Advanced engineering industries – including automotive, aerospace, and oil and gas – rely heavily on materials that can endure harsh conditions and withstand substantial mechanical stress. For instance, it is crucial that the alloys used to manufacture gas turbine blades are capable of resisting the strain of continuously rotating at high speeds in extreme temperatures. As a result, the metals and alloys used in these applications must adhere to strict specifications, and ensuring the accurate composition of these materials is critical for maintaining quality and preventing potential failures. Traditionally, quality control (QC) methods involved sending samples to laboratories for analysis, which was time-consuming, destructive and expensive. Fortunately, advances in technology have resulted in the development of handheld X-ray fluorescence (HHXRF) and handheld laser-induced breakdown spectroscopy (HHLIBS) analyzers that can be used for on-site analysis, enabling real-time testing and often eliminating the need for destructive sampling. This approach offers significant benefits by providing reliable, essential data to operators in a timely manner, aiding manufacturers in optimizing their QC processes and manufacturing operations with confidence and efficiency.
New technologies for elemental analysis
XRF and LIBS differ in their underlying principles and applications, but both techniques enable rapid and accurate analysis of metals and alloys in the field. In XRF, a miniaturized X-ray tube is used to irradiate the sample, stimulating the emission of element-specific radiation known as X-ray fluorescence. These X-rays are then detected and analyzed to determine the elemental composition of the sample. Advances in these technologies have revolutionized material analysis by offering compact, all-in-one tools that are truly handheld, allowing accurate in‑field measurements. Modern HHXRF instruments, weighing less than two kilograms, offer enhanced sensitivity, and can detect elements down to atomic number 12 (magnesium). They can also identify alloy grades by comparing compositions to international standards, including ASTM International, DIN and AISI.
On the other hand, LIBS uses intense laser pulses to generate a plasma on the surface of sample material, which results in each element present emitting a characteristic light signature. This light is then detected using a spectrometer to identify both the elements present and their concentrations. It is a versatile technique with advantages that include rapid analysis, high elemental sensitivity, minimally destructive analysis and the ability to analyze mostly solid samples.
Comparison of the techniques
LIBS and XRF serve as complementary techniques for solid sample analysis in metals. LIBS measures light in the visible and UV spectrums, offering exceptional sensitivity for lighter elements. It also offers superior spatial resolution – making it suitable for microanalysis – by enabling precise analysis of small areas through a focused laser beam. In contrast, XRF is ideal for detecting heavy elements and can cover larger areas – due to the divergence of the X-ray beam – making it more suitable for bulk analysis or larger sample surfaces. XRF is also entirely nondestructive and requires no sample preparation, whereas LIBS is minimally destructive – leaving a small burn (less than 1 mm) – and may require some surface cleaning or grinding to achieve optimal results.
Applications of HHXRF
The automotive and aerospace industries rely on metal coatings to improve properties such as resistance to corrosion, wear and heat. Historically, coating measurements involved destructive sampling and laboratory analysis. However, HHXRF can now measure coating thickness on site, providing quick, reliable and nondestructive analysis. This ensures coatings are consistent and within the desired thickness range, preventing manufacturing issues and potential product failures.
HHXRF is also widely used in the mining and exploration industries for on-site analysis of ore samples, allowing for real-time assessment. It accurately measures the composition of metals and alloys, enabling differentiation between similar materials such as grade 303 and 304 stainless steel. This capability proves valuable for manufacturers in verifying that received materials from suppliers align with the desired specifications (Figure 1). Furthermore, HHXRF finds common application in archaeology, where it is utilized for nondestructive elemental analysis of artifacts, providing valuable insights into their composition and origin.
