When arteries in the heart become blocked due to coronary artery disease, one of the ways to treat it is through the use of a coronary stent. These are tubular support devices that can be surgically implanted into the coronary arteries to keep them open, allowing the arteries to supply blood to the heart properly. Over the last ten years, stents have become one of the most commonly implanted medical devices, and the process to place the stent into the body is only minimally invasive.
To ensure the safety and efficacy of every stent, rigorous testing is critical. In fact, the United States Federal Drug Administration (FDA) recommends that stents must be able to withstand 10 to 15 years of pulsatile loading in the human body, or in vivo. This equates to roughly 400 to 600 million heart pulses, or loading cycles. From a quality control perspective, this demands that stents be tested to ensure they can withstand exhaustive loading and unloading of up to 600 million cycles, which is outlined in ASTM 2477. When it comes to stent testing, this type of rigorous pulsatile fatigue testing often receives the most attention, but in fact, many other mechanical tests are performed throughout the design and quality control process. Raw material characterization, stent design selection, component testing, and stent deployment characteristics must also be evaluated to ensure a stent will safely and effectively help a patient survive.
Raw Material Testing
Stents are most commonly made from medical-grade stainless steel, cobalt metal alloy, or a nickel titanium alloy, known as Nitinol. Nitinol has several unique material properties, including being a high elongation metal, having the ability to recover shape after mechanical yield, and having the ability to relax and/or contract by varying temperature. Because of these characteristics, Nitinol is referred to as a “shape memory” alloy, or a “super-elastic” metal. Testing Nitinol material characteristics is most commonly done in a simple cyclic test to ASTM F2516, which requires Nitinol to be pulled in a tensile test to 6% strain, then unloaded to the point where tensile stress is nearly equal to zero, and then finally the material is pulled in a tensile test to failure. The main measurements reported in this test are upper plateau strength, which is tensile strength at 3% strain on the first loading curve, lower plateau strength, which is the tensile strength at 2.5% strain on the unloading curve, residual elongation, which is the difference in tensile strain at 7 MPa between the loading and unloading curve, and finally tensile strain at the maximum load achieved before failure. The residual elongation measurement is especially important for quality control purposes as it provides quantitative information on the unrecoverable strain, or unrecoverable energy. Materials engineers can vary the composition of nickel and titanium to optimize the material for desired results. When performing Nitinol tests to ASTM F2516, an accurate measurement of strain is especially important and best achieved using a video extensometer or automatic contacting extensometer.
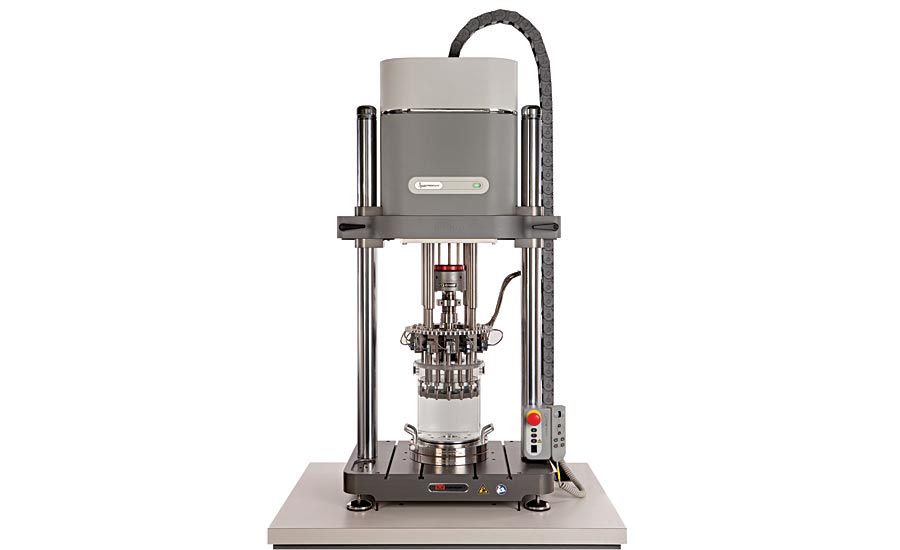
To ensure the safety and efficacy of every stent, rigorous testing is critical.
