We tend to take cardboard packaging for granted, despite its increasing importance in our everyday lives. With the advent of online shopping, more and more of our purchases are shipped to our homes inside cardboard boxes of all shapes and sizes. Despite the simplicity of this packaging, we expect that our purchases will arrive at our doorsteps completely intact and operational. For this reason, cardboard box manufacturers invest in material testing equipment to evaluate several properties relating to the strength and durability of their products.
Online retailers source their boxes from multiple global companies with the expectation that the product quality will be consistent and dependable across vendors. It is critical that packaging meet these expectations; the sheer volume of packages being sent by these companies means that even a 0.01% failure rate could result in tens of millions of dollars in lost sales due to returns. Considering the massive scale of the corrugated cardboard industry, great emphasis is placed on product quality and conformance testing. Most of this testing is performed on universal testing machines that apply compressive forces to specimens in order to obtain a complete mechanical profile of the material or finished product. Ultimately, there is low opportunity for differentiation among the largest manufacturers, meaning product quality is the key to business growth.
When developing a set of test protocols for corrugated cardboard material as well as fully-assembled boxes, it is important to fully understand the external forces experienced by these products in real-world usage. During the journey from the manufacturer to the distribution center to your home, a box needs to withstand the following potential hazards:
- Crushing. Not only do boxes need to endure the weight of their own contents, they also need to endure the weight of other boxes stacked on top of them during transit. The walls of the box experience the highest stress conditions and must be adequately stiff to prevent buckling.
- Piercing. The box walls may also be subjected to various sharp objects and surfaces. Their ability to resist piercing will keep the contents of the box protected.
- Bursting. Bursting occurs when a piercing force is spread out over a large area. This type of failure is usually caused by overloading the box past its rated weight capacity.
- Dragging & Abrasion. Heavy boxes are often pushed along the floor by package handlers, which can damage the box or even cause it to rupture. Looking past the durability of the package outer layer, the coefficient of friction is also important in understanding whether or not stacked boxes will slide off one another, damaging the contents.
- Water Resistance. As most of us know from firsthand experience, the strength of a cardboard box will deteriorate rapidly after it makes contact with water. There are many tests designed to determine the exact quantitative reduction in strength after a box has become wet.
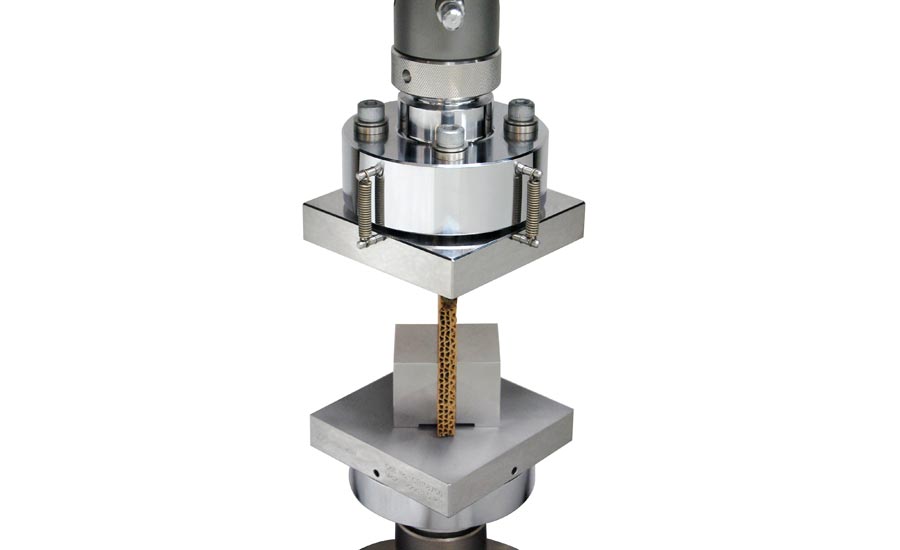
This is an example of an Edge Crush Test (ECT) setup in accordance with TAPPI T811. The guide blocks on either side of the specimen prevent any buckling from occurring.
Tests to evaluate each of these properties have been incorporated into a stringent quality control program for the manufacturers of corrugated cardboard products. The two most popular tests are the Mullen Burst Test or the Edge Crush Test (ECT). All manufacturing companies will test to either or both of these standards and mark their boxes with one of the below labels specifying the box’s rating. The Burst test is more indicative of a box’s ability to withstand excessive internal loading, while the ECT test is more indicative of a box’s ability to withstand forces associated with stacking.
In order to ensure consistency in these specifications across different manufacturers, testing standards organizations develop qualified methods to be followed when evaluating these different parameters. These organizations often include industry experts who understand and acknowledge the challenges facing both manufacturers and consumers. The two largest standard organizations in the corrugated cardboard and packaging industries are International Organization for Standardization (ISO) and Technical Association of the Pulp and Paper Industry (TAPPI). Their international reach has enabled global standardization of test methods and testing fixtures. The standardization also allows material testing companies to offer specialized equipment compliant to these standards and catered to the needs of cardboard manufacturers.