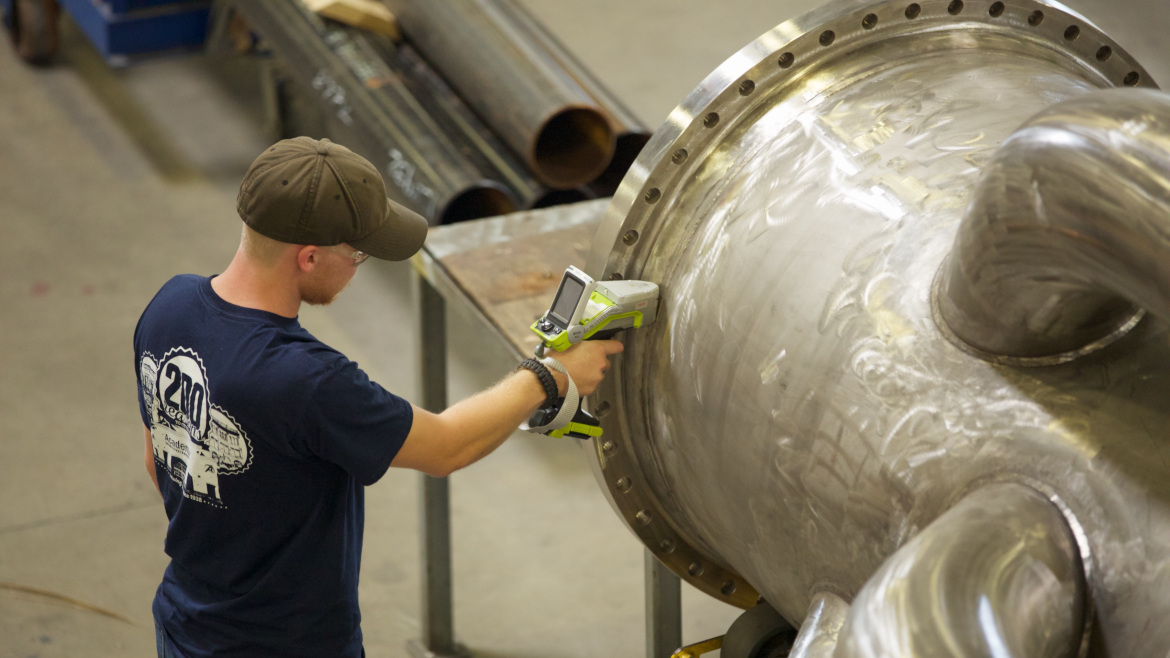
Applications of HHLIBS
HHLIBS is particularly well suited to measuring the concentration of carbon in metals and alloys. It is capable of determining equivalent carbon content (CE) – an indication of the material’s susceptibility to cold-cracking – which is crucial for evaluating material compatibility prior to welding. The CE value depends on the concentrations of carbon and other alloying elements – including silicon, chromium, vanadium, manganese, copper and molybdenum – that are also measurable using HHLIBS. In addition, HHLIBS is an effective tool to analyze stainless steel. It can differentiate between the L and H grades of 316 or 304 stainless steel, based on threshold carbon values as low as 0.03 percent.
Combined approaches
HHXRF and HHLIBS both provide rapid, precise and reliable methods for verifying material composition throughout the manufacturing process. Selecting the appropriate technology depends on the specific application and requirements for each business, as each technique has its own strengths and limitations. Factors to consider include the sample types, elements of interest, analysis goals, cost-effectiveness and regulatory compliance. By choosing the right method, manufacturers can optimize their material analysis processes and make informed decisions. For some applications, using the two methods in tandem can provide truly comprehensive material identification. The handheld nature of these analyzers is also useful for the analysis of materials in hard‑to‑reach spots, allowing the use of ladders or rope-access methods while still ensuring full analytical capability for positive identification of all types of metals and alloys.
Conclusion
HHXRF and LIBS technologies have transformed QC processes in manufacturing, providing rapid and accurate material analysis on site. These handheld instruments have brought laboratory capabilities to the production line in various industries, streamlining manufacturing processes and ensuring compliance with strict specifications. Ongoing advancements in HHXRF and LIBS – such as increased accuracy, expanded elemental detection and potential integration with artificial intelligence – promise further improvements in the future, empowering manufacturers to maintain high quality processes, reduce costs and enhance the overall efficiency in their operations.