Stent Design Selection
The mesh pattern of a stent is often created using high-precision laser cutting to form simple or complex geometries. Manufacturing techniques can include wire braiding, laser sheet cutting, and laser tube cutting to form various patterns. One of the most common repeating patterns in a stent body is known as the diamond structure. To determine and optimize the stent body geometry, fatigue mechanical testing is often done on the diamond structure subsets. Most typically, this type of test is used to collect data to compare different diamond structures. These tests are often carried out in position control at 60 Hz to determine if one geometry outperforms another during fatigue testing.
Component Static Testing
Once the raw material and physical stent geometry are chosen, the stent body can then be created and tested. The two most common static tests performed on stent bodies are three-point bend tests and radial compression tests.
ASTM F2606 defines the testing requirements for three-point bending on balloon expandable vascular stents and stent systems. Three-point bend tests provide data that can be used to compare the flexibility of different products by direct comparison of load-deflection curves, and by comparison of calculated product stiffness data. In many cases, testing to ASTM F2606 is conducted in a saline bath at body temperature to better simulate real-world conditions.
ASTM F3067 requires an even circumferential force to be applied to the stent body in compression. Radial uniform compression should be applied to the stent body until the total stent body is reduced to 50% of the original diameter. Radial compression tests are typically carried out using an iris fixture that circumferentially surrounds the stent body. This test provides data that can be used to determine the maximum force required to compress a stent to 50% of the original volume. In addition, when a stent is inserted into the body, the stent may be subjected to forces that are higher than physiologically expected. It is critical that the stent body maintains rigidity and strength, while also being flexible. Radial compression tests on stents quantify these properties.
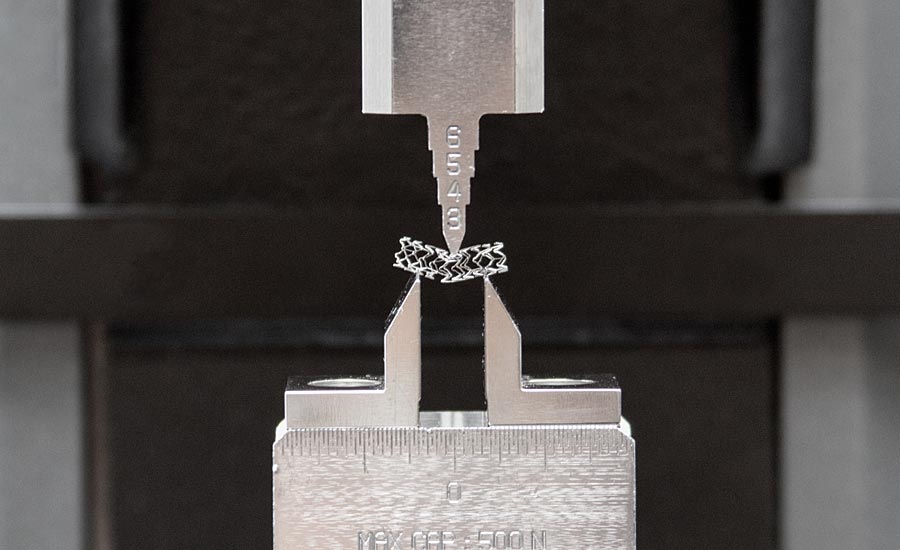
The two most common static tests performed on stent bodies are three-point bend tests and radial compression tests. This shows a three-point bend test.
Stent Deployment Testing
During an angioplasty procedure, a stent is placed into the coronary artery to clear narrowing due to a buildup of plaque or a blood clot. Most commonly, a needle is inserted into the femoral artery, and a guidewire is passed through the needle and guided through the arterial system until reaching the clot or blockage. Next, a flexible catheter is slipped over the guidewire and threaded up to the heart until reaching the site of the clot or blockage. Once the catheter is in place, the guidewire is removed. A second guidewire is then inserted with a collapsed stent on the tip. Many stents are inserted with a balloon which is used to inflate the collapsed stent. Once the balloon is inflated, the stent expands and locks into place, allowing the balloon to collapse and both the guidewire and catheter to be removed from the body. The path through the arterial system in which the guidewire, catheter, and guidewire with the stent must travel is convoluted. The frictional properties of this convoluted path need to be quantified in order to ensure easy and optimal delivery of the stent without harming the patient. Tortuosity testing systems or universal testing systems are often used to measure the frictional forces associated with this procedure. Guidewire and catheter frictional properties can be increased or decreased based on a variety of different lubricants and surface coatings.
With stents and other implantable devices, the cost of failure can be extremely high. Performing mechanical testing throughout the entire design and quality control process is critical to ensuring these types of devices will safely and effectively help a patient survive. Q