Quality control within automotive manufacturing has come a long way.
Although automotive parts suppliers use a variety of testing equipment to conduct a wide range of tests and inspections—and within specific tolerances, which warrant highly precise tools and processes—original equipment manufacturers have refined these inspection practices over the course of decades.
Integrating Industry 4.0
Smart factories, or plants that use data from connected production systems to learn and adapt to new demands, are becoming more status quo.
“It’s no longer a luxury to integrate [smart] technology into your processes,” says Brian Martensen, senior program manager, quality products and services at Automotive Industry Action Group (AIAG).
Martensen recalls a recent visit to a spring manufacturer’s site, with impressive smart intelligence product testing and inspection systems. At the facility, he noticed that cameras analyzed each product and positioned them based on their adherence to standards. Machines received feedback seamlessly. Data was recorded and analyzed so trends could be spotted, which enabled machines to make necessary process adjustments and predictively maintain its equipment.
“These technology integrations were performed in-house, and this team continues to embrace the possibilities for their talent and their processes,” Martensen said.
Such integrated intelligence systems are making significant advancements, says Scott Lukomski, sales director, metrology North America, Jenoptik.
“These approaches tie engineering, manufacturing, and quality together so that a more holistic picture can be seen,” he said. “Industry 4.0, where the Internet of Things is employed in manufacturing, is now becoming a reality.”
Consistency is key
Quality inspection companies ensure that test results are consistent across their automotive customer base by using measurement system analysis (MSA) methodologies. MSA studies can be used in destructive and nondestructive testing equipment, to verify repeatable and reproducible test results and to guarantee consistent test methods and testing environments, Martensen says.
The automotive quality testing industry has singularly embraced MSA methodologies on a large scale to provide consistent and high-quality testing throughout the industry, he added. According to Martensen, automotive quality professionals are able to quickly review MSA data and determine if the testing equipment is of sufficient repeatability.
Measurement system analysis incorporates precise tools to regulate measurement variation and is an objective way to test the validity of a measurement system and ultimately reduce process variation, AIAG said.
AIAG, a nonprofit association of automotive companies, has published several manuals on the subject.
Because automotive parts-testing spans a wide range of products, production technologies and testing requirements, achieving consistency can be somewhat of an art.
“Due to the great diversity across automotive quality testing we don’t see the same application often,” said Konstantin Menzel of Olympus Scientific Solutions EMEA.
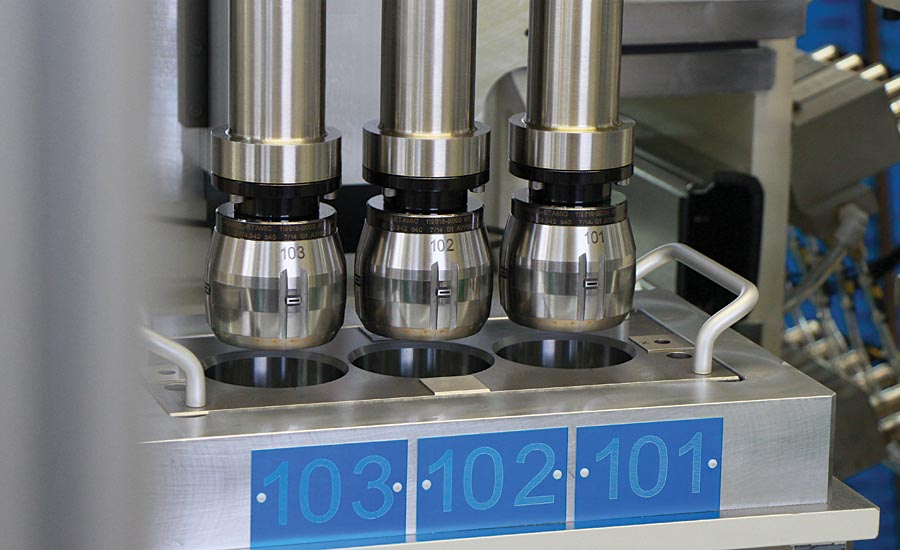
Inline air gaging for internal combustion engine blocks. Source: Jenoptik
Traceability efforts
In the automotive sector, traceability—which allows automotive manufacturers to gauge how suppliers’ engineering processes perform—is a prerequisite for certain quality standards, such as DO178C, ISO 26262, and IEC61508. The guidelines require the verification of critical safety requirements, which must be proven through such traceability.
