Sometimes the smallest act of recognition can bring people to tears.
Even a simple printout of someone’s idea can make him or her feel validated and seen. In his long career in quality, Jim Smith recalled one employee suggestion program that involved printing up the person’s name, their idea and basic information, done on a dot-matrix printer. It was meant just for recordkeeping, but people started taking the papers home with them. One employee, who had been with the company for forty years, came up with an idea that would save the company about six thousand dollars. Later, Smith ran into him and his wife at the mall. His wife threw her arms around Jim and gave him a hug. She told him this was the first time her husband had felt appreciated at work. The man had tears in his eyes.
While it shouldn’t take 40 years for an employee to feel appreciated, continuous improvement programs can help this happen. If done right, a continuous improvement program can provide much deserved recognition along with cost savings and streamlined workflow.
Continuous improvement is a never-ending initiative. Employee suggestions are one way to accomplish this but there are many ways to go about it. Here we’ll discuss how to work on improvement programs as well as some things not to do.
Making Things Better
Done right, continuous improvement can lead to feeling pride in your work as well as better processes. Continuous improvement might take the form of a Six Sigma project, lean, Plan Do Check Act (PDCA) cycle, kaizen events, or benchmarking. Employee suggestion boxes are another method.
“There’s a lot of different versions,” says Smith, who did his master’s thesis on the subject and has written a continuous improvement study guide. “It’s whatever works for the company. It doesn’t happen by itself. Management would like to think it does. No matter where I was at, I always had the continuous improvement program; we saw that as being highly connected to the quality program. When I did my thesis, my thought was that paying for ideas was the best way to generate all the people to be involved. That proved to be false. It really comes down to people need to feel rewarded, no matter how you do that.”
Smith says he always looked at how the quality system is functioning and how healthy the continuous improvement program is.
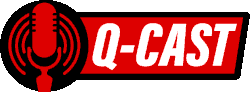
Podcast: A Career In Continuous Improvement
Jim Spichiger, past-chair of the ASQ Inspection Division and a long-time quality expert, discusses how continuous improvement projects might work, misconceptions about the process, and improvement successes from his own career.
“Not everybody does that,” Smith says. When he benchmarked his thesis, he covered about 150 companies and visited about 70. Companies often “talked a good game,” Smith says, but a visit showed a different story. Accounting or HR might be in charge of continuous improvement, for example.
“There’s no silver bullet here. If you want to engage people, it doesn’t happen automatically. If you’ve had a regressive culture, you don’t turn that around overnight,” Smith says. “It might take a lot of effort.”
And here’s a little of what not to do.
Once during a benchmarking trip, Smith saw an automotive plant with white boards in a few project areas that mentioned “heads” with a number. He wasn’t sure if this was referring to the head of an air nozzle or some other device. When he asked, management told him it was the headcount number they were looking to reduce. He was appalled and told them so. Having the audacity to list this in front of staff was no doubt demoralizing and went against everything a continuous improvement program stands for. Management should assure their staff that no one would lose their job over a continuous improvement program. They might be reassigned to another task or division, but their work is secure.
Another Way Of Doing Things
Back in the early 1980s, Smith recalled a plant that faced closure, which would put 6,000 people out of work. Management would transfer to another facility but hourly would not. Smith visited the facility, and talked to senior managers. At the time, they had only a few ideas a month coming in from the 6,000 employees. With a blackboard behind him, Smith told them, “If you implement the program” and then took the chalk and drew a line that went up almost vertically. This got their attention. “Within six months, the activity went from four to eight ideas a month to 200 or 300 a month,” he says.
“Continuous improvement is about a way of life,” Smith says. “What you have to do as a company is to encourage that culture where everybody is participating.”
Is there a better way of doing it? This was the sentence guiding their work. When people work at a job, they will naturally come up with ways to streamline and improve the process, Smith says. Another program he was involved with treated every manufacturing area as its own entity, or its own company. Every area had to track cost of quality and continuous improvement.
To determine if costs were too high, they would look at costs for the previous month and see if they were out of line and if so, what they needed to do about it. This dramatically improved things. The program also had near 100% participation from hourly workers, and eventually was expanded all over the world, including plants in China and Brazil.
Another option is a kaizen event, which might be a three to five day project where the team develops a list of what to do, with managers and in some cases even the president participating. This meant hourly employees rubbing elbows with the CEO. This can change perceptions, Smith said; by the end of the project, staff might be saying we instead of I.
Training
“As quality professionals, continuous improvement is our ultimate goal,” says Jim Spichiger, “so obviously where you would begin is with training.”
Spichiger, a former chair of the ASQ Inspection Division with more than 35 years of quality experience, says lean and problem solving overlap with each other. A continuous improvement idea may begin by considering the projects you want to address, how to go about it, and the data you might need.
One of his first projects with an early employer involved changing the company culture. Most continuous improvement projects were last-minute efforts and not very effective. He was told, “You can keep the deadlines the same, but things should be done sooner. For example, with a 90-day deadline, we would like most of the projects done within 45 days.’ He thought, “How do I change that? How do I change procrastination?”
But he was able to address this. His team walked themselves through the data, looking for root causes and potential solutions, and then were able to meet their goals. “This showed me that the methodology works and almost anything can be solved,” Spichiger says. “Major changes are possible, not only changing processes but changing thinking and culture is very possible.”
While there are many tools, they are also many areas for improvement on a manufacturing floor. “You’re always challenged with production problems,” says Spichiger. “There’s never a lack of things to do and ways to make things better.”
The way to do that is through determining the root cause of a problem—not simply following up on a hunch, which may delay finding the real issue, he notes.
For those who may not be interested in continuous improvement, Spichiger says that success is the best way to change this. After a few successful projects, even the skeptics acknowledge that these methods really work.
Spichiger recalls a previous position where the IT department was “the toughest nut to crack.” The department was skeptical and thought quality knew nothing about IT. Which was true, Spichiger says, but “we knew processes, how to work processes and how to solve problems.”
Eventually, the IT department became the biggest advocates of continuous improvement—but it took years to get to that point.
“As you grow and have more success, more people will buy into it,” Spichiger says. Eventually, the staff started doing these things on their own.
Along with training, Spichiger says continuous improvement learning goes beyond the classroom. Attending conferences and networking can provide access to a host of resources. Spichiger notes that this network has helped simplify his life and it has been satisfying to be able to help others as well.