Many people find vision challenging, and complex vision systems certainly can be overwhelming. But vision is a powerful tool for automated quality control, and in many cases, inspections that previously required costly, complex vision systems—or multiple photelectric sensors—can now be completed with an economical but capable vision sensor.
Vision sensors are an especially great choice for users that are getting started with vision, have relatively simple inspection applications, and are looking for a solution that is intuitive and easy to implement quickly with minimal downtime.
This article describes several key benefits of vision sensing technology, ideal applications for vision sensors, and several considerations to keep in mind when choosing a vision solution for quality control.
What is a Vision Sensor and What are the Benefits?
Vision sensors are self-contained devices that include vision lighting, lens, and camera in a single compact unit, which simplifies implementation. Vision sensors are available with a wide variety of lens and lighting options to match a variety of applications with one simple device. The following are five key benefits of vision sensors:
1. Save time and costs. Vision sensors are typically smaller, lower cost, and less complicated than smart cameras, which makes vision sensors one of the easiest vision solutions to get up and running quickly. In fact, training on a vision sensor can take as little as half an hour with no previous vision experience. Furthermore, a vision sensor with an onboard display that doesn’t require a PC for programming can often be set up in a matter of minutes. A device with integrated lighting makes it even easier to set up a basic vision inspection with no additional devices required.
2. Use fewer devices to inspect multiple conditions. Vision sensors can be used for many simple verification and inspection applications. Because vision sensors capture a whole picture rather than a single point, a single vision sensor can often replace multiple photoelectric sensors and verify several conditions at once.
3. Meet a variety of application requirements with one model. Vision sensors that allow you to change lenses give you the flexibility to meet changing application requirements. For example, different lenses allow you to change the field of view or working distance of the sensor. Swappable lenses allow you to standardize on one device and change out lenses based on application requirements, which simplifies inventory requirements and saves costs.
4. Create contrast with colored lighting. For many vision sensors, you can also choose from a variety of colored lighting to help create contrast in your application. Different color lights can make features appear either brighter or darker to a grayscale (monochrome) camera. For example, use a red light to make red objects in the image seem lighter, or use a green light (opposite of red on the color wheel) to make red details stand out. This makes it easier for the sensor to identify missing or inaccurate details.
5. Verify shapes, patterns, colors, and more. Vision sensors can be either monochrome (black and white) or color. Monochrome vision sensors are often used to verify the presence or shape of objects or to match patterns where the actual color is not necessary to differentiate between pass or fail condition. Meanwhile, a color imager sees in true color and is used for inspections where color is the only difference between pass or fail condition. For example, a color vision sensor can be used to determine the color of trim in the automotive industry or to verify the color of a label in consumer packaged goods.
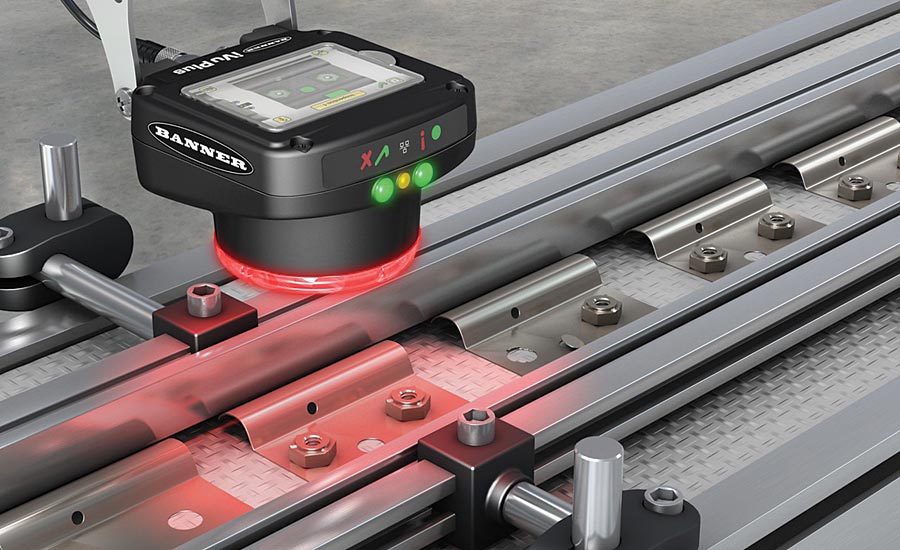
A vision sensor verifies punched holes on a metal part.
Ideal Applications for Vision Sensors—And When to Upgrade to a Smart Camera
Vision sensors are best for simple quality control applications including presence/absence verification, matching, label inspection, verifying the correct color or shade of an object, etc. A great first vision application using a vision sensor is a pattern-match inspection since it simply requires capturing an image of a correct condition. When the sensor detects a part that doesn’t match, the sensor sends a fail output to the line, and the product is rejected. For example, a vision sensor can be used to verify the presence of a label on a product. Another good application is complete assembly verification. For example, a vision sensor can be used to verify that all correct components are present in a completed medical kit assembly.
The next step after a vision sensor would be a smart camera, which usually requires a PC for programming but provides additional capabilities such as feature measurement and flaw analysis. Smart cameras are ideal if you need more functionality than a vision sensor, but still need a versatile, easy-to-use solution. Look for a camera with intuitive software that can handle complicated inspections while still being user-friendly.
4 Questions to Ask When Choosing a Vision Solution
When choosing a vision sensor, it is important to make sure that it will work for your application. The following questions can help you evaluate your application requirements before making a decision:
What is the speed of your application? It is important to verify that the vision solution is suited to the speed of your application. The more conditions that need to be inspected, the longer the inspections will take.
What is the distance from object to sensor? How far away from the objects will the sensor be mounted? A vision sensor should typically be mounted less than 12” away from the target. For farther distances, a higher end system may be required.
What size objects are you inspecting? You will need to make sure that the object(s) fit within the viewing window of the vision sensor. Note that vision sensors have a more limited field of view compared to more expensive vision solutions. Therefore, vision sensors work best for small parts, or assemblies with small quantities of parts. If a wider field of view is needed, a smart camera may be a better option—offering more functionality while still being easy to commission and use.
What are you looking for? This is the question where many people struggle when getting started with vision. You know you are looking for a “good” condition, but what counts as good? What are your true pass/fail requirements? For this, you’ll need to evaluate your tolerance for less than perfect parts. One way to do this is to find your “best bad” part and your “worst good” part and set the tolerances for the sensor at both ends of the spectrum. Setting tolerances is essential for any vision application and will help ensure you are not wasting parts and material by rejecting parts that should be considered passable—or allowing parts through that should have been rejected.
After answering these questions, the next step is to try out a solution. Every vision application is unique, and it is best to try out the device in your real-world conditions to make sure it works for your application. Finally, partner with a manufacturer that also offers smart cameras, which makes it simpler to upgrade if needed. V&S