All the buzz these days is about laser micrometers and vision systems. If you visit a tradeshow or get any online advertisement, many companies are promoting these measuring methods. While they are both highly effective forms of measuring technology, they also have some drawbacks that still make air gaging a particularly important technology to keep in mind. The first air gages were developed in France before World War II. Let’s discuss how a technology that has been around that long measures up to today’s latest offerings.
First I’ll introduce air gaging, how it works, and its benefits, and then we can discuss how it stands up to today’s latest technology.
The first air gages were developed in France before World War II by a carburetor company for measuring its carburetor jets. This proved to be a reliable method that has continually evolved into today’s advanced technology. Air gaging works according to a law of physics that states pressure and flow are directly proportionate to clearance. When clearance decreases, air flow decreases, and air pressure increases. When clearance increases, air flow will increase, and air pressure will decrease proportionally. The pressure is determined by using an artifact, typically referred to as a setting master, of known value. Some air gaging systems use one master and some use two, but this article is not to argue the advantages/disadvantages of either type. This known value is used to plot actual diameters or other features on a scale between your upper and lower tolerance points.
The benefits of using air gaging are many. One of the biggest reasons is its relative ease of use which requires no special training, and will allow multiple operators to get similar, repeatable results. Air gaging is very economical and I do not think we talk about it enough, but the tooling cost is inexpensive when compared with other forms of measurement. It is a noncontact form of measurement, so you do not mark the part or influence thin wall parts with contact points. This also allows for measurement of non-metallic parts such as plastic and other material. This technology can be used to measure exceedingly small diameters (under 1 mm).
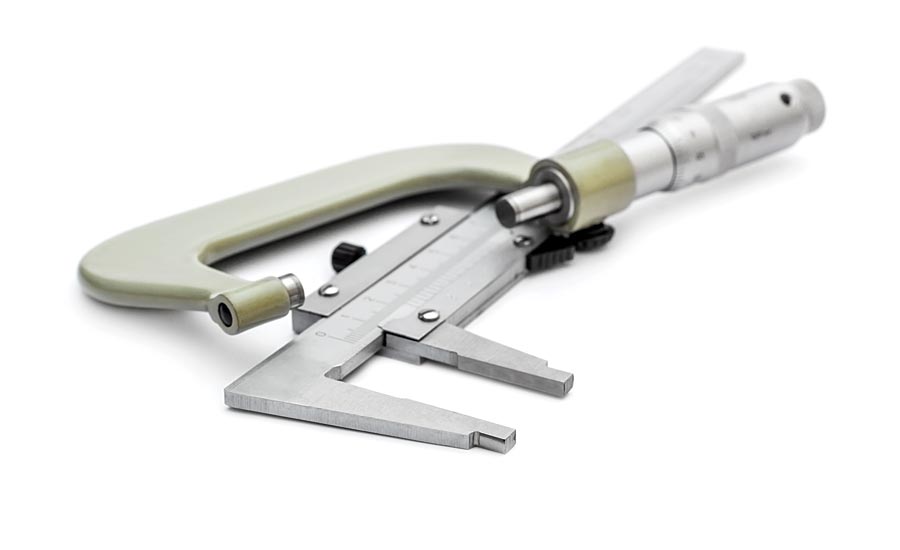
Air gaging is an extremely fast measurement method even when measuring difficult geometries. This can save a lot of money compared to the CMM time required to measure the same geometry. It is extremely accurate; in fact, it is one of the most accurate measurement systems in the world. Because it uses air for measurement, it has a built-in cleaning effect to dissipate any coolant or cutting fluid. It relies on a simple principle that has no moving parts and therefor the life of the product is exceptionally long.
Air gaging can be used to measure diameters, both inside and out, taper, perpendicularity, parallelism, out of round, lobing, straightness, flatness, matching, angle in either decimal degrees or degrees, minutes, seconds, and other geometrical tolerances.
Laser micrometers and vision systems offer the ability to measure a wide range of parts, diameters, and tolerances, there are still some vulnerable issues such as lighting, which is the biggest factor in how successful you will be with a vision system, shiny parts, coolant or oil on parts and other issues that require some level of expertise from the operator to minimize these negative effects.
Air gaging is made specifically for the application requested so it does not have the wide range that comes with those other technologies, but it is still the fastest and most reliable measurement method in the industry for the specific task at hand. There are also some features that cannot be measured using vision or lasers. An example that comes to mind is a small, tight tolerance bore. A laser cannot measure this, and a vision system is extremely limited depending on the depth of the bore. The vision system is also limited to pixel size for repeatability. The higher the resolution of the camera, the more expensive the system is. Air gaging repeats in the submicron level (0.0002 mm or 0.000008”). Because the air gage is designed specifically for the application, measurement is completed in seconds, is repeatable, reproducible, and easy for an operator to manage.
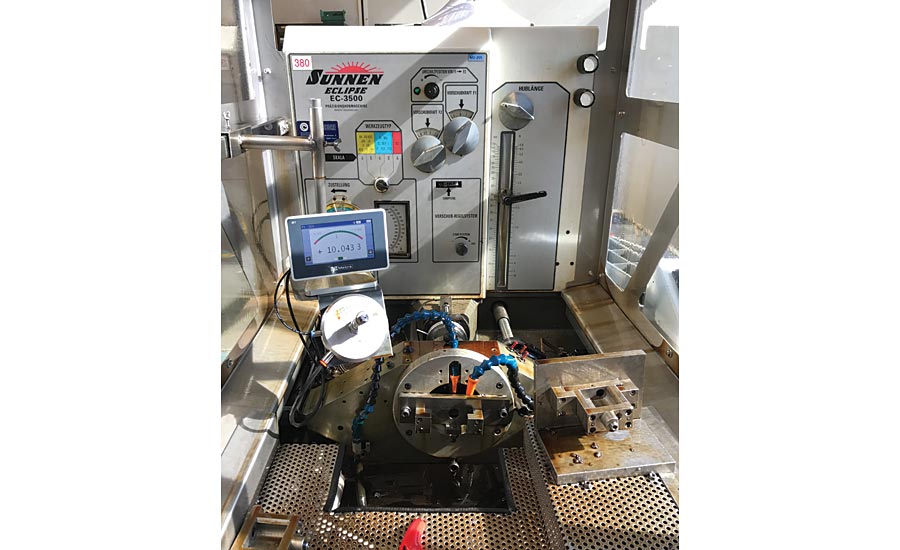
The tooling in air gaging systems has not really changed a lot since those early days with the exception of smaller and smaller sizes. Air gaging systems have evolved on the display side to become a critical component in today’s 100% inspection world. Systems can become an integral part of the manufacturing cell by keeping track of serial numbers, lot numbers, or other important criteria and then sending offset values back to the machine to keep the manufacturing process on track and reducing scrap. The systems can seamlessly integrate with robots and PLCs to require minimal human interaction and offer lights out production to increase profitability and throughput. Some of the communication protocols available today include RS232, Digital I/O (24 Volt DC), USB, Ethernet IP, Ethernet TCP/IP and Profibus. With all the communication protocols available, it will easily integrate into your manufacturing cell. Although the technology is very old, air gaging has found a way to stay a relevant metrology option in today’s demanding world. Make sure to keep air gaging in mind on your next application! Q