Due to rising labor costs and a shortage of skilled inspectors, today’s manufacturers are facing intense pressure to automate processes that rely on the senses of experienced human workers. Visual inspection is one of the areas that continues to make use of human sensibility to a large extent. This sort of work requires extensive experience, particularly when defects can be subtle and tricky to spot.
Today’s emphasis on flexible production only adds to the challenge. Since products coming down the line can vary in color, shape and size, a characteristic that is considered a defect on one item might be considered acceptable for a different product. Efforts to automate visual inspection must account for these variations and the impact they may have on the algorithms’ ability to “learn” what a defect looks like.
Fortunately, powerful new artificial intelligence (AI) technology has demonstrated an ability to match the skills and capabilities of experienced inspectors. Scratches and blemishes that were once difficult for automated systems to capture can now be identified even without the use of samples or adjustment. AI-based image filters are capable of identifying defects on any product background, thereby supporting flexibility on automated production lines.
The challenges of using conventional image processing technology
Characteristics that result in image variation—such as appearance, lighting, surface, deviation from center, and the like—tend to confuse conventional image processing technology. Selection of a feature value and threshold adjustment in these systems requires expert-level image processing knowledge, and even then, the tasks are quite time-consuming because they involve a continuing process of trial and error. The steps in this process are as follows:
- Setting up the inspection area to match the shape of the object to be inspected
- Selecting a feature value for each area
- Setting a threshold level for each feature
- Judging whether a product is defective or not
Some conventional systems have tools that use a type of machine learning technology called a neural network. These tools include optical character recognition (OCR), optical character verification (OCV), and pattern matching tools. These tools can work quite well on noisy backgrounds featuring color and pattern variations. However, many inspection applications require a broader range of capabilities.
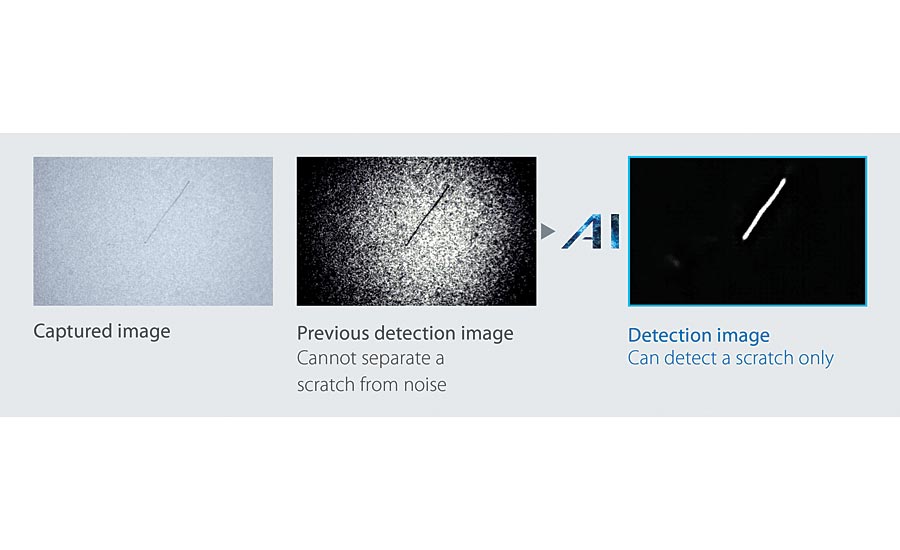
To reliably detect scratches, a vision system must be able to distinguish the actual defect from noise or other patterns on the product surface.
Pre-trained AI tools reproduce human expertise through learned criteria
Accepting variances is challenging for conventional, rule-based systems, and this is where artificial intelligence comes in. To successfully capture defects—like scratches—on any background, advanced AI algorithms must first train on a series of images that each contain either a flawed product or a good product in order to determine which specific characteristics separate the two categories. Essentially, AI learns by example.
Scratch detection uses deep learning, a type of neural network with many algorithmic layers. The images supplied must be sufficient in number to solidify the algorithms’ conception of a “scratch” as much as possible. Since this isn’t always practical for the end user, automation suppliers offer pre-trained, ready-to-deploy AI-based image filters. These make it possible for systems to automatically detect scratches on any product background without samples or adjustment.
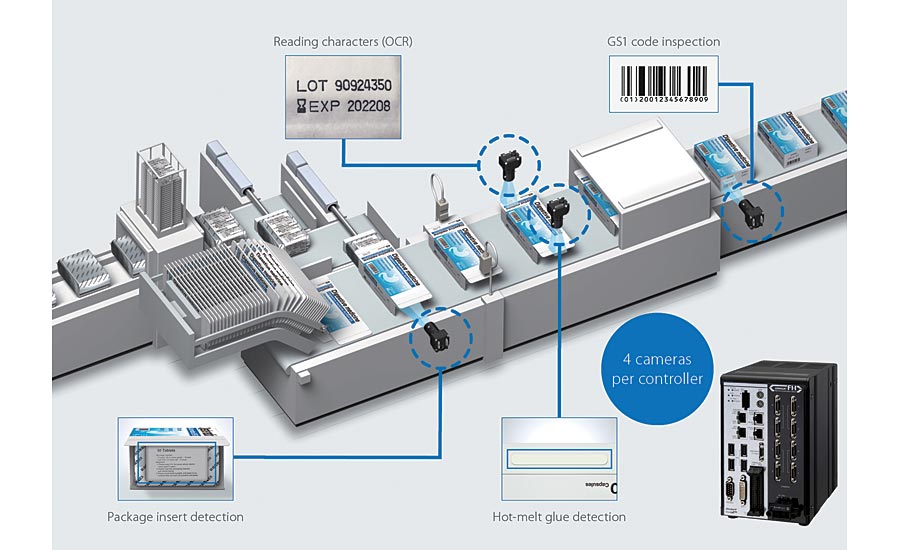
From common applications like OCR and code inspection to more complex tasks like glue application analysis, this system can take care of any inspection need with multiple cameras connected to a single controller.
