A machine vision interface connects a camera to a computer, transferring image data for processing and analysis. What you choose will impact your application, your system component options, and your results for a long time to come.
Machine vision interfaces have changed dramatically over the years, and a radically different future lies on the horizon. Selecting the wrong interface now could leave you with an expensive vision system that can’t reliably achieve the performance you require. Today there are five primary machine vision interfaces: Camera Link, GigE Vision, CoaXPress, Camera Link HS, and USB3 Vision. 10GigE, which is 10x the bandwidth of GigE Vision, and most recently, 5GigE are new interfaces that have just emerged. Currently under development is the newest version of CoaXPress, CXP-12, as well as more GigE Vision standards, 25GigE and 50GigE.
How do you decide?
Each interface offers certain capabilities: GigE Vision affords long cable lengths at low cost; Camera Link is known for its reliability and data integrity; CoaXPress features high data transfer speeds; Camera Link HS has high bandwidth and reliability; and USB3 Vision has low cost cables with high bandwidth.
Selecting a machine vision interface represents a long-term investment and is always application-specific. Here are some considerations to help you avoid making costly missteps.
1. What Are You Trying to Achieve?
The first and possibly most important consideration is to align the specific needs and requirements of your application with the capabilities of the interfaces under consideration.
The evolution of machine vision interfaces has been driven mainly by a constant need for higher bandwidths to support vision systems with higher resolutions and faster frame rates. Resolution, measured in pixels, and speed, measured in frames per second, will be primary technical considerations in your selection process.
Bandwidth essentially determines how much image data can be transferred and how fast without data loss. It’s vitally important to choose an interface with enough bandwidth for your needs. For example, if the interface isn’t fast enough or broad enough to handle your frame rate and resolution, signal and data degradation can distort imaging quality and even make imaging impossible. You must align the capabilities of the interface with the results you want to achieve.
2. Interface Comes Before Camera Selection
Oftentimes a camera becomes the initial focus of research. This may seem logical, but it can be a costly misstep. The interface must be able to realize the technical capabilities of the camera, and you may choose a camera only to find the interface won’t work for you.
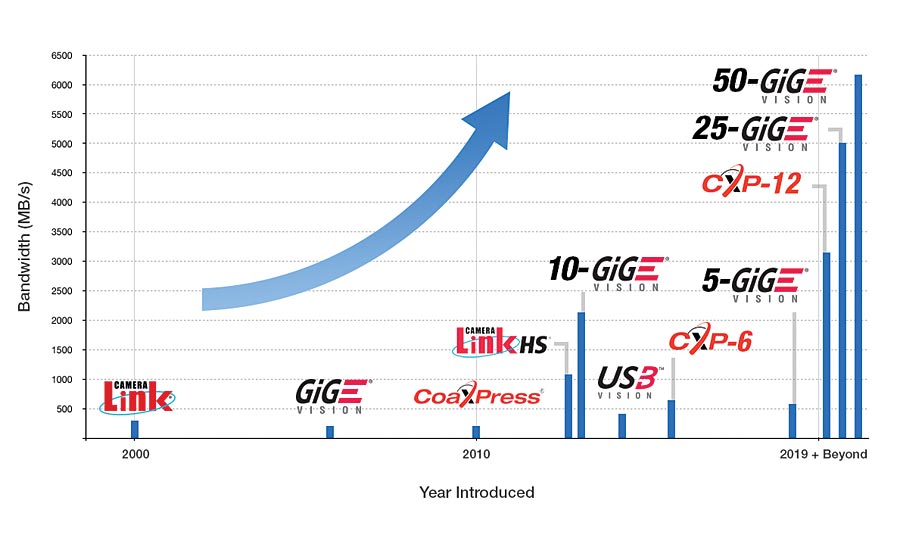
Today there are five primary machine vision interfaces.
The interface dictates the data transfer rate from the output of the camera to your host and is just as important as your camera selection. If you’re considering a cutting-edge, ultra-high resolution sensor, or you simply know that your application will require as much resolution as possible, it’s especially important to accommodate these technical needs by considering an interface first or you won’t get the high-resolution results you require.
