniforms, had faded to “an unsightly pink over six years 1998-2004, and the paint on the stanchions has bubbled and peeled.”
Other property changes of polymer products caused by the effects of weathering can be yellowing, especially of transparent or white polymers, loss of physical strength, and gloss loss caused by micro cracks in the surface.
Accelerated Weathering
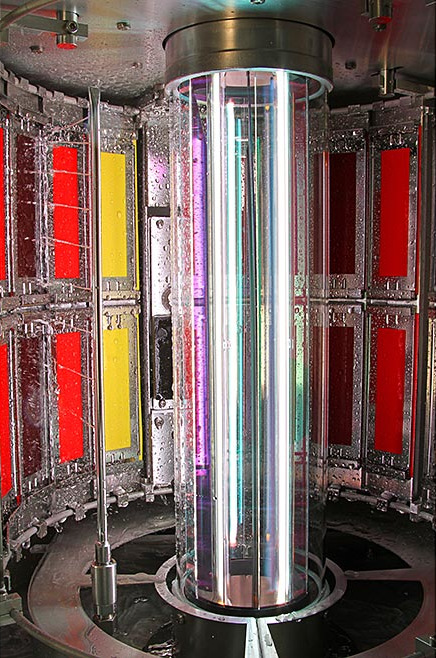
Accelerated weathering instruments have existed for about 100 years. They are designed to reproduce the stress and damages caused by sunlight, heat, and water (rain/dew). Because the weather stresses are applied on a constantly high and intensive way and the night times are avoided, weathering devices typically reproduce within weeks the damage that occurs over months or years outdoors. Thus, accelerated weathering testing helps new product development teams to determining the best suitable polymer type and its best suitable UV-stabilizer package for new products to avoid premature failure in the field.
The two major types of weathering devices are the ones that use full-spectrum xenon-arc lighting technology (UV, VISIBLE, and IR) – all radiation parts closely matching natural sunlight; and the ones that apply majorly short wavelength UV radiation from fluorescent-UV bulbs (UVA-340). Whether the one or the other type is better suitable for a specific product basically depends on the application and the monitored failure type.
The major question in accelerated weathering testing is: do my accelerated weathering test results correlate sufficiently to those from real time natural exposures? Real time natural exposures are performed under standardized conditions - most commonly in Miami. Why Miami? Because Miami is the internationally recognized benchmark location for outdoor weathering testing. Miami provides subtropical weather stress, which is rich on UV radiation throughout the entire year, relatively hot, and humid. Furthermore, dew formation almost every night brings the mechanical and chemical stress. Therefore, 12 months of Florida weathering can equate to several months more or even years elsewhere with less stressful climates. Benchmark testing is important to be started parallel with the laboratory accelerated testing, typically for periods of one to three years.
Test Methods
Finally, we need suitable weathering test methods. For plastics, the most common methods are the international fluorescent-UV weathering standard ISO 4892-3 and the xenon weathering standard ISO 4892-2. Both are very useful, as they provide options for both outdoor and indoor testing applications. While the fluorescent-UV devices make use of different bulb types - for outdoor testing (UVA-340), and for indoor (UVA-351), the xenon devices use optical filters. For the xenon weathering test method “A” (outdoor conditions), you install the Daylight filter, and for the indoor lightfastness test method “B” the Window Glass filter. With those options, a xenon weathering device realistically simulates outdoor or indoor exposures. Inside the test chamber water is applied as water sprays for 18 minutes every two hours. This part provides the cyclic mechanical stress due to swelling when wet and contraction when drying up. Additionally, the water chemistry such as hydrolysis reactions or photocatalysis. The irradiance at 60 W/m2(at 300 - 400 nm), the air temperature at 38°C, and controlled black surface temperature at 65°C are all close to natural maxima. Everything is set to support faster degradation than natural. That is where the name accelerated weathering comes from. The test duration depends on the product and its expected service lifetime. The questions here are – how much faster is the accelerated weathering test reproducing the same product changes compared to the Miami benchmark and how well does the test correlate?
