
For an effective connection without product damage, choose a test connector with pressure-assisted gripping and sealing. This design eliminates the need for sealants or wrench tightening, which can cause thread damage or distortion to the tested part. Source: FasTest Inc.
Leak testing is essential for virtually any product that contains or keeps out a liquid or gas. The sophisticated leak testing equipment available today-capable of data acquisition and communication with a controller- can provide highly accurate results by automating the testing process, eliminating the risk of human error. However, this automation comes at a high price, requiring costly equipment, time-intensive calibration and maintenance.
For many applications, especially research and development, water immersion testing provides a simpler, less expensive yet effective alternative. Water immersion testing, also referred to as water dunk testing, can deliver accurate results by allowing a properly trained operator to visually determine if a part is good.
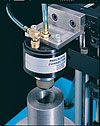
To effectively seal a part for testing, select a fixture that seals without applying compressive force. This method provides the highest accuracy by using seals that are either expanded into or over the part’s opening, better mimicking the actual conditions of part use. Source: FasTest Inc.
Test Connectors
To ensure water immersion testing is performed accurately, the part must be effectively sealed using a reliable and easily repeatable method. A poorly sealed part will create a stream of bubbles that may be mistaken as a leak. For this task, select test connectors that are:- Suitable for immersion testing.
- Resistant to contamination and corrosion.
- Made of stainless steel and/or anodized aluminum.
- Designed to have few moving parts-reducing the effects of contamination.
- Ergonomically designed, which makes them easy to use and install.
- Easily maintained, to ensure long-lasting operation.
- Manufactured with features such as pressure assisted gripping and sealing, which ensure a safe, consistent and reliable seal.
Fixture Method
Another important aspect of sealing the part is selecting the appropriate fixture method. For example, if a clamping fixture is used to hold a part, such as a reservoir bottle for windshield washer fluid, using the force of the clamp to create the seal could damage the part-or perhaps mask a leak by pushing the two halves of the part’s components closer together.For this reason, it is important to select a fixture method that does not use external clamping force to seal the part. Select a fixture that uses seals that are either expanded into or over the part’s opening. Sealing by this method will not exert a clamping force to the part and thus better mimics the actual conditions of part use. This fixture method will provide the highest accuracy results.
When sealing parts with threaded ports, such as a casting, if a fixture is used to clamp and seal the casting, a clamp may be needed to exert a high force to create an effective seal. This high force has the potential to mask hairline cracks that may be present in the casting-thereby masking a possible leak.
Another method is to use a threaded fitting of the same thread, such as an NPT fitting, apply thread sealant to the fitting and use a wrench to tighten the fitting into the port. However, when wrench tightening a fitting into a port, the port can become distorted from the torque and thread sealant.
Instead, select a threaded test connector that grips and seals the port, with no thread sealants and no wrench tightening required. Connectors such as these are easily attached to the thread and use pressure-assisted sealing and pressure-assisted gripping to provide a safe, reliable seal. Sealing threaded ports in this manner will provide the best test results with no damage or distortion to the ports.
Water immersion testing does have some downsides. It is a messy test method, because water splashed during the testing process may cause the surrounding equipment and floor to become slippery, and get the operators wet. Also, after testing, parts may need to be dried to eliminate corrosion-and some parts are not suitable for immersion testing all together.
If the water is not properly maintained, murky water along with poor lighting conditions makes it difficult to see a leak. And lastly, the method relies on human observations to identify a leak-which may be more inconsistent than automated alternatives. However, for many industrial applications and for research and development, it often provides the test results required at a fraction of the cost.
Mark Spindler is product manager for FasTest Inc. (Roseville, MN). For more information, call (651) 645-6266, e-mail [email protected] or visit www.fastestinc.com.