Metal coatings are essential to many industrial sectors by providing enhanced surface properties to a wide variety of products. The metal coatings can provide a durable, corrosion-resistant layer to protect the base material, and help to minimize the wear and tear of metallic products. Besides, metallic coatings can improve electrical conductivity, resistance to torque, solderability, among other things. The quality control of composition and thickness of coatings is critical to ensure the correct coating properties and durability.
Different nickel-based coatings are one of the most important industrial coatings due to their durability, corrosion resistance, and aesthetics. Traditionally, electrolytic plating is the most common process used to deposit a nickel coating and it is still widely used. However, the use of an electroless nickel plating process has been increasingly used due to the improved quality and more environmentally friendly process.
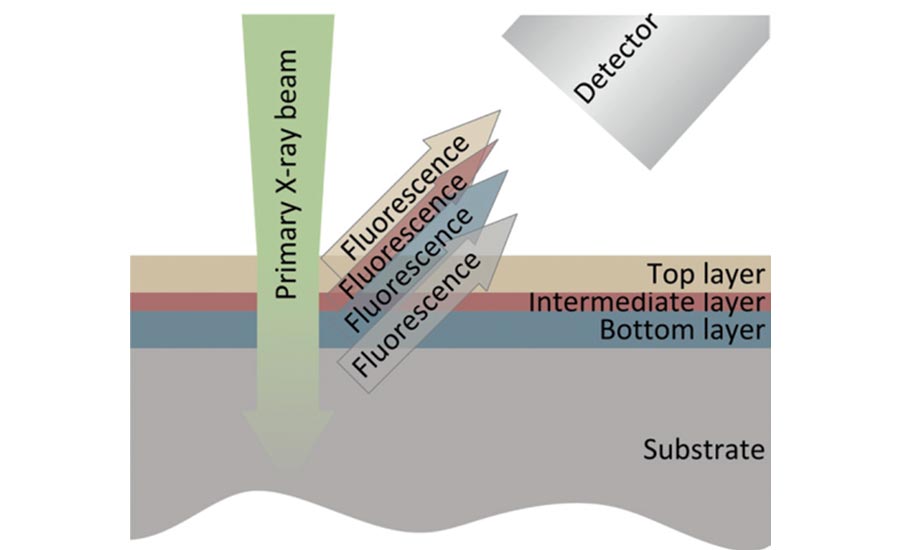
Figure 2: Principle of the XRF coating analysis
Electroless Nickel Plating
Electroless nickel plating (ENP) is an auto-catalytic chemical process used to deposit a layer of nickel-phosphorus (Ni-P) alloy coating on a substrate. The nickel-phosphorus coating thickness varies typically from 1 to 40 µm depending on the application. Electroless nickel coatings can have varying phosphorus content which impacts specific metallurgical properties. The phosphorus concentration range typically varies from 2% up to 15%. The benefit of low phosphorous nickel coating is very uniform thickness inside and outside of complex parts, whereas a higher phosphorous level offers corrosion resistance and ductility for demanding industrial use cases.
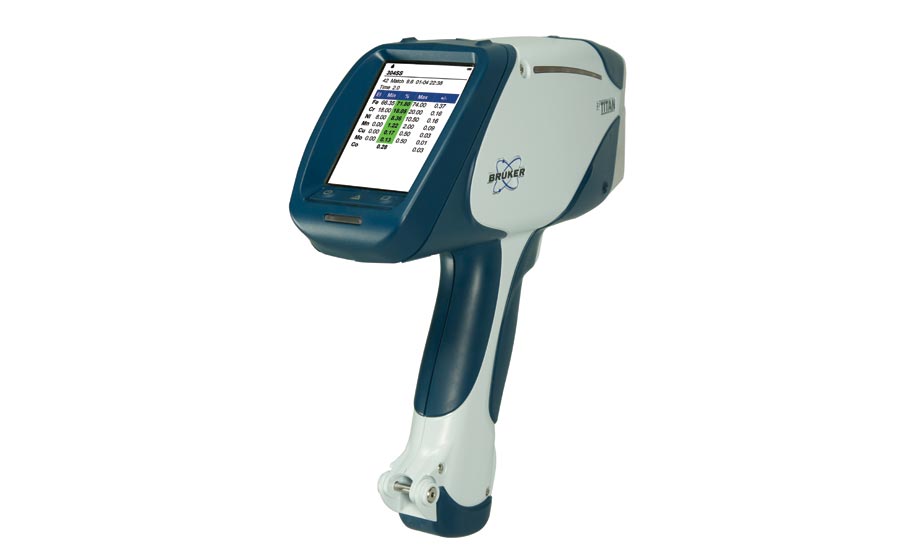
Handheld XRF
One of the key benefits of the nickel-phosphorus coating is that it provides a very consistent thickness that isn't dependent on part geometry. Electroless nickel plating can reach all hidden surfaces to offer complete coating coverage even on the most intricate parts. An additional benefit is that electroless nickel plating can be applied to both conductive and non-conductive materials, meaning it can be used also for a wide range of non-metallic substrates such as plastic, textiles, wood, and paper. Today, electroless nickel coating is used in many industries such as automotive (e.g. bearings and gear assemblies), electronics (e.g. printed circuit boards and connectors) and it continues to be adopted into new industries.
