Quality control applications that require precise measurement can be some of the most challenging applications to solve. Very tight tolerance requirements demand a reliable solution that can measure parts in micrometers to detect the smallest variations in part size, thickness, orientation, placement, and more. Ensuring parts meet strict quality standards can help reduce problems downstream and reduce the risk of product recall due to imperfect parts.
Laser measurement sensors are a common solution for precise part inspections. However, real world conditions—including variations in target color and reflectivity, fluctuations in ambient temperature, and vibration from improper mounting—can make precise measurement challenging, even for laser sensors that perform well in perfect laboratory conditions. Therefore, it is important to understand the factors that can impact measurement precision in order to identify a solution that can overcome these challenges.
Below are several key considerations to help you find the right sensor for your most precise quality control applications.
1. Start with the Specifications
Resolution is one of the first specifications you might look at when choosing a sensor for precise inspections. Resolution tells you the smallest change in distance a sensor can detect. So, a resolution of 0.01 mm means that the sensor can detect changes in distance of 0.01 mm, or 10 micrometers. For precise applications, measurement in micrometers is essential. For example, in the semiconductor industry, very small IC chips must be fully seated in nests before being delivered to testing stations to ensure the integrity of the tests. A laser sensor with resolution in micrometers is necessary to identify minor height differences when one of the razor-thin chips is either missing, stacked on top of another chip, or even slightly tilted in the nest.
However, while resolution is very important for precise applications and can get you in the ballpark when choosing a sensor, resolution specifications only represent a sensor’s performance in “best case” conditions. Because of this, resolution specifications often do not provide a complete picture of a sensor’s capabilities in the real world and sometimes overstate sensor performance. In typical applications, resolution is impacted by target conditions, sensor distance to the target, sensor response speed, and other external factors.
Therefore, it is important to consider the resolution specification in combination with other indicators of the sensor’s capabilities. For example, in discrete sensing applications, it is also important to consider the sensor’s repeatability (how reliably the sensor can repeat the same measurement in the same conditions) and the sensor’s minimum object separation (the minimum distance a target must be from the background to be reliably detected).
For analog applications, it is important to consider both the sensor’s resolution and its linearity (how closely the analog output approximates a straight line across the measuring range) to ensure a reliable output across the full range of the sensor. When combined with resolution, these additional specifications provide a more complete picture of sensor performance in the real world.
2. The Challenges of Real-World Targets
One reason resolution alone is an imperfect specification is because real world targets are often difficult to measure consistently. Depending on the industry and application, objects may be very dark (low reflectivity), glossy (high reflectivity), or contain multiple color transitions—all of which can significantly impact measurement reliability.
To mitigate this issue, some laser measurement sensors feature automatic gain adjustment, which means the sensor dynamically reduces or increases its power based on the reflectivity of the target. This ensures targets of varying colors and reflectivity are all measured reliably. Another feature to look for in a precision measurement sensor is a small spot size, which minimizes measurement variation across color transitions.
3. Temperature Fluctuations
Precision measurement can also be greatly affected by changes in ambient temperature. For some sensors, natural temperature fluctuations of even a few degrees up or down throughout the day can cause the sensor’s measurement error to double, eliminating any benefit of a precision sensor. Therefore, it is essential to choose a sensor with high thermal stability for reliable measurement regardless of the surrounding temperatures.
When evaluating a sensor for use in these conditions, an important specification to look for is the sensor’s temperature effect. The temperature effect refers to the measurement variation that occurs due to changes in ambient temperatures. A temperature effect of ±0.008 mm/°C means that the measurement value can vary by 0.008 mm for every degree of change in temperature. A sensor with minimal temperature effect is critical for precise sensing applications since the induced error from just a few degrees of temperature shift can greatly impact sensor results.
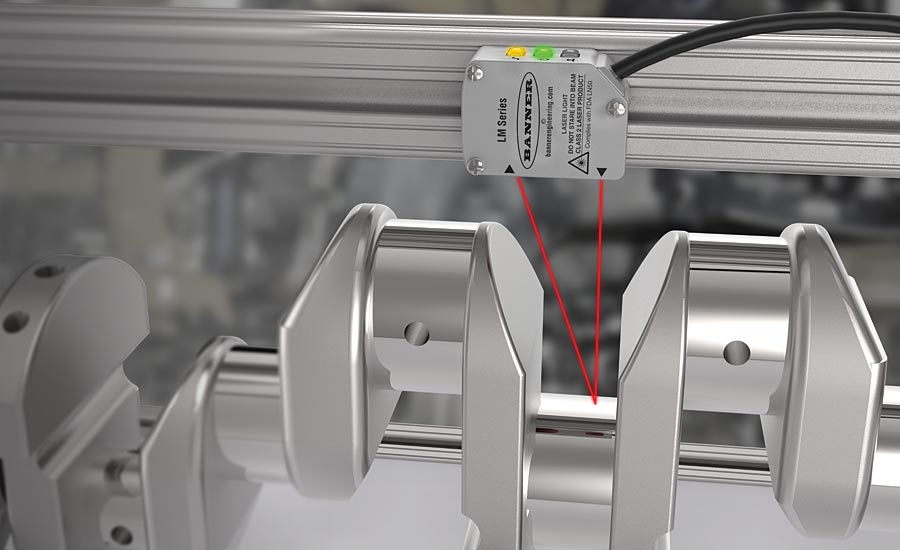
The LM laser measurement measures crankshaft runout to ensure that parts meet tighter tolerances with fewer defects.
4. Sensor Configuration and Monitoring
Another important factor is sensor configuration, because the movement of pushing buttons on a sensor can negate the sensor’s precision. Therefore, a precision measurement sensor must offer remote programming capabilities, including via IO-Link, a remote input wire, and/or a remote sensor display. Some precision measurement sensors forgo buttons entirely to ensure that the sensor’s precision cannot be accidentally compromised by maintenance staff.
Remote programming capabilities not only help maintain precision, but they also enable a host of other benefits. For example, with some IO-Link sensors, users can also monitor the device remotely, including monitoring internal sensor temperature, to identify and prevent potential problems before they occur. In addition, users can easily monitor, configure, and troubleshoot sensors in hard-to-reach locations.
5. Application Speed
Many precise quality inspections are also high-speed applications. For these situations, look for a sensor with a fast, sub-millisecond response speed and sampling rate to reliably identify errors on quickly moving parts, reduce inspection times, and increase machine throughput.
For example, in the automotive industry, engines and motors require many rotating components, such as crankshafts, to function properly. An uneven crankshaft impairs the balance of the motor and creates heat and vibration which can cause equipment to malfunction. To prevent future mechanical failure, a rigid runout tolerance must be set, and parts must be tested frequently for errors. This requires an extremely precise measurement solution of the quickly moving crankshaft. A sensor with a 0.5 ms response speed and 0.25 ms sampling rate can reliably measure targets at high speeds and rapidly identify problems.
6. Mounting Considerations
Finally, mounting stability is crucial for a precision measurement sensor. Even with the best specifications, if a precision sensor isn’t mounted securely, measurements will not be reliable. To reduce the risk of measurement error, ensure that the sensor can be securely fastened to the mounting fixture and kept away from excessive vibration.
In precise part inspections, a reliable solution is a must. Finding a precision measurement sensor that works for real world applications involves examining a variety of specifications and features to ensure the sensor can hold up to challenge. V&S