Simply put, product quality is always on the mind of a production manager. But what exactly characterizes a quality product? Is it when CMM inspection data reads good versus bad? Or when a product is delivered on schedule with minimal downtime and resources were used wisely? Manufacturers continue to discern part quality with new data-driven technologies while pressed with increasing production demand.
For years, the QC department was labeled a necessary bottleneck within the production process. But that era is long gone, as measurement professionals have forged efficiencies in their operations with the help of metrology equipment manufacturers. The demand for faster production while maintaining product quality set the industry on a completely new trajectory. Metrology OEMs were pushed to rethink their traditional approaches to inspecting a product. IoT data is playing a big role and it had to move forward with smart manufacturing at the forefront.
Quality Measurement: The Evolution of Measuring Sensors
Traditionally coordinate measuring machines (CMMs) were often equipped with a touch trigger probe that would touch the part in a pre-determined spot, taking one point of measurement at a time. While this method is good for ensuring highly accurate measurement data, it is not ideal for manufacturers with strict deadlines or lofty production goals. In response, a variety of sensors were introduced to the market offering diverse levels of capability.
One of these new sensor categories, the scanning probe, provides significantly faster inspection of parts than traditional touch trigger measurement. The CMM moves the probe along the part profile and captures thousands of points at a time. Scanning probes are particularly effective for evaluating part features such as form, location and size.
Scanning probes can also significantly decrease measurement cycle time compared to touch trigger probing methods. However, for parts that have difficult geometries or multiple material types, laser line scanners offer better flexibility for capturing surface form characteristics and generating point clouds without physically touching the part. This sensor category gives manufacturers the ability to obtain a 3D viewpoint of the part to investigate sections and extract certain features.
All of these sensor options have a place within the marketplace, but each different approach sacrificed speed, flexibility or accuracy depending on the probe. Tactile probing can be slow for certain applications, and laser scanners are often not accurate enough for today’s challenging tolerance requirements. These realities brought on another sensor evolution of frequency-modulated interferometric optical distance measurement.
This noncontact optical sensing range combines speed, accessibility and accuracy for distance measurement. Interferometric measurement offers the accuracy and reliability comparable to tactile scanning probes, at higher scanning speeds, increased measurement range and the general optical advantage of noncontact measurements. This is the next-gen alternative for high-precision tactile measurements when speed is important, parts are difficult to access with tactile probes, or when parts may deform or be damaged by touch probing.
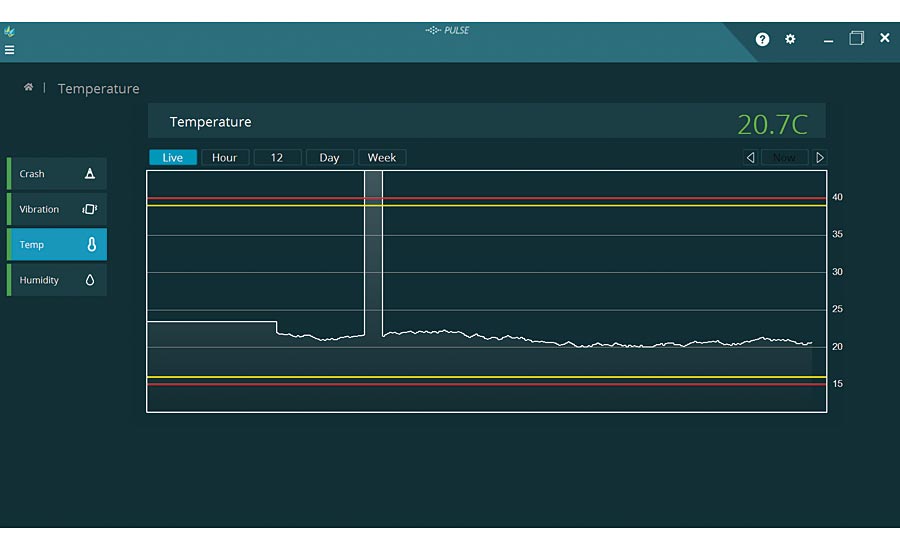
PULSE uses a range of sensors to monitor, collect and store environmental data surrounding the CMM in one simplified user interface.
Quality & Efficiency
While choosing the right sensor for the application at hand is a good first step, the quality department’s efficiency goes beyond sensor selection, and must consider environmental data surrounding the quality systems. As the Industrial Internet of Things (IIoT) has made its big debut, companies working in quality were interested in finding ways of using this technology to provide smarter data to manufacturers and ultimately enhance their efficiency. One aspect of IoT involves the use of sensors within the machine frame to track environmental changes surrounding the CMM. If at any point the CMM stops due to an environmental disturbance, then the entire process is affected as well.
Environmental events can affect measurement data including vibration, temperature spikes, probe crash events, humidity, etc. By tracking these events, manufacturers obtain increased confidence in their measurement results. A major advancement for the CMM market is the introduction of remote environmental monitoring software designed with the Internet of Things (IoT) in mind. This technology monitors the measurement execution status along with several typical environmental causes for interruption or failure in the measurement process. Not only are these environmental conditions monitored, but they are recorded to provide the actionable information needed to keep the process operating smoothly.
In addition to increased confidence, manufacturers can begin to eliminate environmental cause to bad data or verify it when anomalies occur. Furthermore, they will spend their time more efficiently during root cause analysis by ruling out environmental events. Environmental data may also shed some light on issues that could potentially cause downtime in the near future. For instance, tracking this data over time gives manufacturing engineers visibility to trends such as wear on vibration pads that could potentially need replacement.