The right algorithms can minimize overdetection
Pre-trained AI tools are limited to specific types of defects like scratches. Manufacturers seeking to detect other product flaws will need to actually train their AI systems. While it’s essential to strive for capturing all defects that could impact product quality, manufacturers also want to minimize false positives that could waste time and material. To get the best of both worlds, the user needs to create a product model that includes tolerable variances.
Today’s most advanced systems guide end users through the process of creating a workable AI model that properly determines acceptable variation tolerances. The vast majority of images provided should be “good” images with just a few “no-goods” to support optimization and threshold definition. By learning from the image data of non-defective products, the system quickly acquires the “expertise” that inspectors develop over the course of many years.
Every time an inspection is carried out, the algorithms reconstruct the model for what’s presumed to be a good product. Artificial intelligence then extracts a difference between the reconstructed good product image and a captured image to identify a defect. By reducing overdetection, this advanced strategy minimizes costs and boosts productivity through automation.
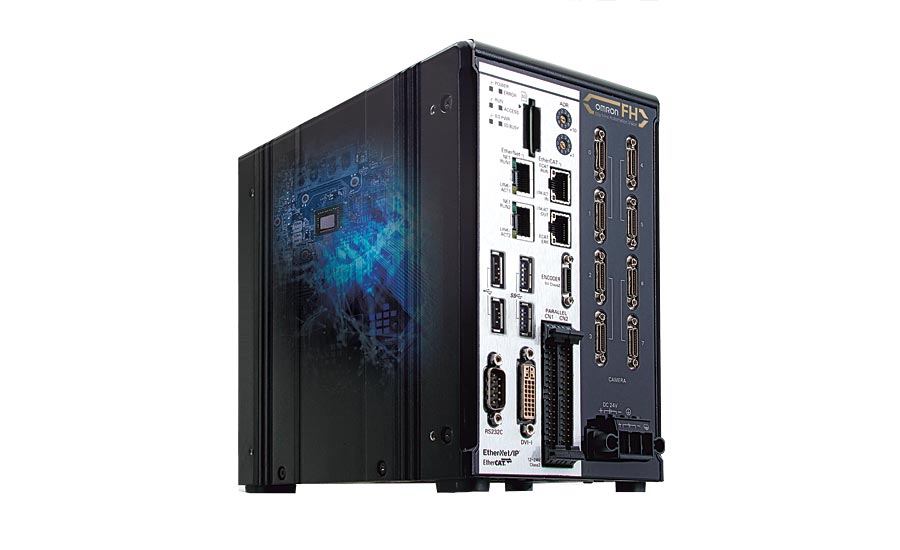
A high-speed, high-capacity controller forms part of Omron’s FH Series vision system to support powerful AI algorithms and high throughput.
An in-camera system boosts flexibility for the end user
In the majority of systems, users must create the AI model outside of the camera. However, in some systems, it’s possible to actually create and run the AI model within the camera. This is helpful because it allows users to acquire images and create the AI model within the same system without needing to switch between the camera and external PC or cloud-based system to upload the photos externally.
Having everything running within the same system allows users to reduce programming time, eliminate the need to acquire additional hardware (such as more powerful PCs) and avoid adding more complexity by deploying another non-industrial device in the manufacturing plant which requires working with additional departments like IT for such needs as PC acquisition, installation, maintenance and network configuration.
Keeping everything within a single vision system enables the same group of people within a single department to accomplish all vision inspection-related tasks. In this manner, in-camera AI contributes to a much less complex way of solving customer issues and a reduction in the time required to integrate and test additional systems.
Three ways AI helps manufacturers maximize inspection capabilities
- AI algorithms capture defects with human-like sensitivity. Scratches and blemishes that were once difficult to detect can now be identified even without the use of samples or adjustment.
- Algorithms identify good products as well as experienced inspectors. Advanced tools learn from non-defective product image data to quickly acquire the “expertise” that inspectors develop over many years.
- Pre-trained AI is accessible and easy to use. Today’s lightweight solutions feature user-friendly processing items that require no special hardware or advanced expertise.
Pre-trained AI makes AI accessible to anyone
One of the things that makes the adoption of artificial intelligence challenging is that it typically requires someone with specialized knowledge (such as a data scientist) to implement the right algorithms for a manufacturing application. With pre-trained AI, this deep expertise is no longer necessary. There’s no requirement to learn PC-level programming languages to take advantage of AI capabilities.
Today’s advanced AI systems become more intuitive by “hiding” some of the more complex parameters associated with AI implementation from the user. This dramatically simplifies the process of achieving the expected results and helps encourage the implementation of comprehensive, automated visual inspection in a broader range of manufacturing scenarios.
In summary, new developments in artificial intelligence make it so that flexible production lines are no longer a barrier to automating the time-consuming and costly process of manual quality inspections. Pre-trained AI tools can recognize defects on a wide variety of backgrounds with minimal input from the end user. By reproducing the skills and expertise of experienced visual inspectors, artificial intelligence provides an easy-to-use, fully automated solution to the current challenge of finding enough skilled inspectors to meet manufacturers’ needs. V&S