The use of automated processes, regardless of industry or application, has become nothing out of the ordinary. The world of materials testing is no different. We find ourselves in the midst of a technological revolution that is seemingly nowhere near approaching boundaries. But how did we get here, where are we going, and is automation always optimal?
The automation of materials testing has been an evolutionary process. The task of automatically feeding standard specimens into universal testing machines has been in place for decades—at least as far back as the 1980s. In those days, this was a solution mainly confined to steel plants producing sheet metal for automotive applications, which required that each coil be tested prior to shipment. The volume of testing was large enough that even back then investments in automation were justified. In addition, studies showed that the scatter of test results was significantly reduced, an important feature when meeting tight automotive standards.
Fast forward to today and the situation is quite different. The acute shortage of labor, ever tighter testing tolerances, product liability, and data traceability and security are driving companies to look for ways to automate as much of their testing processes as possible. The questions then become, what can be automated? And what makes sense to automate?
The expansion of automation into previously unforeseen application areas has been driven by forces that would seem to be acting in contradiction to each other. For example, the handling and measurement of very small specimens (a growing segment driven by additive manufacturing) is a challenge for operators. Such specimen, with total length < 25 mm are also challenging for traditional robotic systems to handle, which however add the promise of more reliable test results. Similarly, testing of very large specimen (heavy plate or rebar, for example) presents ergonomic and safety concerns for operators running manual tests, but has also been beyond the scope of traditional automation solutions – until now.
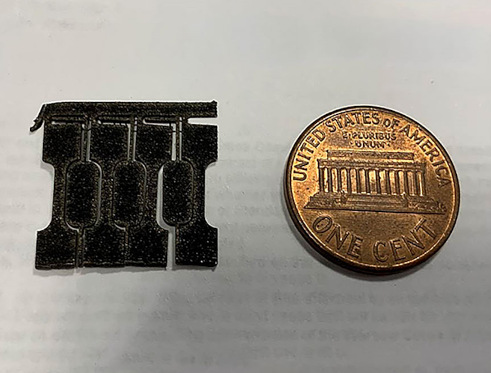
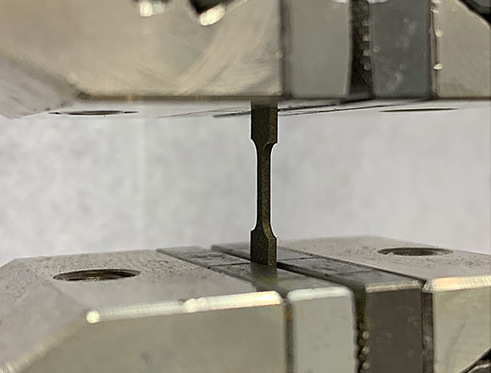
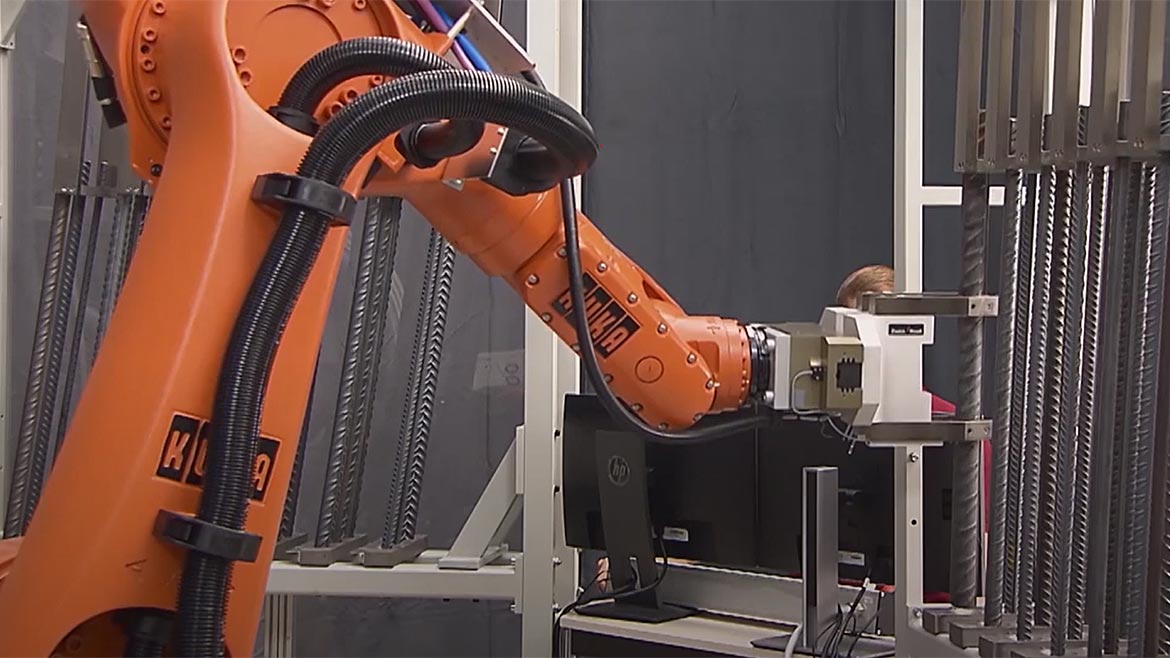
In addition to specimen sizes, expansion of testing application types and other handling functions to be automated have also expanded dramatically. The next applications added to the automation toolbox were hardness, surface roughness, pendulum and drop weight impact, and testing at high and low temperatures with robots feeding samples into temperature chambers with additional magazines. In many cases, these multiple test applications are combined in a single automation cell with one or more smart robots.