Jenoptik has its own American Association for Laboratory Accredited lab, which is certified to the ISO 17025 standard. Lukomski said this gives Jenoptik an advantage when it comes to traceability efforts.
“We know that gages and measurement results are consistent across the years and even decades,” he said.
Testing electric vehicles
Electric vehicles are becoming more popular and widely produced. Although electric motors have existed for decades and use well-established testing procedures, the high-capacity batteries electric cars utilize are still being developed, Menzel said.
Still, noise, vibration and harshness are a factor in testing these engines. To inspect them at production speeds, noncontact technologies such as laser triangulation and interferometry are necessary, Lukomski said.
“While neither technology is new, the demand is for more accurate systems that use these technologies,” he said.
Electric car batteries require special test methods, such as resistance-measurement of contact welds, helium leak testing of the cells and cooling channels, and surface inspection for crimps and dents of the battery cooling tray, Lukomski added.
Heavily changing markets
With electric and hybrid vehicles’ surge in popularity and a growing interest in autonomous driving, the automotive industry as a whole must navigate between developing these new concepts of mobility while continuing to maintain profitable product lines for conventionally powered vehicles, Menzel said.
This struggle trickles down to inspection and quality assurance, as the demand for flexible and modular measurement solutions grows, while “the investment in specialized solutions for conventionally powered vehicles is being questioned,” Menzel said.
Because of this, manufacturers of products such as internal combustion engines and related components are likely investigating new opportunities to adjust, as they must “cope in a heavily changing market and ready their product offering for future vehicle projects,” Menzel said.
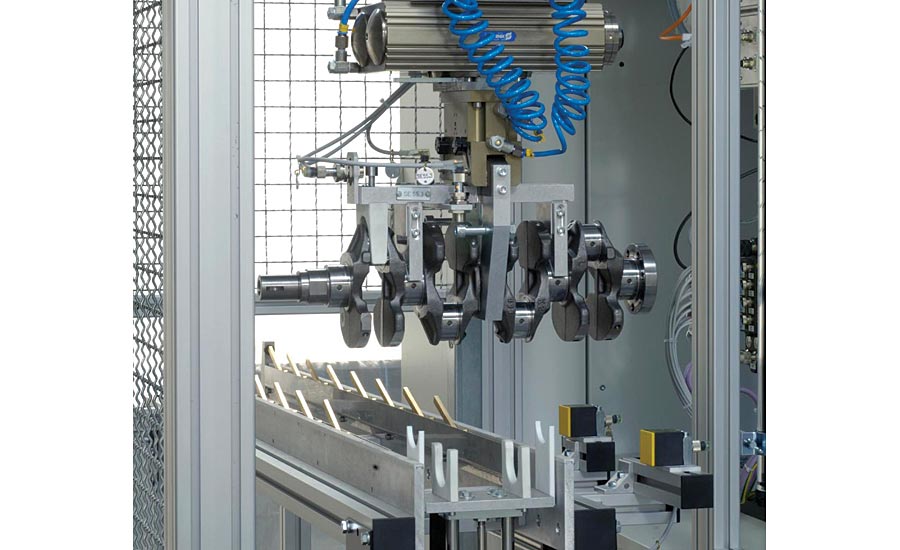
Automated dimensional metrology for crankshafts. Source: Jenoptik
Meeting consumer expectations
As automotive technologies become increasingly diverse, testing all of them can become more complex.
Additionally, automotive safety is a matter of particular public concern. As such, manufacturers can face intense scrutiny when things go wrong.
“There is continual pressure to ensure vehicles are correct the first time through,” Martensen said. “The costs, quantities and consumer exposure of warranty issues continue to increase, and the industry needs to work together to address these concerns.”
Skills in succession
This intensified pressure comes as the manufacturing industry as a whole grapples with a growing, well-known problem: the knowledge-transfer lost between generations of workers as fewer employees enter the field.
Martensen said that while many organizations develop succession plans to ensure knowledge and skills are passed on, this development doesn’t happen overnight.
This knowledge shift occurs as separate forces, such as changing consumer tastes and increased automation continue to shape the field.
Rediscovering quality
While rapidly changing global technology threatens to make some products obsolete, it also ushers in significant quality advancements, enabling quality professionals to perform calculations more rapidly and accurately than before. This allows for better, consistent data analysis.
Because of this, Martensen said, it’s an exciting time to be part of the automotive quality field, in which new waves of change are prompting quality professionals to “rediscover the foundational quality principles that were taught by quality legends like Deming and Crosby.”