3. Ensure Cable Length and Durability Are Compatible With Your Facility
Cable length is another crucial technical consideration. Longer cable lengths are often desired by machine vision users, but the bandwidth of some interfaces simply don’t allow for long cables.
USB3 Vision, for example, is one of the most popular machine vision interfaces in the U.S. It boasts a 350 MB/s bandwidth—fast enough to handle high frame rates and high resolutions for some of today’s most advanced cameras. USB3 Vision cables, which differ from everyday USB3 cables, are readily available at low prices without an expensive frame grabber.
Like all machine vision interfaces, USB3 Vision has a number of benefits, but also some drawbacks depending on the needs of your application.
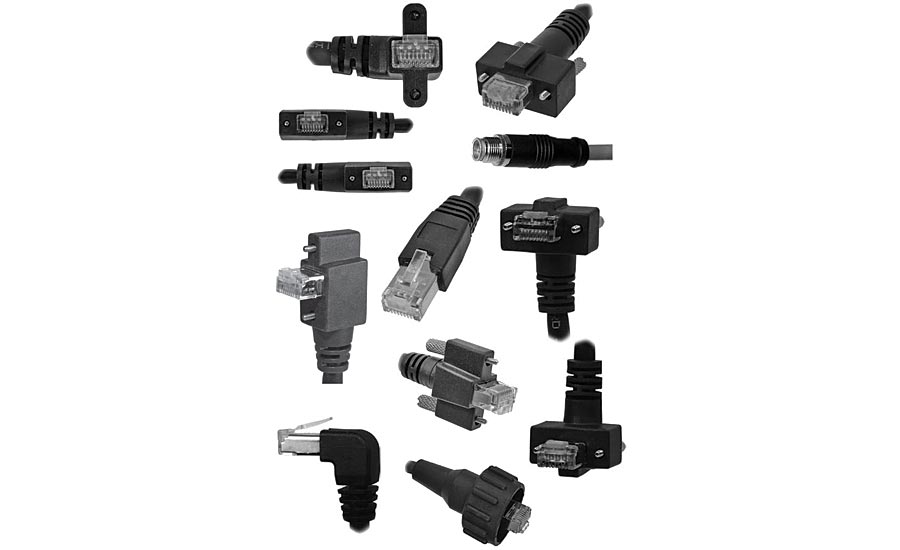
GigE cables are long, affordable and readily available, but less deterministic.
The cables have a maximum length of three meters. In some floor layouts, the demand for long cables is non-negotiable, and sometimes vision systems need to be protected from machinery, making the USB3 Vision standard difficult to use in both cases. These cables can sometimes be sensitive to noise and vibrations too, which may make them unsuitable for tough environments. While there are technical ways to extend the length of these cables, it’s extremely challenging and may not deliver the expected results.
4. Assess the Tradeoffs
The GigE Vision standard and Camera Link standard were released around the same time and provide a great example of assessing tradeoffs. Technically they could be used in most of the same applications, but their various performance and cost tradeoffs in some scenarios have to be considered.
GigE is one of the most popular interfaces in the U.S. and features low cost connectors and cables that can reach 120 meters in length or more. They’re readily available with bandwidth around 125 MB/s without needing a frame grabber. GigE offers many benefits, especially in terms of its low cost, but it has disadvantages too. It is vulnerable to PC interruptions because the computer it is connected to runs programs in the background, leading to errors in data transfer. While GigE software has error detection and error correction features that make it reliable enough for a wide range of applications, your particular needs may demand something more deterministic.