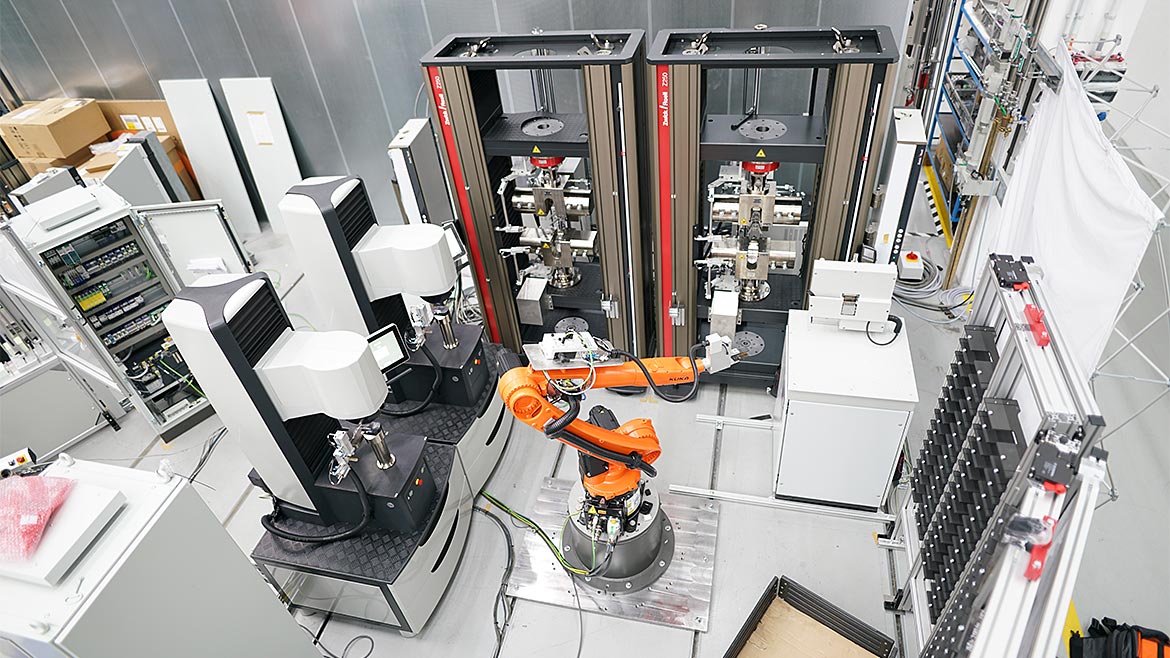
The next logical step was to look one step back into the testing process – sample preparation. In metals testing, this can mean a robot moving samples from a CNC milling machine to a magazine that is carried by an AGV (Automatic Guided Vehicle) to a tensile tester fed by another robot. For plastics testing, an automatic notch milling station can be integrated directly into a system with one or more Izod or Charpy impact testers. One can imagine that the data handling of such systems (typically facilitated by barcode or QR codes) is paramount.
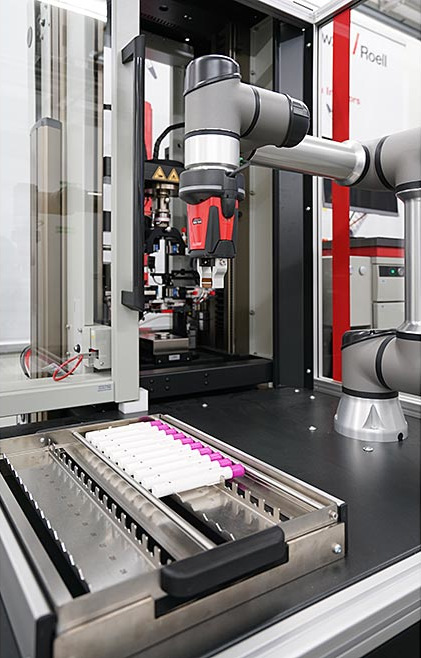
More recently, systems are being deployed that can do much more. They, for example, automatically measure rib geometry on rebar, verify temperatures, and package and label broken specimen. In the medical device industry, automated systems are running full functional tests on autoinjectors, providing the benefit of secure, traceable test results by removing the possibility of operator manipulation or simple mistakes. Today’s technology is suited to these complex systems but it’s true that the more elements in a system and the more variation in specimen type and geometry, the more a skilled operator may be preferred over a robotic solution.
So, therein lies the quandary: should a lab manager entrust many functions to their well trained and reliable staff, or to a robotic system that represents a significant investment and is perhaps not yet considered “mainstream.” Of course, the decision is made on a case-by-case basis. One important consideration is the actual availability of well trained and reliable staff, and the likelihood that they are willing to perform mundane tasks in the lab like feeding samples into a testing machine for hours. Another factor is understanding the state of the art in automation systems—what is available and proven today, what are the current limitations, and what future opportunities do they present? As described above, there is a wide range of available and ever-growing possibilities to automate materials and component testing processes—solutions that have already been deployed and proven successful, supporting the fact that it quite often pays to “push the envelope.”