For medical device manufacturers, having a product that functions as designed is critical, as a person’s health—or even their life—could be at risk. It’s one thing if my Alexa won’t respond to a voice command to remind me of a task, but it may be life threatening if my asthma inhaler won’t give me the medication I need when I’m struggling to breathe.
Medical technology advancements improve and sustain lives like never before. When a problem occurs with a medical device, actions to identify the root cause, correct the problem, and prevent it from happening again need to occur quickly. Having an effective corrective and preventive action (CAPA) process ensures timely resolution of issues.
FDA, ISO, and the Product Record
In an FDA-regulated market such as medical device manufacturing, the key to introducing new products effectively is maintaining a tight connection between your product information, quality, training, and audit processes. Furthermore, ISO 13485 standards must be adhered to in order to demonstrate quality systems are implemented and maintained properly. Together, FDA regulations and ISO standards help inform best practices for compliant quality management processes.
It can be challenging to meet regulatory requirements while trying to launch a product quickly. Medical device companies must manage a complex bill of materials (BOM) containing all the mechanical, electrical, and software components. In addition, they need a way to track and manage an approved manufacturers list (AML), an approved vendors list (AVL), the design history file (DHF) and design master record (DMR), regulatory and environmental compliance information, and engineering changes—in context with all related quality issues and corrective actions.
The FDA Title 21 CFR section 820.100 requires the establishment of necessary CAPA processes. All product companies, medical or otherwise, strive to follow closed-loop CAPA processes whether they are connected to an underlying product record or not.
Initial Steps: Identify, Document, and Approve the CORRECTIVE Action
The first part of the loop addresses the typical CAPA quality process to identify, document, and approve the corrective or preventive action. The second part takes the actions and updates the impacted systems and processes.
In these initial steps, a cross-functional team determines what the root causes are for a given problem documented in a customer complaint, nonconforming material report, audit findings, or other sources of quality issues.
As issues are identified by employees, partners, or customers, they are recorded. The records will include the problem description or symptom, the severity of the problem, product identification information (e.g., serial or lot numbers), and relevant usage information like the operating environment.
A cross-functional team then analyzes the issue. Customer support, engineering, and quality teams may work together to research the problem and try to replicate it. Once it’s understood, the team determines the root cause, documents it, and identifies corrective actions. These may include changes in product design, new suppliers, or changes to the manufacturing process.
That proposed resolution is then reviewed by the impacted groups for approval, typically as part of a corrective action request (CAR). Once approved, the necessary changes are documented and may be driven by engineering change orders (ECOs) if the design or suppliers are affected or need to change. Typically, the final resolution or corrective actions will address one or more of these elements, which are part of the product record:
- Personnel training
- Product design
- Manufacturing or test documentation
- Purchased products or services
Closed-Loop Steps: Change Product Records, Update Downstream Systems
The second part of the CAPA process closes the loop from problem identification through problem resolution. Because most CAPA processes relate to one or more elements of the product assembly and design, a CAPA system tightly connected with the product record eliminates silos and ensures a more traceable approach—so all impacted teams, from quality to engineering to manufacturing, can view and collaborate around the product record and resulting quality or CAPA issues.
