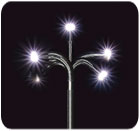
The articulating tip of a videoscope contains the micro-camera, LEDs and “bending section.” Source: RF System Lab
For any technician who monitors, maintains or repairs complex machinery or equipment, nothing aids the diagnostic process more than being able to see the physical condition of critical components. Unfortunately, this often means tearing down an engine, disassembling a machine or shutting down an assembly line, all of which cost precious time and money. And while there are other instruments and methods than can sometimes help determine the condition of wearing components–think eddy current or radiography, for example–nothing is quite as useful as a visual inspection. This is where the newest advancements in remote visual inspection (RVI) technology can have a huge impact on maintenance and repair expenses and, most critically, downtime.
RVI instruments have existed for nearly a century and, while the technology behind RVI has certainly evolved, the basic goal remains the same: to see into places an operator’s eyes cannot. The pathway to today’s state-of-the-art RVI instruments has evolved from rigid borescopes that relied upon mirrors and lenses, to fiberscopes that utilize highly flexible fiberoptic strands to transmit a remote image, to the current technology in which distally-mounted micro cameras are used to capture real-time, high-resolution images. Along the way, advancements in articulation mechanisms now allow a technician to accurately control exactly where the micro camera is pointed, even while it is snaked five or ten feet into a piece of machinery.
Today, the most common RVI instrument is a video borescope, and most video borescopes on the market can be broken down into three main components: 1) The articulating tip, which contains the micro-camera, LEDs and “bending section”; 2) The insertion tube, which can range in length from a few feet to several meters, and can range in diameter from 3.9mm to 8mm; and 3) The base imaging unit, which houses the main PCB, camera articulation controls, video monitor and power supply.

The videoscopes insertion tube can range in length from a few feet to several meters, and can be made of braided, stainless-steel tubing. Source: RF System Lab
Why RVI?
In addition to the obvious advantage of being able to see things operators could not otherwise see without time-consuming disassembly, there is another key reason to consider adding a modern video borescope to your tool kit, and that is the ability to document, through pictures and video, the condition of the inspected components. Visual documentation can serve three important purposes.First, pictures can be used to help explain to a customer why certain repair work needs to be done. It’s one thing to read an oil analysis report that turns up metal shavings in gear box lubricant, it’s another to see a color photo of a bevel gear with missing teeth. Second, visual documentation provides an insurance policy against any potential misunderstanding or disagreement over component condition or service work justification. In the example above, if the customer sees the condition of his bevel gear, and still decides not to replace the broken gear, he will be hard-pressed to come back to the service technician three weeks later when the gear strips out entirely and claim he was not properly informed of the severity of the problem. Forewarned is forearmed. The third reason is, when used over time, visual documentation can show the wear trends that occur with use. For example, by inspecting the stators of progressive cavity pumps at regular intervals–say every 10 hours of use–a technician can learn to gauge the remaining life of the stator and remove it from service before it chunks out on the job. Other types of inspections in which it is helpful to monitor and document the condition over time include engine valve inspections, boiler tube inspections and any inspection related to corrosion or accumulated blockage.
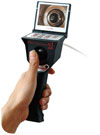
The base imaging unit houses the main PCB, camera articulation controls, video monitor and power supply. Source: RF System Lab
Industry and Product Trends
One of the key trends occurring with video borescopes is the simplification of design in order to allow the technology to “trickle down” into applications that previously did not justify the expense. This same trend occurs in many other technical and consumer product categories, from flow meters and thermal imaging cameras to GPS and digital cameras. With technology in general, devices that at one time were very expensive and complicated tend to become more affordable and easier to use, opening the door to much wider adoption. In the case of video borescopes, this “trickle down” trend has been fueled by the ever-smaller and more powerful cameras developed for use in cell phones and laptop computers, as well as advancements in micro-LEDs that deliver the necessary illumination. The result is that there are now video borescopes that deliver all of the key features–joystick articulation control, direct micro-camera imaging, on-board photo and video storage–at a fraction of the price seen only five years ago.We can see this trickle down effect, for example, in aviation MRO centers, where, until recently, only technicians in the engine shop used borescopes because of their cost, complexity and lack of portability. Now, because borescopes are less expensive, more portable and easier to use, their use is being extended to inspections of airframes, instrument panels, flap tracks and even ground support equipment. In other industries, borescopes are being used to inspect gear boxes, internal welds, pump vanes and combustion chambers in reciprocating engines. These are all applications for which the use of a borescope would have been cost prohibitive just a few years ago.
Another important trend is an increase in the portability of full-featured video borescopes. Gone are the days when a user had to pull out a large cart-mounted system just to do a quick inspection. Today’s scopes take advantage of the miniaturization that has occurred in camera and lens design, as well as the latest techniques in image processing and PCB manufacturing. What used to weigh 30 lbs., require a 120 volt wall outlet and come in its own suitcase now weighs less than 2 lbs. and runs on AA batteries. In the aviation industry, this means that a full-featured borescope can be transported as carry-on luggage when a tech has to travel to an AOG (aircraft on ground) location. Additionally, in such a situation, any photos taken with the scope can be easily emailed back to the shop for analysis or a second opinion.
Thanks to the increased portability, ease of use and lower cost of modern video borescopes, this technology is finding its way into many industries that have multiple, geographically dispersed locations, including onshore and offshore drilling rigs, natural gas compressor stations, heavy-equipment service trucks and small power-generating facilities.
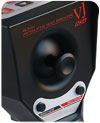
Many videoscope models offer joystick camera-articulation control. Source: RF System Lab
Choosing the Right Scope
In selecting the right video borescope application, it is important to choose a scope that has the critical features needed, without going overboard paying for features or add-ons that are unneeded or rarely used. For example, one feature available on some high-end video borescopes is referred to as a “measurement function.” This is an expensive add-on, but it can be worthwhile in certain applications, such as in the inspection of turbine aircraft engines, where tolerances for defects or damage are spelled out by the manufacturer. When there is a question as to whether a certain defect is within tolerance, a measurement function can help determine the answer. As anyone in the aviation MRO industry will tell you, repair work on an aircraft engine is very expensive, so the added cost of a measurement function on a video borescope can be worthwhile.While it is important to not buy a more complex or expensive borescope than needed, be careful not to buy the cheapest scope. A good understanding of basic requirements–the length and diameter of your access path, whether or not you require camera articulation, or how close you are able to get the camera to the inspection target–can help zero-in on an appropriate scope through a simple, five minute conversation with a knowledgeable sales rep. As with anything, try before you buy, and some companies will even ship a no-cost demo unit to evaluate in-house before making a buying decision.
A final consideration in selecting a borescope is the total cost of ownership, which includes not only the acquisition cost, but repair costs, ongoing maintenance costs and costs to train new employees on the system, if required. These items can add up over time, so be sure to inquire about these expenses when shopping for the right system. Also ask about warranty coverage and whether a loaner is available if the scope should need service.