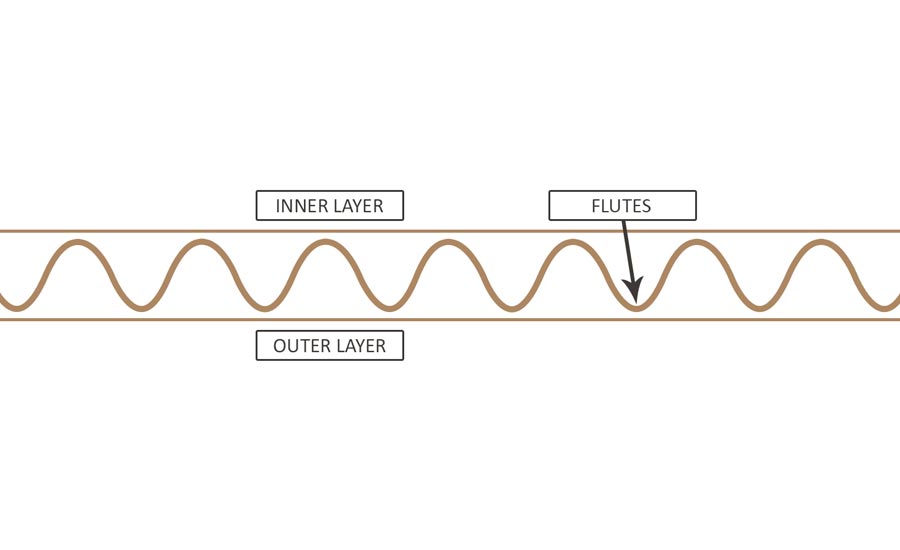
The above diagram indicates the structural break down of a cardboard wall. Each part contributes to the overall box integrity.
In order to meet these standards, box manufacturers must carefully consider their design options. Packaging engineers must make many choices including the grade of corrugated board, box closure design, flute size and direction, and inner supports. Their design parameters will also be influenced by the end use of the box, whether it be home delivery or industrial use.
The overall structure of a cardboard box can be defined by three sections: the outer and inner liner, which are both types of cardboard paper, and the flutes, which are sandwiched in between the layer and provide the box with structure and strength.
The flute design is the main driver for ECT strength, while the two liners are the drivers for Mullen Burst strength testing. Most boxes for commercial use will have single walls, but boxes destined for industrial use tend to have double or triple walls to increase their strength.
Crushing is the most common mode of failure for boxes, and more importantly the most common cause of damage to the contents of a box. Resistance to crushing is evaluated by performing the ECT test on a universal testing machine using compressive forces. The major challenge associated with this testing is the need for extreme parallelism between the compression platens. This can be accomplished by using guide columns connecting the upper and lower platens, which prevents any sort of bending movement of the platens and directs all applied compressive load directly to the test specimen. The guide columns will also integrate linear bearings to prevent any unwanted friction and maintain accurate load readings.
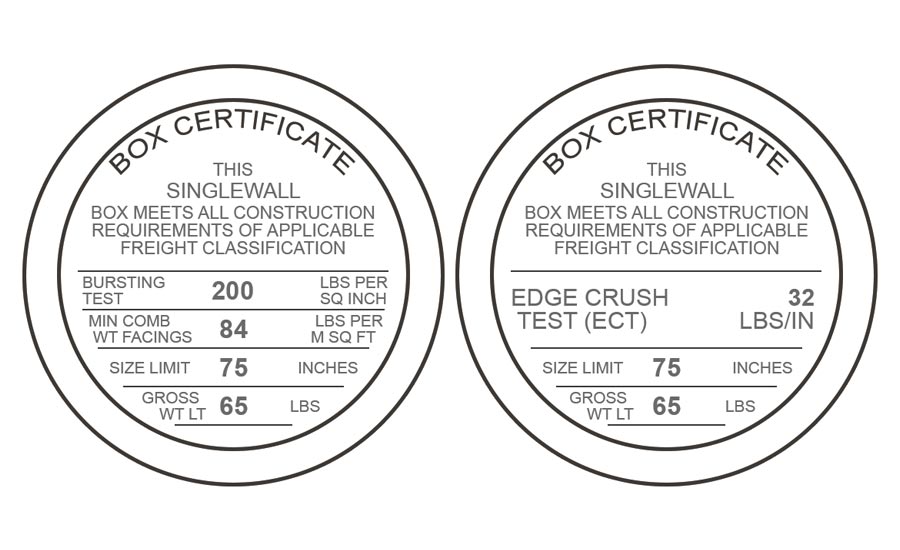
As part of a required quality control program all boxes come labeled with the above stamps, indicating either their Mullen Burst or ECT results as well as additional specifications.
Simply testing the wall material in compression does not give a complete picture of the structural integrity of the box, nor does it evaluate the box closure design. To better simulate real world usage, a full box compression test is often performed to compensate for variations due to the construction of the box. Box size is generally the most challenging factor in performing this testing, so any supplier of universal testing machines must be able to provide flexible solutions including extra wide machines and oversized compression platens. When working with extra wide or tall machines, the overall system stiffness is important to ensure the aligned loading of the boxes as well as accurate crosshead displacement readings.
With economic globalization growing at a staggering pace and online shopping taking over retail, there has been an exponential increase in the consumption of corrugated cardboard products. Global companies recognize the importance of packaging integrity and how its reliability can have a large impact on their bottom line. Establishing a robust quality control department, equipped with the proper compression testing equipment, is integral for manufacturers seeking to deliver exceptional product consistency and performance. Furthermore, the international standards organizations give companies the tools to properly evaluate and benchmark the quality of their products, resulting in low failure rates and greater market share.