Nondestructive testing (NDT) encompasses a variety of test and inspection procedures that are used to find defects or inconsistencies in test samples without compromising the integrity of the parts.
The field has advanced rapidly in recent years, with the proliferation of more testing methods and other technological innovations that have enhanced accuracy, increased efficiency and throughput, and improved upon the amount of information that can be acquired in a single test, says Dave Nelson, president of Nel PreTech Corp.
Because the design and manufacturing fields need to get product to market faster and better, they continuously drive improvements in NDT testing, Nelson says.
Nel PreTech provides CT scanning services, using X-rays to scan and build 3D, digital models of entire components. Its focus on NDT services keeps it on the cutting edge of new advances, Nelson says, and so the company is able to do more with less—which most customers demand, he says.
“With CT scanning in particular, we can unlock the potential of a single scan by offering multiple services once the 3D data set is acquired,” Nelson says. “We can offer nondestructive metrology, part to CAD design comparisons, porosity analysis [and] finite element analysis,” among other services.
In addition to NDT metrology, part-to-CAD design comparisons, and porosity analysis, the company can also detect mold flow patterns, look for defects, analyze density or material thickness patterns, find leak paths or perform reverse engineering in hours. This used to take NDT labs days or even weeks, and previously required multiple tests, samples and operations with older technology.
Full body inspections are all the rage right now, which encompass methods such as computed tomography and resonant acoustic method (NDT-RAM), says Gregory Weaver, president, Weaver NDT.
“These methods can provide critical information about the total part, Weaver says. “CT provides an image of a component’s total geometry and a 3D view of the entire product. NDT-RAM provides an overall full body response of a component. This response is a combination of the geometry, material properties, and the overall structural integrity of the sample.”
Testing systems are becoming faster and cheaper as the demand increases, says Weaver.
The increased availability, maturity, and ease of use of NDT equipment, such as X-ray diffraction (XRD) and resonance acoustic method (NDT-RAM) have provided additional NDT methods for labs to use for collecting key material information without having to damage parts, says Weaver.
“XRD is allowing labs to collect details about a material’s atomic and molecular structure and NDT-RAM is providing labs a method for understanding the internal and external metallurgical consistency of a given product,” Weaver says.
Ultimately this is good for manufacturers’ bottom lines.
“If we can fully understand the lab samples using NDT methods, then we can help to reduce the burden of destructive testing and save those components so they can be sold,” Weaver says.
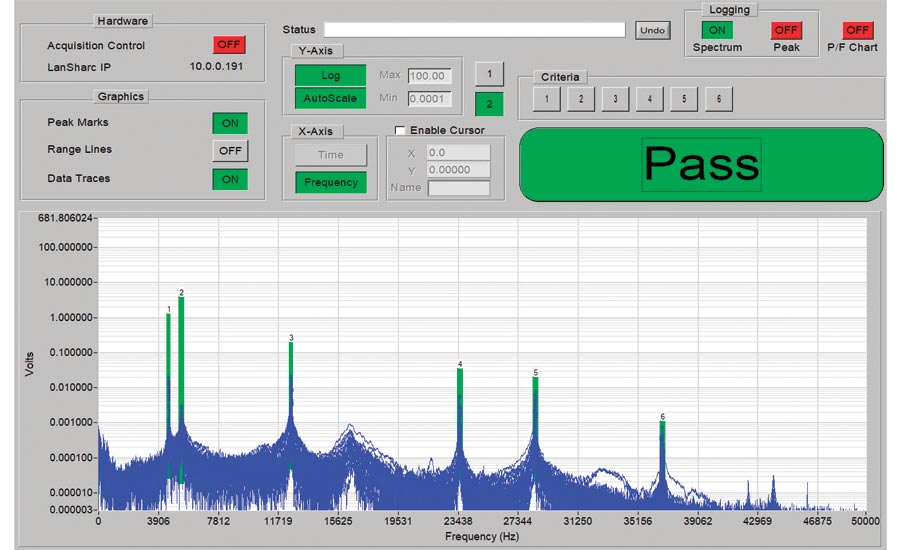
The NDT-RAM software interface, which is used in validating a sample’s overall geometry, material properties and structural integrity.
More demand for NDT
The demand for NDT services is growing, necessitating more services, says Scott Bucholz, senior vice president at Magna Chek Inc.
“More companies are starting up, basing themselves from home and doing all remote work,” Bucholz says. “More schools are offering training than 10 years ago. Moreover, with the change and new techniques, larger marketplaces that were not previously available [are popping up]. The industry as a whole has seen unprecedented growth and thus far shows no signs of slowing down.”
Toni Bailey, owner, TB3, NDT Consulting, sees the same pattern.
“Everyone that I talk to is extremely busy,” she says.
As technology evolves, older, traditional NDT methods are being replaced, while new tools such as automated ultrasonics and digital radiography (DRT), which utilizes digital detector arrays, take the stage, Bailey says.
Bailey, an NDT Level III consultant and NDT classroom instructor, has found that her customers most need digital radiography training, and technicians transitioning from film techniques to non-film techniques need hands-on experience.
“Middle-aged inspectors are struggling with the implementation of computer technology into their daily tasks and it [can be] a frustrating transition,” Bailey says. “Younger inspectors are typically excellent with the technology, but they lack basic NDT education and [also] lack the desire to maintain quality assurance.”
The skills gap hits NDT; QA suffers as a result
As other fields in the manufacturing sector have experienced, the NDT industry is struggling to retain, recruit and replace enough qualified staff.
“My customers are constantly asking me to help them find qualified and certified personnel,” Bailey says. “Companies are willing to hire trainees with no experience and this trend is a great opportunity for anyone who is seeking a solid long-term career.”
Because the pool of qualified and certified NDT technicians is lacking, companies find it difficult to balance the demands of production managers and engineers while training staff and meeting production quotas.
Quality assurance suffers for the following reasons, Bailey says:
As manufacturers grow, relationships between NDT mentors and the next generation of NDT inspectors can become strained.
Quality assurance managers are leaving the field faster than anticipated. “The departure of such experience leaves a large management-and-NDT-knowledge gap between the retiring generation and new management and NDT Level III personnel,” Bailey says.
Lastly, businesses are struggling to replace experienced staff and train the new generation while also keeping up with production demands.
All these challenges take a toll on quality assurance initiatives, she says.
Certification programs fall behind
NDT testing has evolved so rapidly that training and certification programs are struggling to keep up, says Bryan Shumway, NDT Level III technician at Laboratory Testing Inc.
“As we continue to innovate, training and certification programs along with the body of knowledge are having issues adapting to the new equipment, technology, and theory behind it,” he says.
Because the adaption is slow, certification programs are under scrutiny, Shumway says.
“The most challenging part of the business is how varied and fragmented the requirements from different regulating bodies are,” he says. “Specifications from different authorities can have vastly different or even conflicting requirements. There may be different quality control checks, different certification requirements [and] different testing parameters. This divide, especially when it comes to certification of personnel, seems to only be growing, and maintaining compliance across varying specifications becomes very cumbersome.”
Additionally, much of the world is using centralized certification programs, but U.S. employer-based programs can deviate, Shumway adds. Increased specifications result in mandatory certification requirements, necessary testing for recertification, and attempts to otherwise ensure that personnel are competent.
“I believe that the industry is shifting towards more audits, oversight, quality control and third-party reviews/certifications,” he says. “The quality and integrity of examinations is recognized now more than ever as the most important thing.”