Our modern history is defined by the advent of writing. Writing is humankind’s principal technology for collecting, manipulating, storing, retrieving, communicating and disseminating information. Cave drawings gave way to hieroglyphics; stone tablets evolved into scrolls, then bound books; the invention of typeset documents gave more and more people access to the written word and today, we can send emails and text messages all around the world in a matter of seconds. Man has evolved, documentation has evolved, and with it, the way in which we manage calibration.
In the beginning, there was no way to document calibration findings other than with a pen and paper. This information was brought back from the field, entered into a form and filed away. Just as the Library of Alexandria (one of the largest and most significant libraries in the ancient world) housed thousands of papyrus scrolls, managing hundreds or thousands of paper calibration documents comes with inherent risk including misplaced, lost or damaged documents or in the case of the Alexandria library, a fire allegedly started by Julius Caesar. Additionally, a paper and pen system is labor-intensive, time consuming, prone to errors and provides little to no analysis of historical trends.
As we progress through time, more digitized systems of calibration management have emerged, including the use of spreadsheets and databases. While certainly a step in the right direction, this method of documentation still has drawbacks. Similar to pen and paper, this form of recording calibration data is still time consuming and error prone. It also lacks automation in that reminders and tasks cannot be set up on instruments that are due for calibration.
The use of software to manage calibration reports is the next giant leap. The calibration module within some maintenance management software allows instrument data to be stored and managed efficiently in the plant’s database. But again, this method falls short due to lack of automation, limited functionality and often not meeting the regulatory requirements (e.g. FDA or EPA) for managing calibration records.
Advances in technology seem to come faster and faster. Today, calibration software is the most advanced solution available to support and guide calibration management activities. With calibration software, users are provided with an easy-to-use Windows Explorer-like interface. The software manages and stores all instrument and calibration data. This includes the planning and scheduling of calibration work; analysis and optimization of calibration frequency; production of reports, certificates and labels; communication with smart calibrators; and easy integration with maintenance management systems such as SAP and Maximo. The result is a streamlined, automated calibration process, which improves quality, plant productivity, safety and efficiency.
In order to understand how this software can help better manage process plant instrument calibrations, it is important to consider the typical calibration management tasks that companies undertake. There are five main areas here, comprised of planning and decision-making, organization, execution, documentation, and analysis.
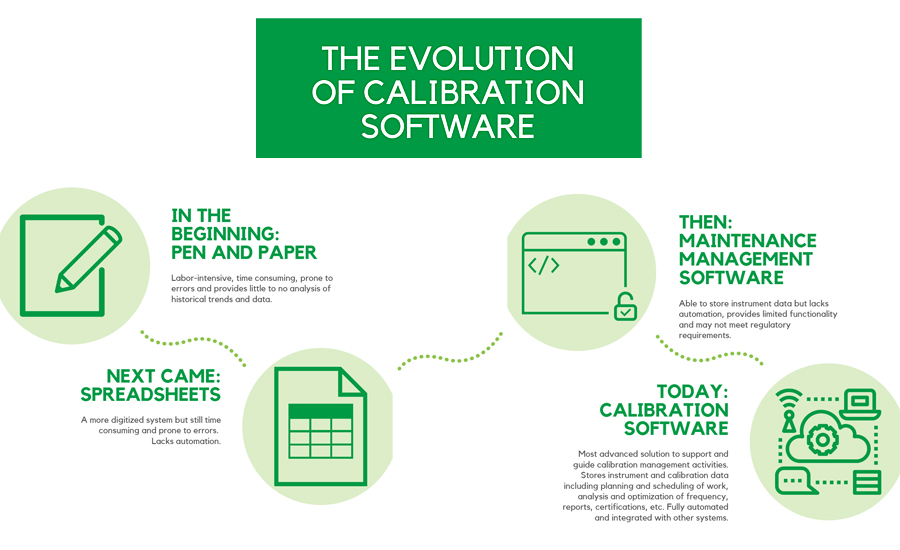
Planning and decision-making
Instruments and measurement devices should be listed and classified into ‘critical’ and ‘non-critical’ devices. For each, calibration ranges and required tolerances should be identified. The calibration interval, creation and approval of standard operating procedures (SOPs) and selection of suitable calibration methods and tools should also be defined. Finally, the current calibration status for every instrument should be identified.
Organization
The next stage, organization, involves training the company’s calibration staff in using the chosen tools and how to follow the approved SOPs. Resources should be made available and assigned to carry out the scheduled calibration tasks.
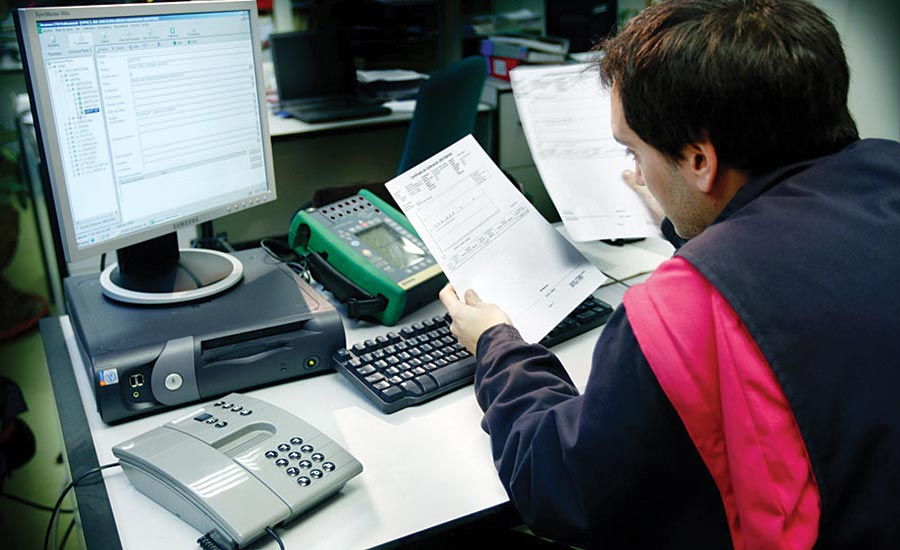
Execution
The execution stage involves staff carrying out assigned calibration actives and following the appropriate instructions before calibrating a device, including any associated safety procedures.
