Need convincing? Here’s a quick overview of some of the reasons why flexible gaging is a good choice.
1. Flexibility. It’s in the name. One of the primary applications for flexible gaging is to function as a gage on the shop floor. Traditionally, when complex, accurate measurements are required on the shop floor the solution is a fixture gage with sensors such as dial or digital indicators, LVDTs, etc. The indicators are set to nominal by using a perfect “master” gage. Although relatively fast and accurate, these fixture gages lack flexibility. They are typically capable of measuring only one-part configuration. Even a small change in the part or process can make the master, or even the fixture gage, obsolete.
When dimensions or processes change the measurements required, the flexible gaging can easily be re-programmed to accommodate. No masters are required. An added benefit is the ability of the flexible gaging to support an infinite number of part programs, making it perfect to support cell manufacturing with one gage for multiple operations.
2. Accuracy. Although not listed first, accuracy is the prime concern when measuring parts in process or in the lab. Flexible gaging has an accuracy spec superior to most CMMs. The metrology built into flexible gaging is outstanding. On board temperature compensation, magnetic loading of the stages and a compact measurement volume are some of the reasons that flexible gaging can produce lab accuracy on the shop floor.
3. Speed. In the modern manufacturing environment speed is very important. Faster machine processes demand faster measurements to maintain in tolerance results. Flexible gaging is significantly faster than traditional CMMs. The compact measurement volume, center driven stages, and an outstanding controller all contribute to make flexible gaging very fast, not just on longer, straight line moves, but when measuring small diameters and other features.
When setup time is taken into consideration, flexible gaging can offer significant time saving over fixture gages. Changing from one part to another is sometimes as simple as loading a new program.
4. Space. Floor space is always at a premium in the modern factory. The compact footprint of flexible gaging is often less than 50% of the footprint of a typical CMM. This allows for a close proximity to the machine process when desired. One other special capability of the flexible gaging as relates to space is the ability to build a measurement machine with one long axis. This is particularly valuable with long parts such as hydraulic rams, broaches, lead screws, etc. For instance, a recent system sold for measuring hydraulic rams measures 6.5m in the X axis, by 300mm in Y and 300mm in Z. The CMM to measure the same part would likely measure 7m by 5m by 2m
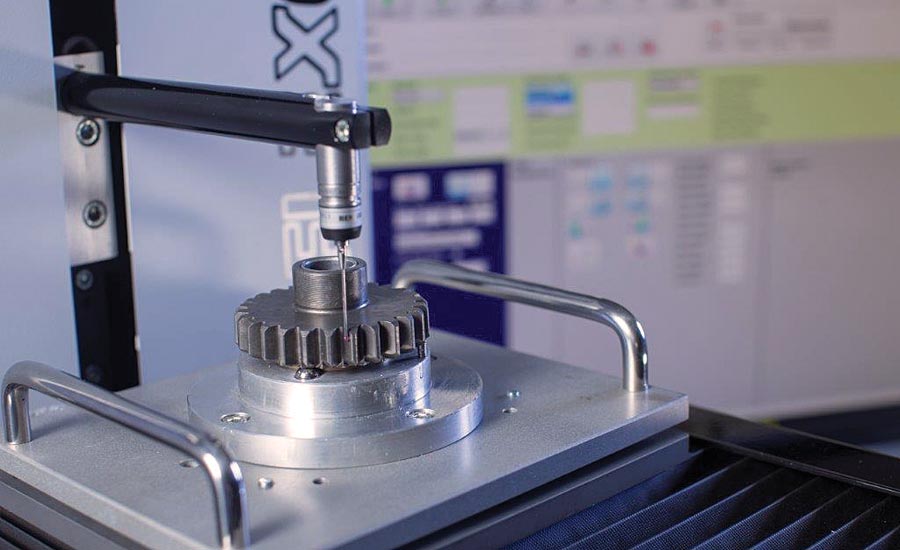
Flexible gaging can provide an alternative to the lab CMM and relieve a bottleneck without sacrificing accuracy.
5. Resource Utilization. Even more critical than space is the utilization of critical equipment. Often a CMM or multiple CMMs carry the measurement load, and are typically placed in the lab. The CMM is also often a bottleneck for measurements. Although accurate, they tend to be slow and require a controlled environment, making them less accessible to the shop floor. Flexible gaging can provide an alternative to the lab CMM and relieve a bottleneck without sacrificing accuracy, and possibly providing faster measurements at the process location.