Correlation to Natural Benchmark and AF
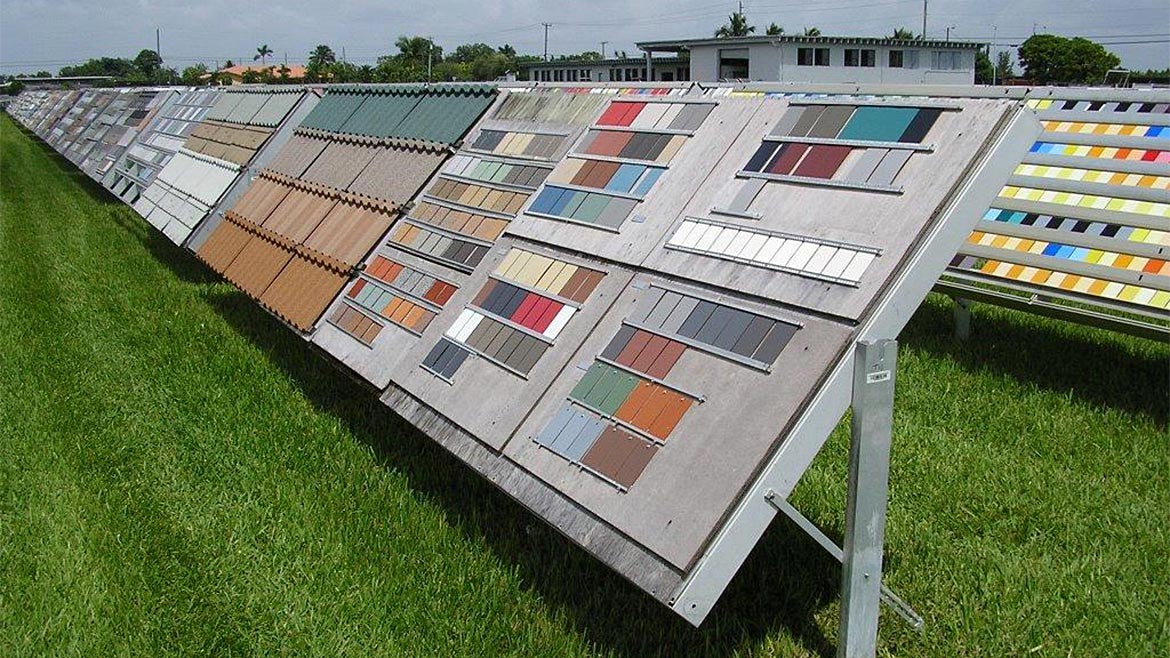
The correlation of accelerated and natural benchmark weathering is pure statistics. For some cases, it is sufficient to simply look at the ranking correlation. The related statistical method for the ranking correlation of test results is the Spearman rank correlation coefficient. A reliable and simple method of checking both the strength and direction (positive or negative) of any correlation between two variables - our laboratory test compared to the natural. The coefficient value can lie between –1 and +1. The closer to +1, the better.
Probably more commonly used is the Pearson correlation coefficient. Same as for Spearman, the closer the Pearson value towards +1, the better the correlation. Determined Pearson correlation values >0.7 can be regarded as an indication for sufficient correlation and sort of proof for a well-functioning accelerated weathering test. Pearson correlation coefficients <0.7 however indicate, that further fine-tuning of the accelerated test parameters (e.g., temperature, wet dry phase duration) is required.< p>
The acceleration factor “AF” for my accelerated weathering test is another simple calculation. Just as an example: we may find that our product reaches our color change fail-criteria at the Florida benchmark after 208 days (approximately 5000 hours) and my xenon device reproduces the same level of change after 17 days (approximately 415 hours), then AF would be 12 for the color change. We then know, that one month accelerated weathering equals about one year Florida for the color change of our specific product type. Please remember, acceleration factors are material dependent. Furthermore, dependent on the evaluated change criteria. For example, color change could have a different AF than the one for tensile strength.
State-of-the-art accelerated weathering tests, notably xenon-arc and fluorescent-UV methods, are invaluable assets in both new product research and quality assurance. While xenon-arc technology might have some limitations for extremely short test durations, it still stands out as the superior laboratory technique due to its comprehensive coverage of all polymer-based products and their various failure modes. Finally, when acceleration factors AF are determined, these tests also enable reliable predictions of product service life. This is important, especially in meeting or exceeding customer expectations, particularly when establishing robust brands or providing product warranties.
0.7>