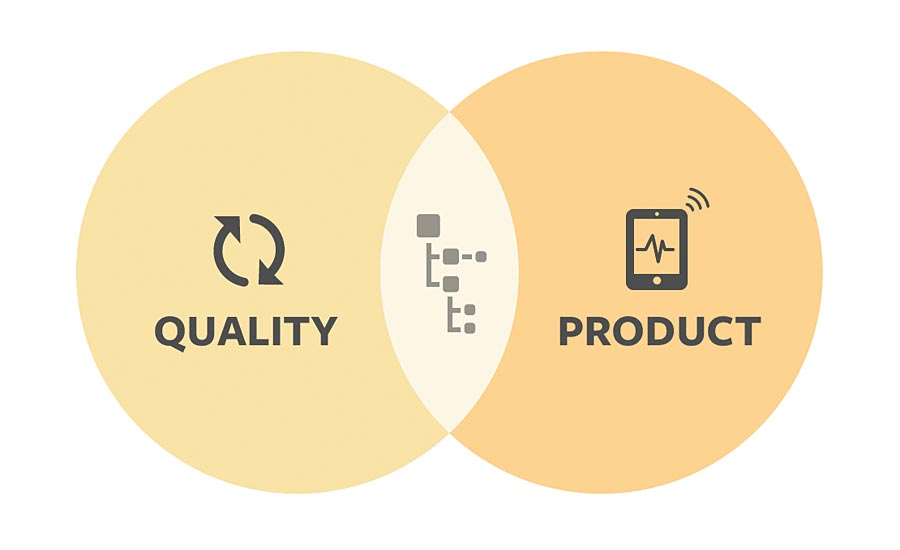
Because CAPA resolutions relate directly to one or more parts of the product record, a closed-loop CAPA process should manage the initial steps to identify, analyze, and determine root causes, along with documenting the steps to implement resolutions to the problem with links from the CAPA record to the product record. This ensures all impacted teams, from design to manufacturing, know about outstanding issues and can easily participate in resolving the problem. This connected nature between product records and quality or CAPA processes is known as a product-centric quality management system (QMS) approach. Let’s consider the corrective actions that may be taken.
Personnel Training
If an issue is traced to an employee or an external team member who is not following the latest instructions or procedures, changes to training or procedures may be necessary. A product-centric QMS system includes training record-management that notifies the person, tracks training activity, and tests for competency. The CAPA loop closes when the training record is linked with the product record and associated training plans. Any required changes to personnel training can be documented, corrected, and linked via a CAR.
Product Design
When the team decides the product needs to be changed, an engineering change process manages this resolution. An ECO describes the change, the reason for it, and tracks the change to the product record. A redlined BOM designates changes in components, assemblies, quantities, or possibly approved manufacturers’ parts.
The CAPA loop on product design issues closes when the product-centric QMS system links the ECO with the CAPA that initiated that ECO.
Manufacturing and Test Documentation
Occasionally, the documentation, like an assembly instruction, does not reflect the most recent change to the product design causing the product problem. In this case, an ECO will be used to propose and approve changes to one or more documents. ECOs clearly explain the description and reason for the changes.
For documentation issues, the CAPA loop closes when the ECO links to the impacted documentation as part of the CAR. All team members can see the change and what started it, and then access the updated released revision of the documentation as needed.
Purchased Product or Service Issues
Finally, a problem may be traced to a purchased product or service. If a purchased part or service is the root cause of a product problem, the manufacturer will find an alternate part and update the AML to document the change.
The CAPA loop closes through the captured link between the CAPA process and the change process, implementing the new approved manufacturer’s part.
Connecting Quality to the Product Is Key
Product-centric QMS provides your extended product team controlled access to quality records and product records. All of the impacted teams can see quality issues and resulting resolutions in context to the product design record. And, they can see all of the proposed engineering changes to BOMs, approved manufacturers, or documents. Without a single product-centric QMS solution, you would need to continually reference quality, training, and CAPA processes and try to relate them to the latest product record design stored in a separate system.
Connecting to Downstream Systems
A product-centric QMS approach helps close the loop further by connecting with downstream systems.
When an ECO is released, purchasing, manufacturing, and supply chain partners need to know immediately. A product-centric QMS solution includes the complete assembly or BOM and can instantly update downstream systems like enterprise resource planning (ERP) upon approval by all required stakeholders. Passing real-time BOM changes via an automatic integration to the ERP system eliminates manual data entry and errors.
When comparing product-centric QMS and document-centric QMS, the ability to pass BOM information via an automated integration is the key ingredient missing from paper-based, hybrid, and document-centric quality systems. Integrating cannot be done automatically since the BOM record is not managed in a relational database that downstream systems require.
Conclusion
Connecting CAPA and product processes enhances and saves lives. It also helps today’s medical device manufacturers innovate more rapidly by bringing teams, product records, and quality processes together for maximum traceability throughout the entire product lifecycle. This product-centric QMS approach simplifies compliance with FDA, ISO, and other regulatory bodies to help medical device companies deliver life-changing products to make the world a better place. Q