Which is more important to you: complying with industry and federal regulations, or improving the efficiency and profitability of your operations?
It might seem disingenuous to oppose compliance and continuous improvement so starkly. After all, continuous improvement is a means of attaining quality, and compliance is a means of documenting it—two sides of the same coin. But it’s a tradeoff many manufacturers face every day. In highly regulated industries, the cost of noncompliance is often higher than the opportunity cost of incremental improvements to processes. In the course of certifying and maintaining a QMS, processes can easily become rigid, and many manufacturers leave money on the table for fear of triggering an audit or violating regulations. What I want to show here is that compliance and continuous improvement need not exist in tension, even in the most heavily regulated industries (pharmaceutical, medical device, aerospace and defense). With the technologies currently available to manufacturers, it’s possible to have both.
But why does continuous improvement seem like a Faustian bargain for so many manufacturers? Why does it have to be one or the other? To answer these questions, it helps to pull apart compliance and continuous improvement. There are good reasons why they’re hard to reconcile.
Striking a Balance
In the last half century, manufacturers have developed a host of different continuous improvement methodologies. Lean, kaizen, lean kaizen, TPS, Six Sigma, 5s, agile—over time, adherents have refined each to a science. It’s likely you use one or another, or a mix, in your own operations. Though each methodology varies in its focus and scope, they all share a single trait: each method helps practitioners identify areas of inefficiency in order to implement solutions in ever-tightening cycles of improvement. These cycles are ongoing—continuous. There is no horizon to continuous improvement, just gradual, cumulative progress. Continuous improvement fundamentally values change.
Compare continuous improvement’s emphasis on change to the values implicit in compliance. More than anything, compliance requires understanding a set of rules or external guidelines and designing production systems to meet their specifications. When a production system is finally approved—a process that can take years—the focus changes to executing without deviation. If nonconformances do occur, manufacturers have clearly outlined CAPA procedures. With the FDA’s recent shift from a compliance culture to a quality culture, standards for documentation have only increased. Most manufacturers facing strict regulation privilege following a clearly prescribed system over incremental improvement. In short, compliance is about consistency, about adhering to a script.
In rehearsing these concepts, I hope I’ve done more than highlight an obvious difference. I mean to show that, under the surface, compliance and continuous improvement evince fundamentally different values: change vs. consistency. Progress vs. stasis. Risk ready vs. risk averse. Frame it how you will, but there are good reasons manufacturers find themselves on one or the other side of the divide.
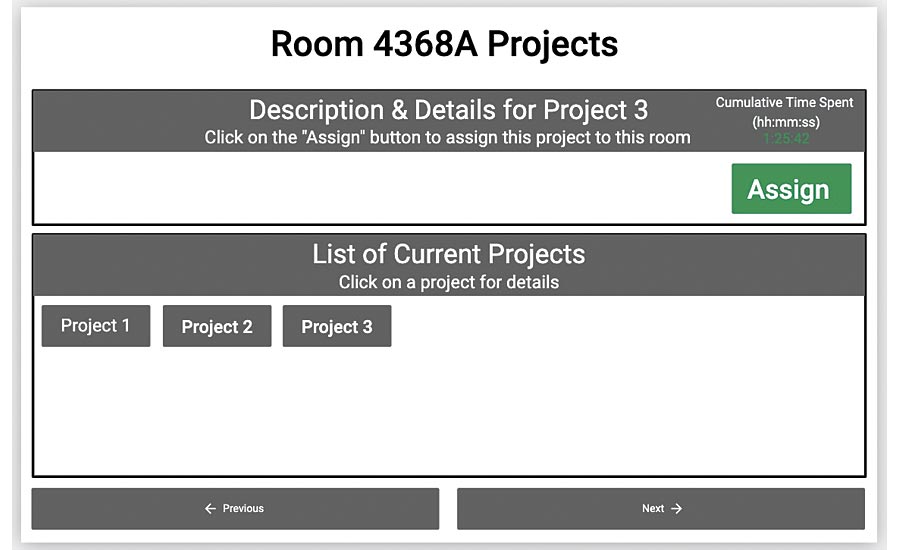
This app lets a coordinator assign projects to room based on availability.
Continuously Improving in Compliant Contexts
In order to show why there needn’t be a tradeoff, I want to share how several innovative manufacturers are balancing compliance and continuous improvement in their operations.
Consider one of the most heavily regulated manufacturing contexts: the pharmaceutical production facility. Manufacturing takes place in segregated clean rooms, creating barriers to personal communication. Frequent cleaning and validation procedures are difficult to coordinate. And the FDA’s Title 21 CFR Part 11 outlines strict criteria under which electronic records and signatures are considered acceptable, so paper-based documentation is still common. Nevertheless, manufacturers in such contexts face the same challenges as those with less oversight. Bottlenecks still hurt production schedules. Process visibility is essential to process improvement. And data is necessary to understand which steps might slow production.
So how do you implement a continuous improvement program in this environment?