The documentation and storage of calibration results typically involves electronically signing or approving all calibration records generated.
Based on the results, analysis should be performed to determine if any corrective action needs to be taken. The effectiveness of calibration needs to be reviewed and calibration intervals checked. These intervals may need to be adjusted based on archived calibration history. If, for example, a sensor drifts out of its specification range, the consequences could be disastrous for the plant, resulting in costly production downtime, a safety problem or leading to batches of inferior quality goods being produced, which may then have to be scrapped.
Documentation
Unlike many of the more archaic methods that came before, calibration software generates reports automatically and all calibration data is stored in one database rather than multiple disparate systems. Calibration certificates, reports and labels can all be printed out on paper or sent in electronic format.
Analysis
Improvement in documentation leads to improvement in analysis. Using specialized calibration management software enables faster, easier and more accurate analysis of calibration records and identifying historical trends. Also, when a plant is being audited, calibration software can facilitate both the preparation and the audit itself. Locating records and verifying that the system works is effortless when compared to traditional calibration record keeping. Regulatory organizations and standards such as FDA and EPA place demanding requirements on the recording of calibration data. Calibration software has many functions that help in meeting these requirements, such as change management, audit trail and electronic signature functions.
Just as advancements in tools and the proliferation of the written word has helped shape our evolution, advancements in calibration documentation shape the efficiencies and productivity of plants utilizing these technologies. By replacing manual procedures with automated, validated processes, efficiencies should improve. Reducing labor intensive calibration activities will lessen costly production downtime and the ability to analyze calibration results will optimize calibration intervals, saving time and increasing productivity.
Every type of process plant, regardless of industry sector, can benefit from using calibration management software. Compared to traditional, paper-based systems, in-house built legacy calibration systems or calibration modules of maintenance management systems, using dedicated calibration management software results in improved quality, increased productivity and reduced costs of the entire calibration process.
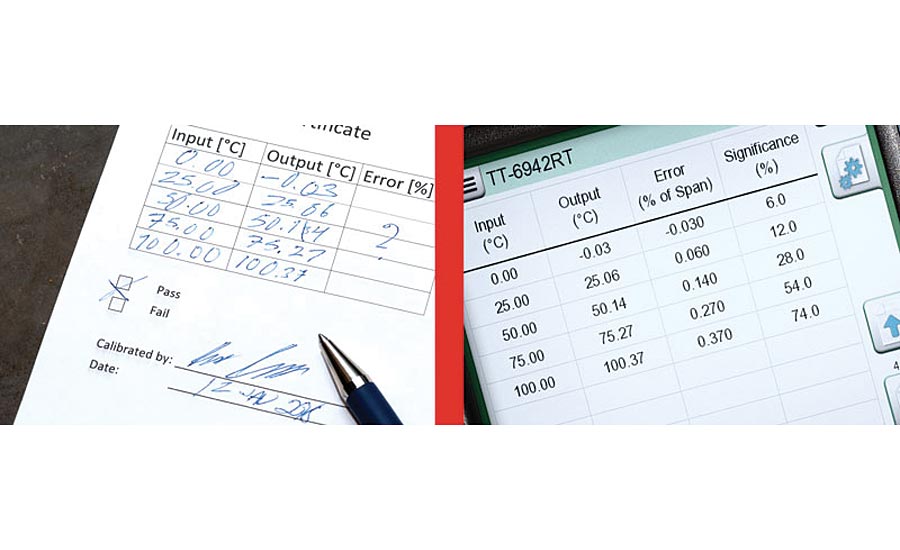
Calibration software gives users access to data and history trends. These insights help you make better decisions. For example, when a piece of equipment needs to be upgraded, it can be difficult to get approval based on speculation. Being able to show data of the inconsistences and malfunctions make the approval process much easier. In addition, as tasks for calibration technicians continue to increase, having insights into process can create a more streamlined and efficient work schedule. Therefore improving reliability, better managing technician’s workflow and creating a safer and more well-organized process.
As we become a more advanced society our need to share information progresses, as do our methods of collecting, manipulating, storing, retrieving, communicating and disseminating it. While simply writing calibration data down with pen and paper is still an effective way of collecting the information, it lacks efficiency and hinders the ability for those that come later to retrieve and process the information. Databases and maintenance management software are certainly steps in the right direction but still miss the mark when it comes to disseminating the data in a useful and streamlined way. By implementing a calibration software, information is easily collected, stored, analyzed, retrieved and shared. Until the next advancement, calibration software remains the most advanced solution available to support and guide calibration management activities. Q