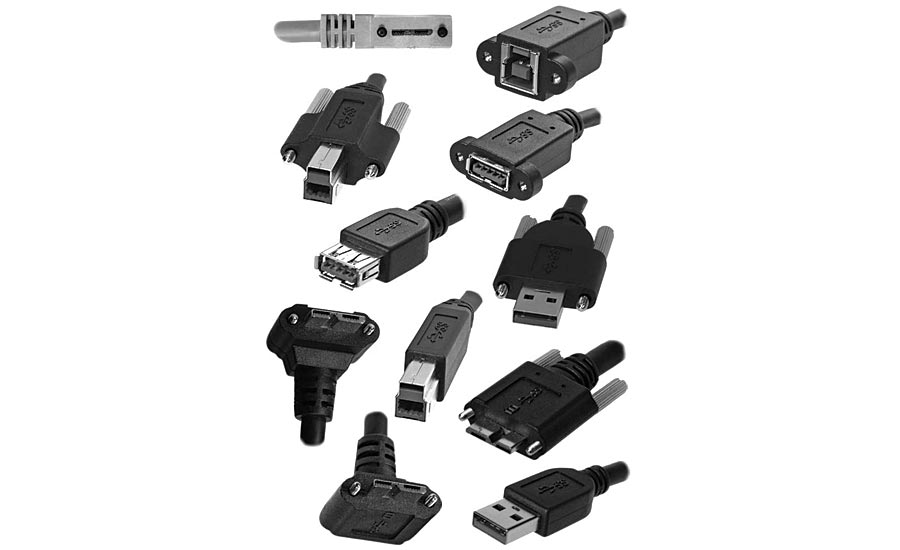
USB3 Vision cables offer high bandwidth at low cost, but short cable length and sensitivity to vibration.
Camera Link, on the other hand, is a highly deterministic interface. All interfaces lose some data, but Camera Link loses this data in a highly predictable manner, making it a reliable vision interface. But like GigE Vision, there are tradeoffs when using Camera Link. Mainly, it’s the fact that the cables are costly—production volumes were never high enough to drive down prices. Plus, Camera Link interfaces require a frame grabber, which is an additional cost.
Each interface can be a great solution, but they aren’t interchangeable. While machine vision interfaces are constantly improving, assessing their individual tradeoffs in current versions is important to finding the best interface for your application and budget.
5. Consider Emerging Vision Interfaces
Emerging vision interfaces may offer the right solution for your application, as they seek to solve any issues that have arisen in previous vision standards.
10GigE, for example, is a relatively new interface with 10x the bandwidth of normal GigE, but all of the same cable and connectivity specifications still apply. Typically, 10GigE is used for extremely high resolution or high-speed applications such as virtual reality—now a part of proof of concept in manufacturing engineering—or sports broadcasting.
5GigE, following the original GigE standard, is an even newer development. Oftentimes, 10GigE is too much bandwidth for typical machine vision applications; so 5GigE was created for industrial use. With a slightly higher bandwidth than USB3 and an affordable NIC card, 5GigE is now one of the highest performing machine vision interfaces.
Embedded vision systems, where image capture and processing capabilities are embedded into a larger system with a different purpose, are a disruptive technology with major growth potential. These systems need small, simple interfaces for design purposes. Today, the MIPI interface, originally intended for mobile devices, is the standard interface in these scenarios. While embedded systems are somewhat new, they’re what’s enabling everything from self-driving cars to augmented reality and smart medical devices, among countless other cutting-edge technologies.
Interfaces are always evolving, and the newest solutions tend to offer exciting new possibilities.
6. Keep the Future in Mind
As mentioned, investing in a machine vision interface has implications for the future of your system. It’s important to keep an eye on how interfaces impact the technological landscape for machine vision applications.
CXP-6 and CXP-12 are the next generation of CoaXPress standards currently under development. They will feature 2.5 GB/s and 5 GB/s bandwidths, respectively. Also under development are 25GigE and 50GigE vision standards that will feature 3.1 GB/s and 5 GB/s respectively. While some are closer to reality than others, each one of these future interfaces will allow for dramatically increased bandwidth.
Extreme bandwidth levels will change entire industries. For example, factories of the future may be “dark” factories, with no people in them. This may sound far-fetched, but there are dark factories currently in development, and there are a few examples around the world of farms operating with few or no human workers.
For automation on this scale, vision systems will need to enable mobility, flexibility, and intelligent decision-making in real time in a dynamic environment. This will require enormous amounts of image data to be transferred and processed, including machine to machine communication, putting a large responsibility on extremely high bandwidth interfaces to transfer all of this information.
The Right Choice for Long-Term Productivity and Quality
Avoiding costly missteps when selecting your machine vision interface starts with a clear understanding of the needs of your application and the results you require, not just today but as you expect your business to evolve. Get to know your options and select the interface before you select a camera so that your machine vision system can deliver the long-term productivity and quality you need to remain competitive. V&S