This was precisely the challenge facing a consultant I worked with recently, who preferred to remain anonymous. His task was to run a multi-room production facility more effectively while remaining compliant with FDA guidelines. Many of the sources of inefficiency and low-visibility were a result of the facility’s reliance on paper. While the paper logs used throughout the client’s operation were sufficient to demonstrate compliance, they weren’t providing enough information to guide improvement efforts. As the consultant noted, “We scan all our paper logs into a computer for regulatory purposes, but it’s difficult to use for continuous improvement since the data cannot be easily analyzed and times are not tracked.”
The consultant’s solution was to develop manufacturing applications using a no code digital platform to track the status of production rooms. Rather than using traditional visual indicators such as colored magnets, this consultant is creating apps that let team members track progress in each room in real time. Their entries will be stored automatically and available immediately. When rooms are ready for cleaning or validation, the app will send a signal notifying the appropriate team they are needed.
This system allows this consultant’s client to have the best of both worlds. Because the apps and databases run in parallel to prescribed compliance requirements, the manufacturer can continue to improve and refine their processes without needing to recertify the entire production process. The consultant summarized, “Team members will continue to write in the logbooks in each room in order to comply with FDA standards. However, since the apps running on the iPads are simply used for operational efficiency, they do not need to comply with 21 CFR part 11 guidelines.”
For other manufacturers, balancing continuous improvement and compliance means turning attention to the human element in their operations. Much of the burden of compliance comes from ensuring employees are trained sufficiently to execute their responsibilities to the letter. Where complex lab equipment and complicated paper SOPs are involved, this is no trivial task. For global life sciences company Merck, balancing continuous improvement and compliance took the form of digital work instructions. Using a manufacturing app platform, Merck designed IoT enabled training modules to guide operators through complex processes while documenting their progress. The app automatically documented operator performance, so mentors were able to track progress and give targeted feedback to their trainees. In this instance, finding an opportunity for continuous improvement in a highly regulated environment meant empowering team members to excel in their work. Improving training times also improved Merck’s ability to adhere to regulations.
So what do each of these examples have in common? In each, the pursuit of continuous improvement did nothing to hinder compliance. In Merck’s case, finding an opportunity for continuous improvement—training—naturally improved their ability to meet regulatory standards. And because these process improvements occurred in parallel to a QMS, they allowed the manufacturers flexibility even under strictly monitored conditions.
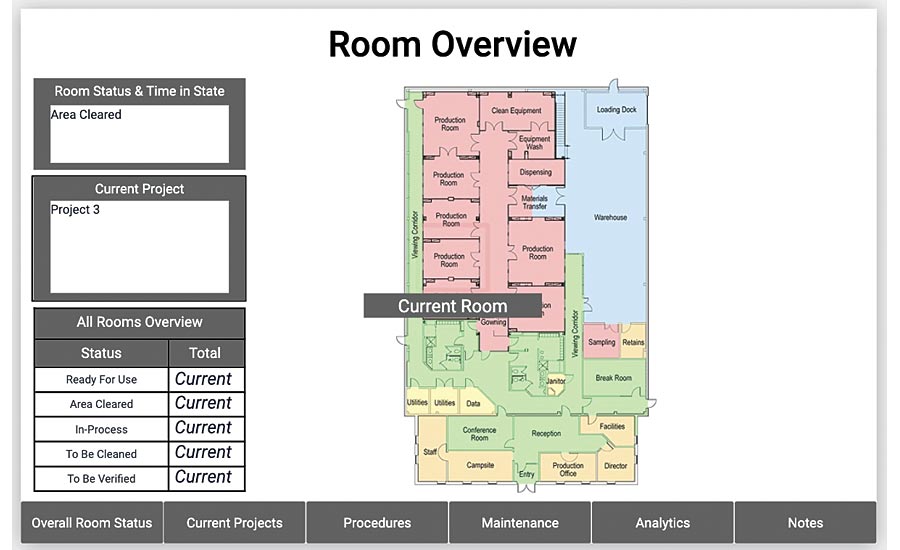
A no code database tracks status of all projects and rooms. From this screen, an engineer has full visibility into production.
Looking Forward: Making Compliance a Seamless Part of Manufacturing
As new requirements for demonstrating quality—not just compliance—take hold, manufacturers will be held to an even higher standard of evidence.
The manufacturers featured in this article highlight the potential of new technologies to make compliance a seamless part of the manufacturing process. Looking forward, the same technologies in use today have the potential to make compliance a seamless part of the manufacturing process. For example, IoT enabled work instructions, like those Merck use, have the potential to act as a record that a team member performed a given action as specified. Process visibility apps can provide documentation of what processes took place when, thus creating an instant record for demonstrating compliance. So while both of these applications have obvious utility for continuous improvement, they also open the doors to automatic traceability, attributability, validation, and product genealogy.
Most importantly, however, they demonstrate that continuous improvement and compliance can be brought into sync in powerful ways.