Coating thickness measurement methods
There are several different methods to measure coating thickness. The use of a small handheld coating measurement gage based on magnetic induction or eddy current method is a quick method to check the approximate coating thickness. Another more complicated technique is the assessment of coating thickness by measurement of cross section with a scanning electron microscope. However, these methods can only measure coating thickness, not coating composition which has a significant impact on the metallurgical properties of the nickel-phosphorus coating.
When tight quality control of metal coatings is required, X-ray fluorescence (XRF) analysis is often the best overall solution. The modern microspot XRF instruments can provide simultaneous coating thickness and coating composition measurement and provide a solution for many challenging coating measurement applications that other measurement methods are not able to do.
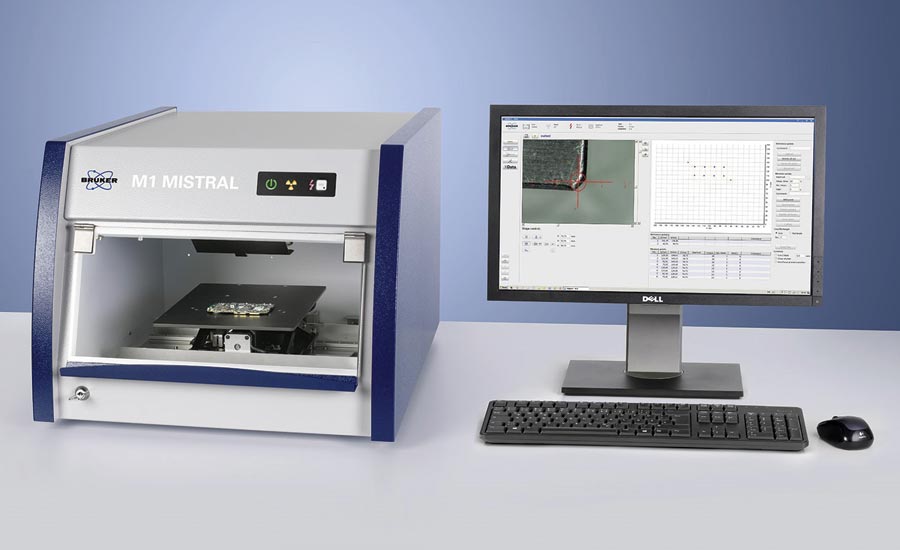
Figure 3: Benchtop microspot XRF
Microspot XRF
XRF is a nondestructive analytical technique used to determine the elemental composition of materials. XRF analyzers determine the chemistry of a sample by measuring the fluorescent X-ray emitted from a sample when it is excited by an X-ray source. Counting the number of secondary X-rays enables the XRF instrument to determine the amount of each element present in the sample. This makes it possible to determine both the coating thickness and elemental composition.
XRF instruments have been employed widely for many years to determine elemental composition and coating thickness. There is a variety of different types of XRF instruments, ranging from small handheld devices to large stationary units. The most applicable XRF instrument type for typical industrial coating applications is a benchtop microspot XRF instrument. These systems are designed to measure both large and small features and samples and can measure complex coating applications with a wide range of elements or coating layers. If the measure part is too large to fit into the benchtop XRF measurement chamber or if quick point and shoot field measurement is needed, handheld XRF is the best solution.