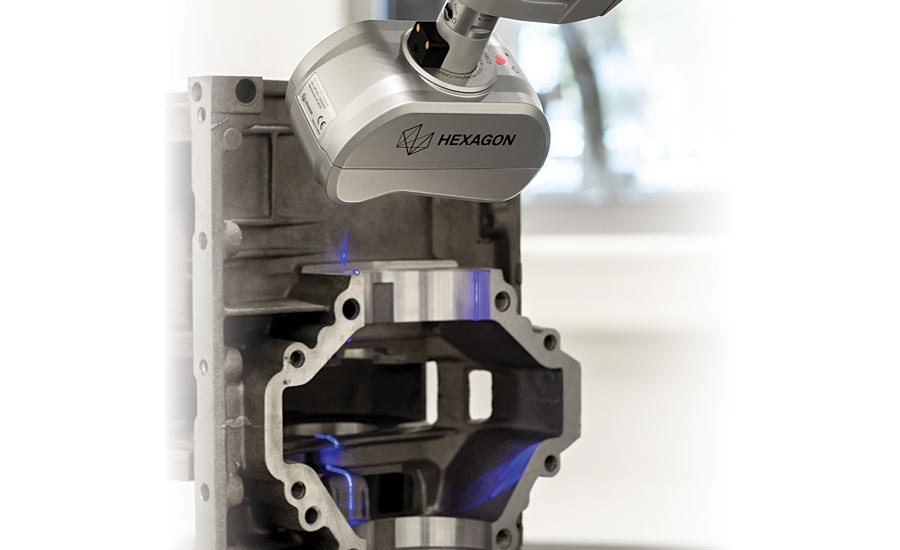
This new blue laser line scanner was designed for use with a wide range of applications and measurement surfaces, whether surfaces are very dark or shiny.
Quality Data
With new metrics like Overall Equipment Effectiveness (OEE), a gold standard for improving manufacturing efficiency, manufacturers are relying on data captured from different product development touchpoints to help them make smarter decisions on equipment to purchase, resources to obtain, and cost-effective ways to run production more smoothly. Some companies are even implementing special efficiency teams to track and communicate with senior management on ways to improve efficiency.
CMM data has always had its place in manufacturing. But today, data plays a huge role in smart manufacturing, and companies are still mining through it to find the answers they need. Adding sensors to measurement systems for tracking anomalies is one part of the equation. But cutting through the noise to find the data that truly matters is the challenge.
So, what types of data will provide companies with the feedback required for better decision making?
Utilization information found by tracking and monitoring machine data, such as run time and downtime, can provide production managers a clear vision of resource gaps and which departments are being the most efficient. In addition to utilization, tracking data over time will provide loads of information to help with decision making. Performing trend analyses provides a better look at how manufacturing equipment is performing over time. In some instances, it may even allow those analyzing the data to see when machines should be calibrated or the wear on tooling.
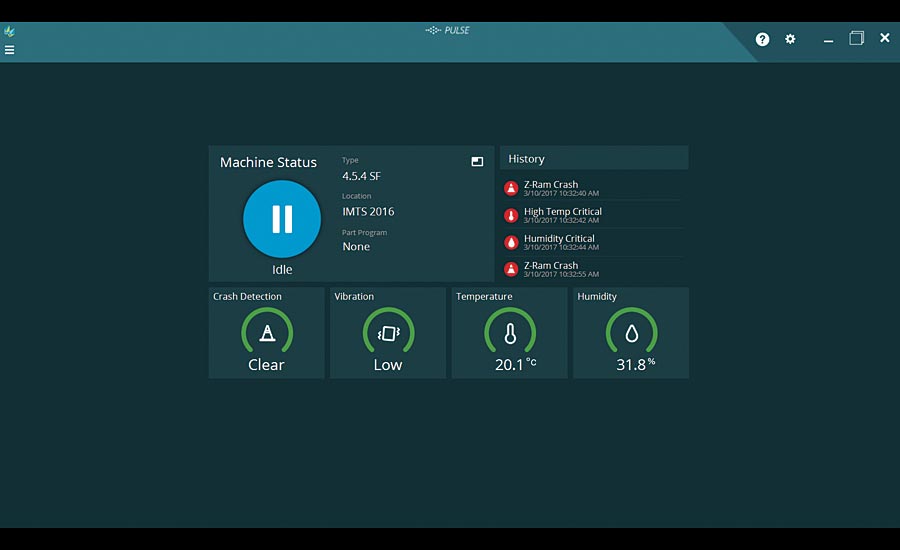
Within this dashboard, users can analyze environmental spikes such as temperature to verify measurement accuracy.
Future of Quality in Manufacturing
The future of quality in manufacturing will be connectivity within the enterprise. Connectivity takes data to a whole new level by letting information flow throughout the production process, giving manufacturers results that allow them to act and communicate more quickly. Back in the day, quality was seen as a CMM operation conducted away from the rest of production and often treated as such in a separate area of the factory floor.
Today, quality and quality data are being pushed throughout production optimizing the process in real time.
By capturing and sharing data throughout the product lifecycle, whether its source is a CMM or a scanning sensor, manufacturers have a clearer picture of their quality operations. The access to on-demand actionable data leads them to take corrective steps to optimize output, minimize downtime and utilize resources more effectively. Not only does having a connected ecosystem provide better decision making, it can also impact the way manufacturing machines work with each other. Now CMMs with various enhancing sensors can connect with each other, and other manufacturing devices. Based on this data, smart decisions can be made such as automatically scheduling maintenance, running trend analysis, or scheduling machines for different jobs. Q