In addition to coating analysis, the same instrument can also measure metal alloys, plating bath liquids, plastics, and many other materials. Microspot XRF instruments also are equipped with an adjustable collimator to select an optimal measurement spot size and a programmable XYZ sample stage which allows automatic measurement of multiple pre-defined test points.
To ensure the highest level of coating measurement accuracy, it is important to choose a microspot XRF instrument that is specifically designed for this task. Important characteristics of the high-performance microspot XRF instruments are the latest SDD detector technology, optimized microfocus X-ray source, and powerful analytical software.
Microspot XRF can measure the coating thickness at any stage, starting from incoming inspection up to the final quality check. Using the XRF analysis as an integral part of the quality control program minimizes risks of non-spec products and product recalls and can improve production efficiency.
Determining electroless nickel Coating Thickness and Chemical Composition Simultaneously
The coating composition significantly influences the mechanical, corrosion resistance and magnetic properties of a nickel-phosphorus coating which makes it critical to not only measure coating thickness but also phosphorus content. Microspot XRF analysis of electroless nickel-phosphorus coating ensures complete quality control of the coating properties. It is especially critical when coatings with a different alloy of phosphorus and nickel are frequently used.
Phosphorus is a relatively challenging element to measure and requires excellent hardware and instrument calibration for precise analysis. A microspot XRF instrument is typically calibrated using certified reference standards and advanced fundamental parameters algorithm. Together with the latest hardware and electronics, excellent accuracy and repeatability can be achieved. With high-performance microspot XRF, it is possible to monitor phosphorus content with +/-0.5 wt.% accuracy and with excellent measurement repeatability, which enables tight quality control of the electroless nickel-phosphorus coating properties.
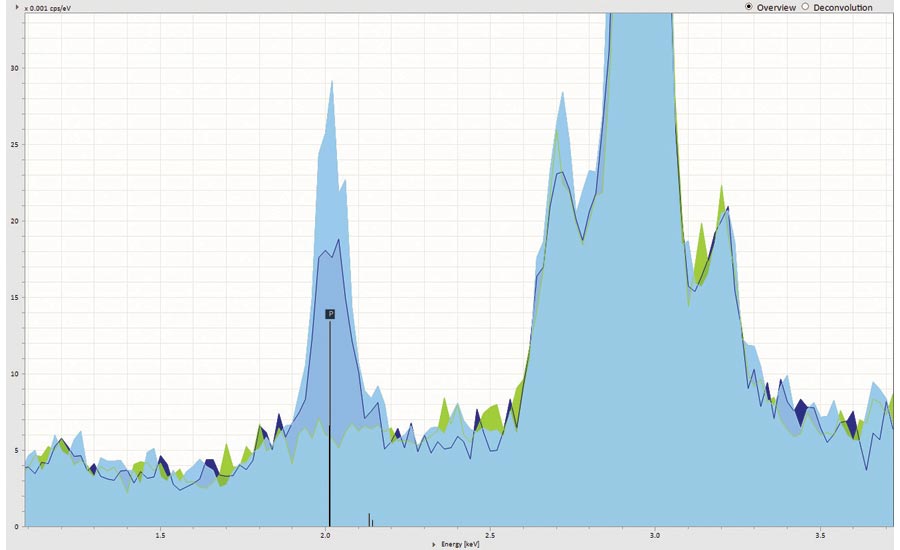
Figure 4: Overlap of 3 nickel-phosphorus coating spectra with different phosphorous content (0%, 5%, 9%)
Summary
A modern microspot XRF analyzer is a perfect tool for the quality control of metal coatings. XRF analysis enables accurate analysis of challenging alloy coatings such as electroless nickel-phosphorus which are difficult to measure with other methods. Microspot XRF is a completely nondestructive quality control method that helps to monitor production processes during all stages of the plating process and to improve process efficiency.
The microspot XRF analyzer enables the user to make quick quality control decisions, as well as parts acceptance during incoming inspection. Whenever properties of the coating are critical for product functionality, use of microspot XRF helps minimize risks of quality issues and product recalls. NDT